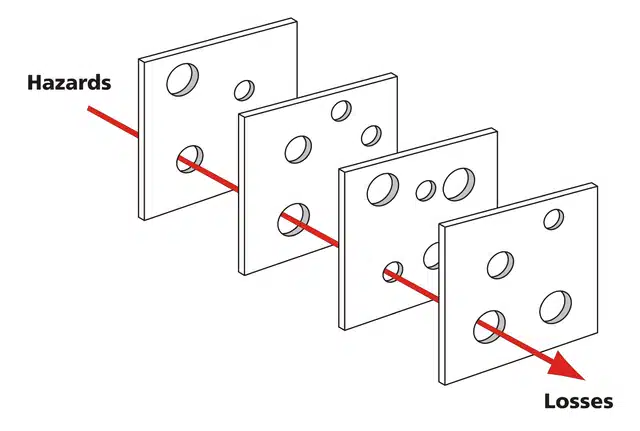
Ultimate Guide to Swiss Cheese Model and Its Applications
Reading Time: 7 minutes
With over two decades in business – spanning strategy consulting, tech startups, and executive leadership – I am committed to helping your organization thrive. At Reliability, we’re on a mission to help enhance strategic decision-making and operational excellence through the power of Root Cause Analysis, and I hope this article will be helpful! Our goal is to help you better
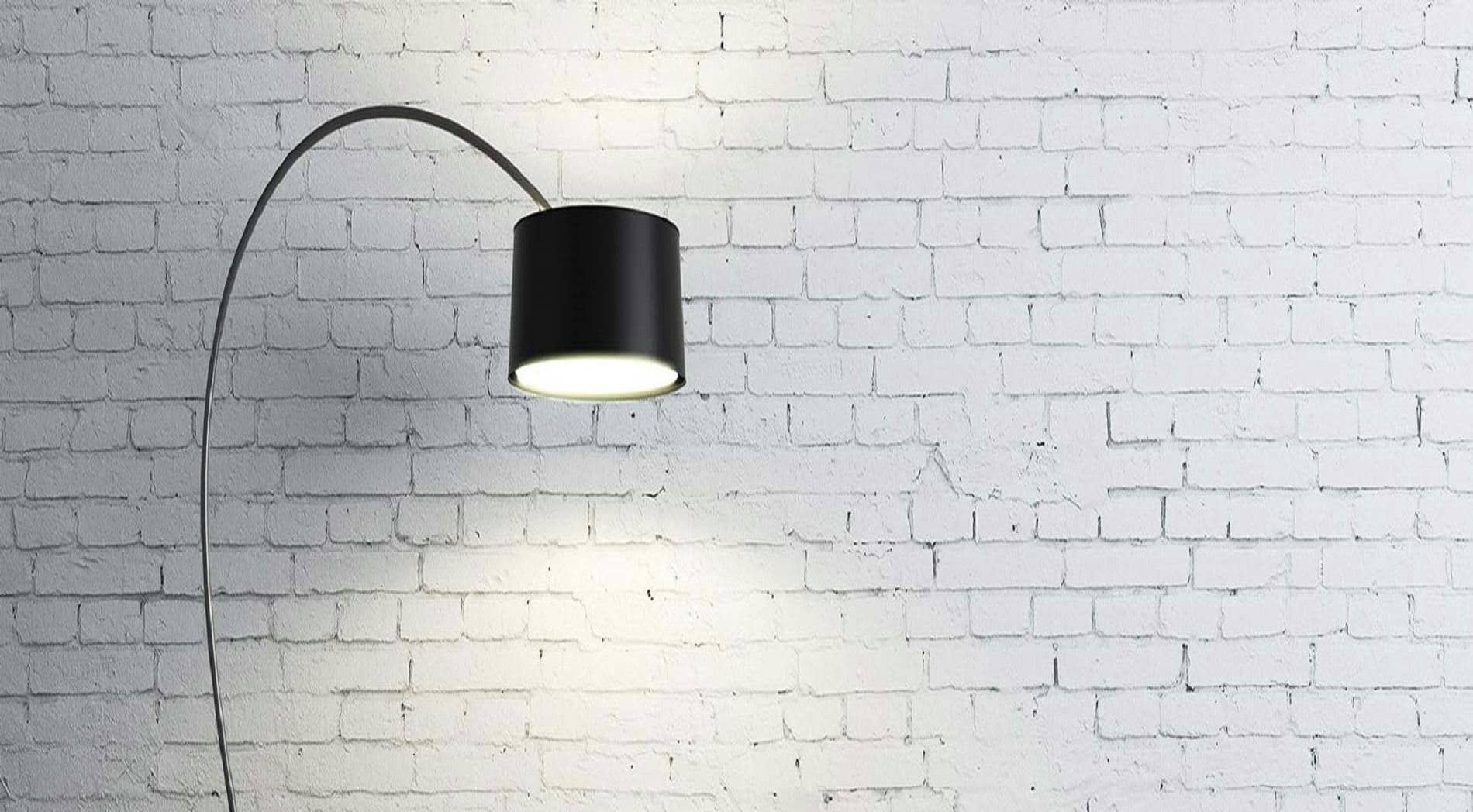
5 Root Cause Analysis Examples That Shed Light on Complex Issues
Reading Time: 7 minutes
With over two decades in business – spanning strategy consulting, tech startups, and executive leadership – I am committed to helping your organization thrive. At Reliability, we’re on a mission to help enhance strategic decision-making and operational excellence through the power of Root Cause Analysis, and I hope this article will be helpful! Our goal is to help you better
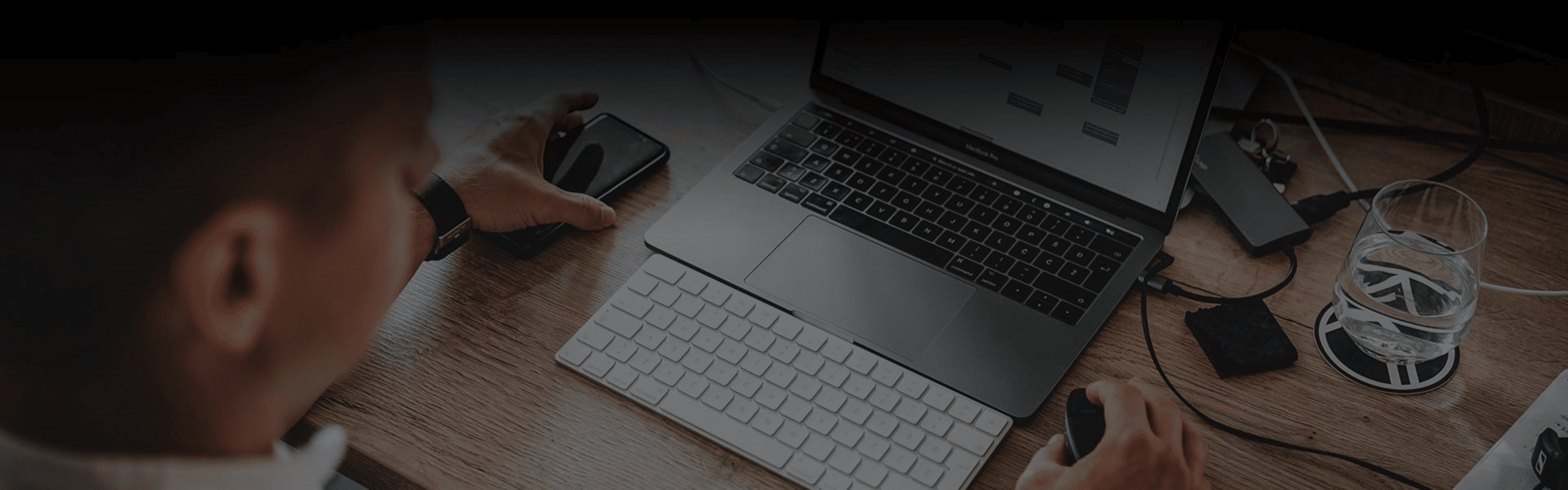
5 Whys Technique: Simple Steps to Find Real Problems (with examples and template)
Reading Time: 7 minutes
With over two decades in business – spanning strategy consulting, tech startups and executive leadership – I am committed to helping your organization thrive. At Reliability, we’re on a mission to help enhance strategic decision-making and operational excellence through the power of Root Cause Analysis, and I hope this article will be helpful! Our goal is to help you better
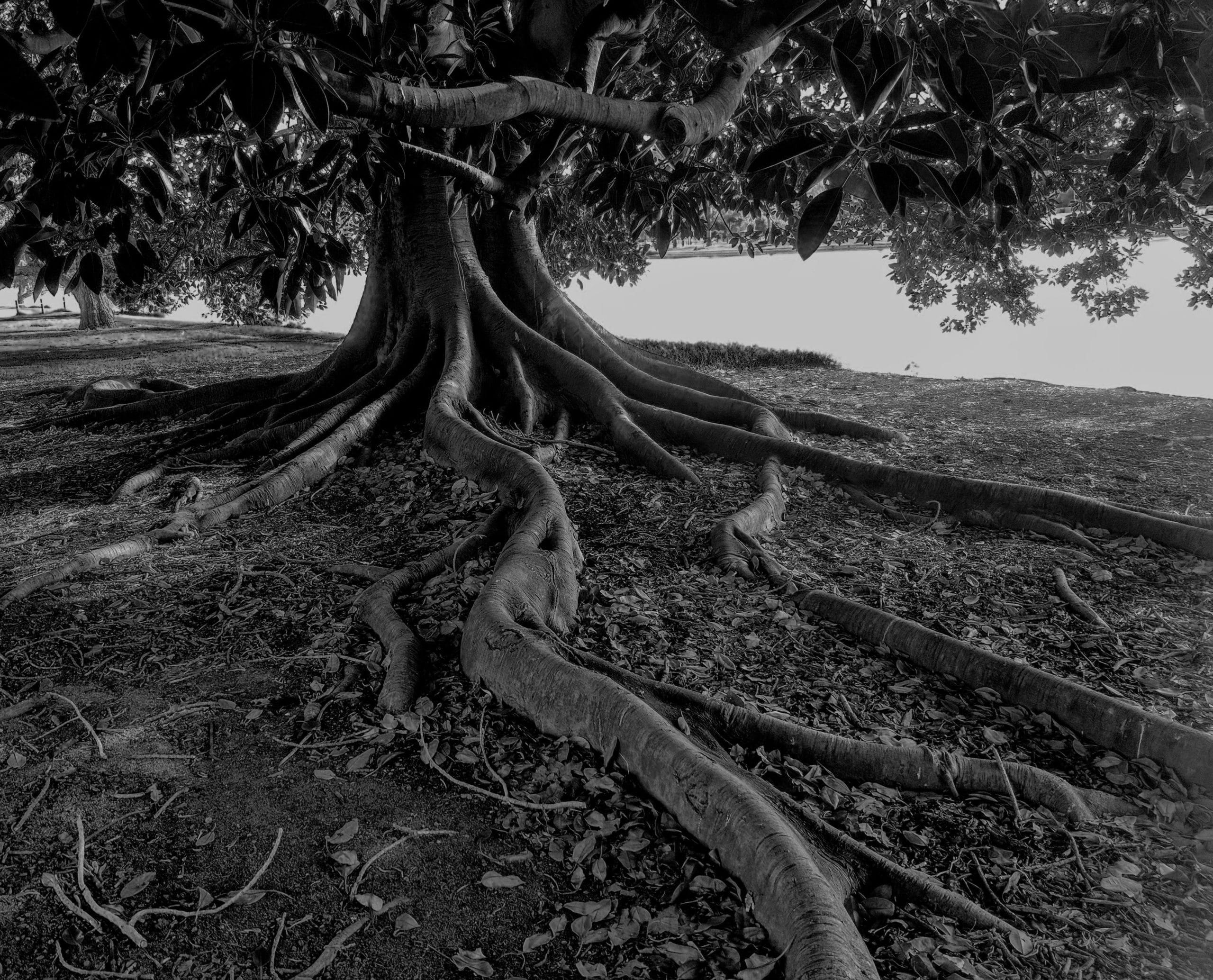
Fault Tree Analysis (FTA) Guide: Process, Symbols & Examples
Reading Time: 7 minutes
With over two decades in business – spanning strategy consulting, tech startups and executive leadership – I am committed to helping your organization thrive. At Reliability, we’re on a mission to help enhance strategic decision-making and operational excellence through the power of Root Cause Analysis, and I hope this article will be helpful! Our goal is to help you better
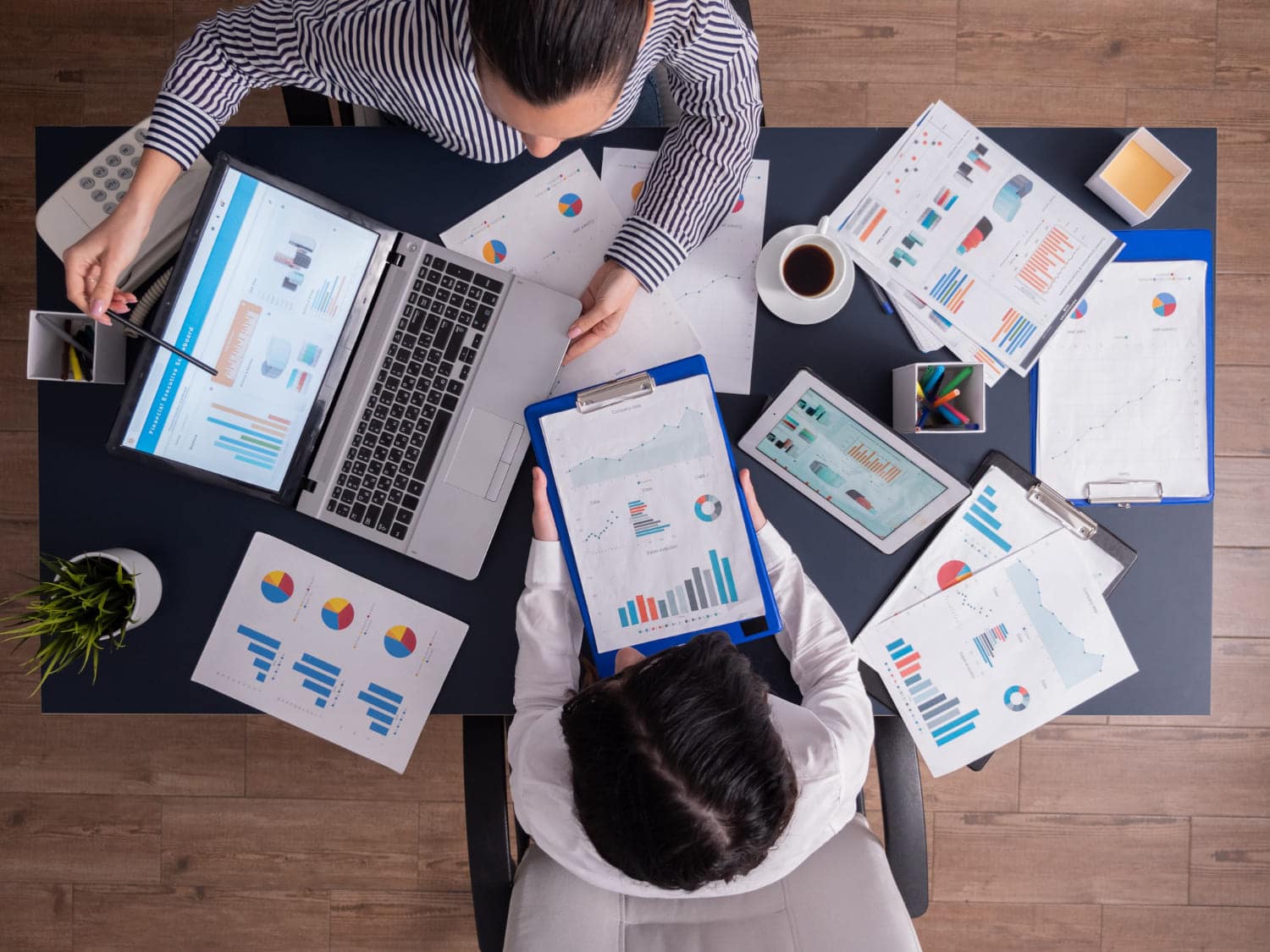
FMEA Guide: Failure Mode and Effects Analysis in Root Cause Analysis
Reading Time: 7 minutes
Dealing with potential failures and mitigating their impacts forms the core of reliability engineering. FMEA, also known as Failure Mode and Effects Analysis is a root cause analysis method that provides a path to improved reliability and enhanced performance. With over two decades in business – spanning strategy consulting, tech startups and executive leadership – I am committed to helping
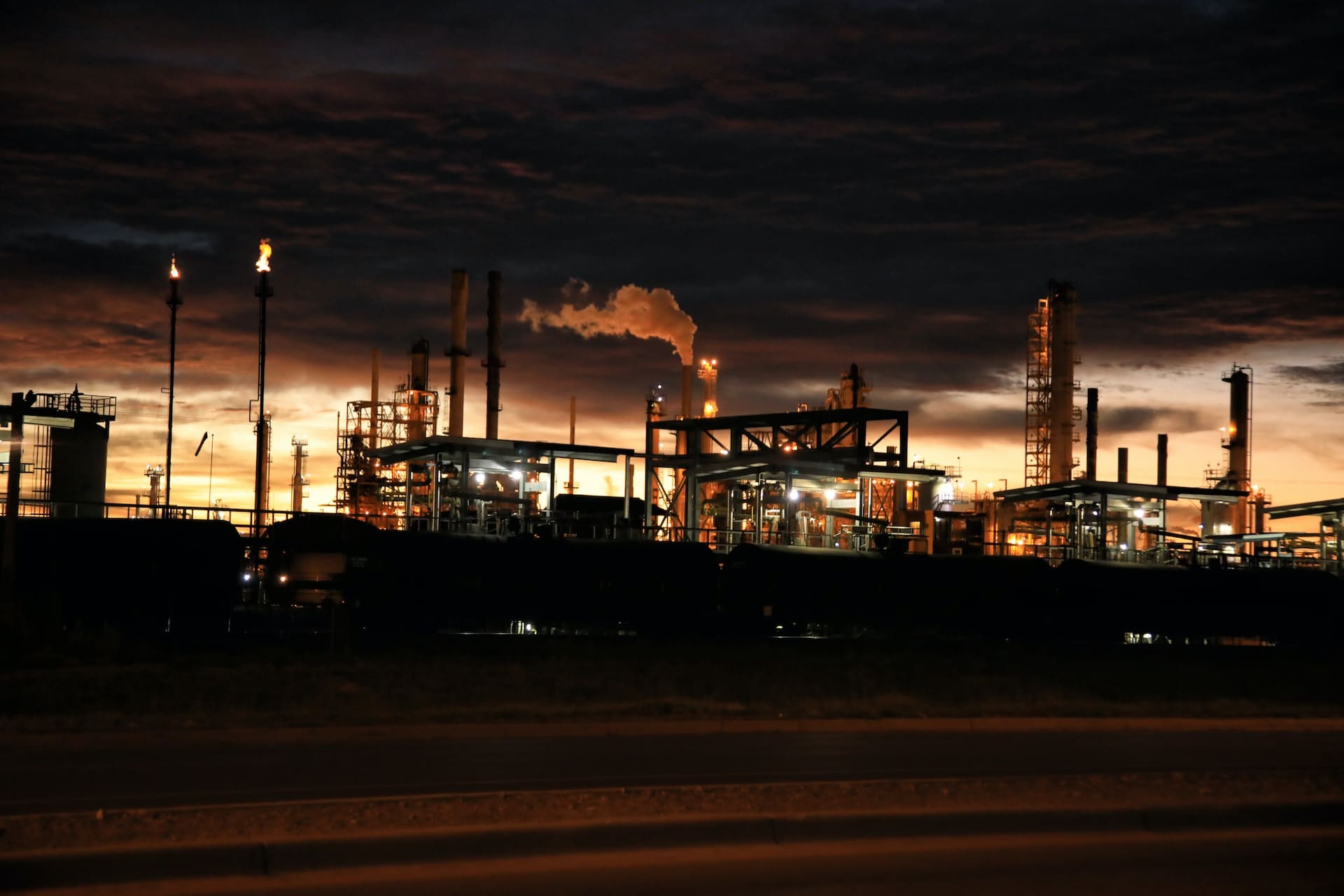
7 Powerful Root Cause Analysis Techniques and Tools
Reading Time: 5 minutes
With over two decades in business – spanning strategy consulting, tech startups and executive leadership – I am committed to helping your organization thrive. At Reliability, we’re on a mission to help enhance strategic decision-making and operational excellence through the power of Root Cause Analysis, and I hope this article will be helpful! Our goal is to help you better
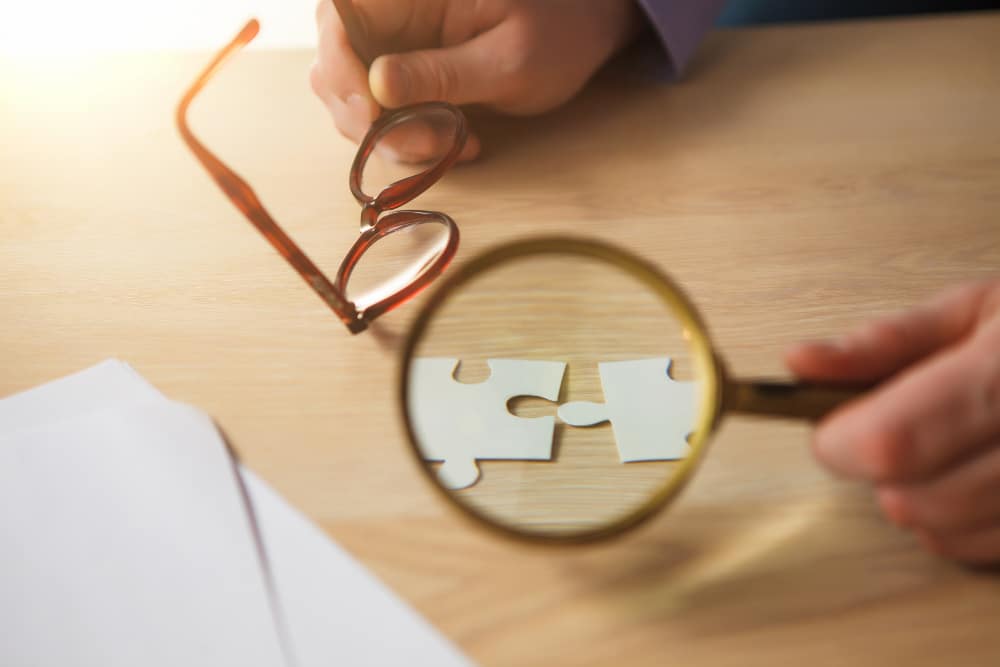
Understanding Failure Mechanisms and Components
Reading Time: 5 minutes
Understanding failure mechanisms and components is a critical aspect of reliability engineering, manufacturing, and maintenance across various industries. Whether you’re dealing with machinery, electronic devices, or complex systems, the ability to identify and comprehend how and why failures occur can significantly impact performance, safety, and longevity. This guide aims to delve into the intricacies of failure mechanisms and the components
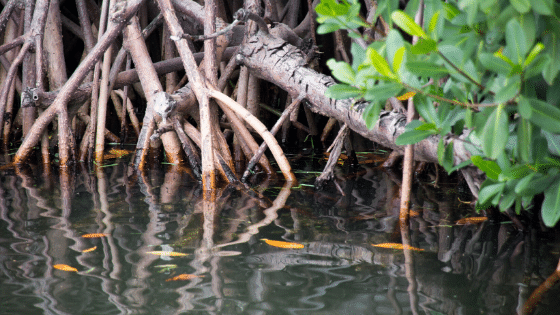
What’s Wrong With The Term “Root Causes”?
Reading Time: 2 minutes
There is great variation when it comes to a common understanding of the term ‘Root Cause Analysis’ or RCA. In a previous, lengthy paper, I wrote an article entitled “The Stigma of RCA: What’s In a Name?“. It focused on common understandings (or misunderstandings) of what RCA means and then described the basic steps of any investigative occupation. I just
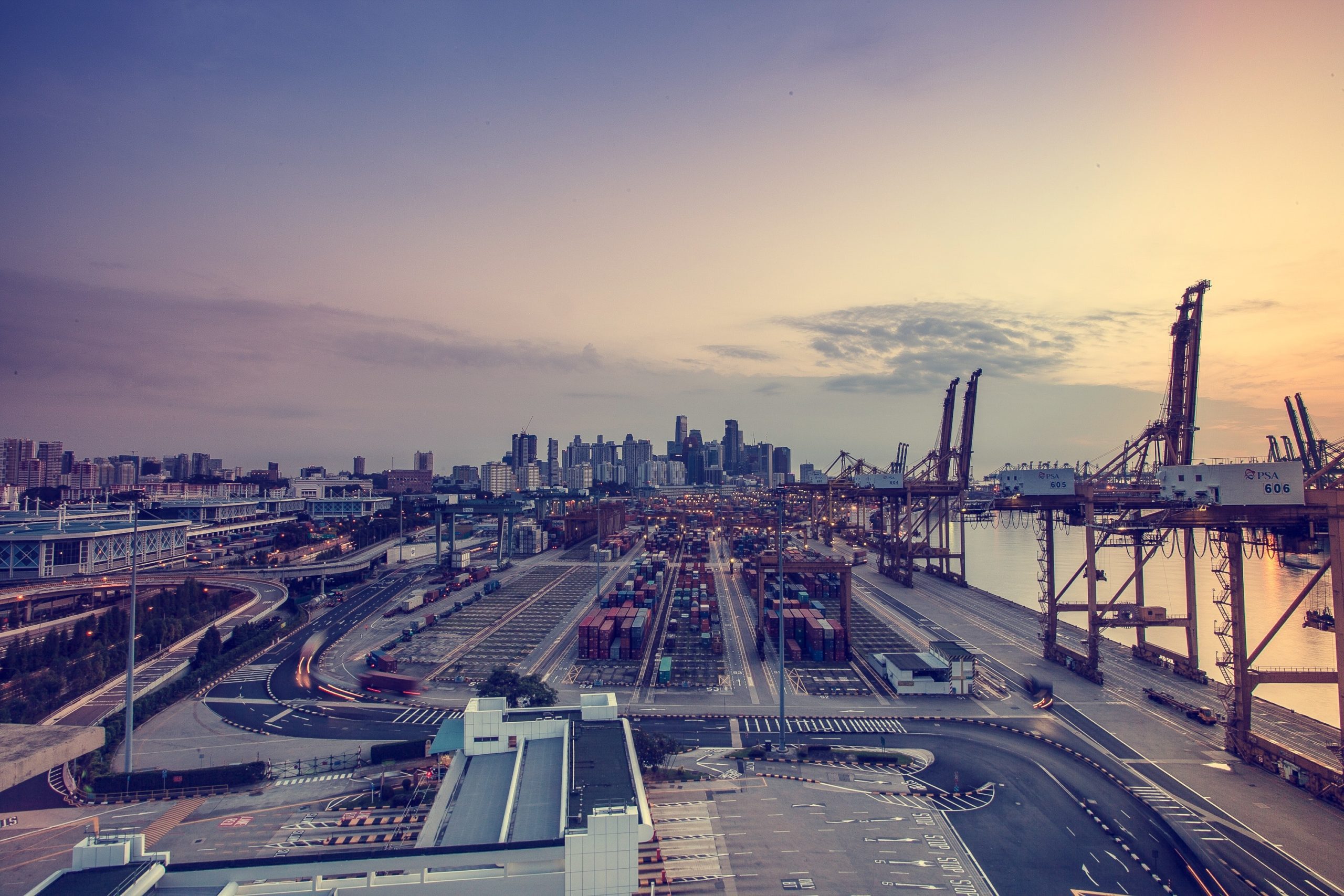
The Stigma of RCA: What’s in a Name?
Reading Time: 4 minutes
The Stigma of ‘RCA’ Let’s start off with some honesty…the term ‘RCA’ (Root Cause Analysis) is quite vague, misleading and easily misinterpreted by those who are not immersed in its use. It is a useless and counter-productive term because there is no universally accepted, standard definition. Therefore, any process/tool someone is using to solve a problem is likely to be labelled as
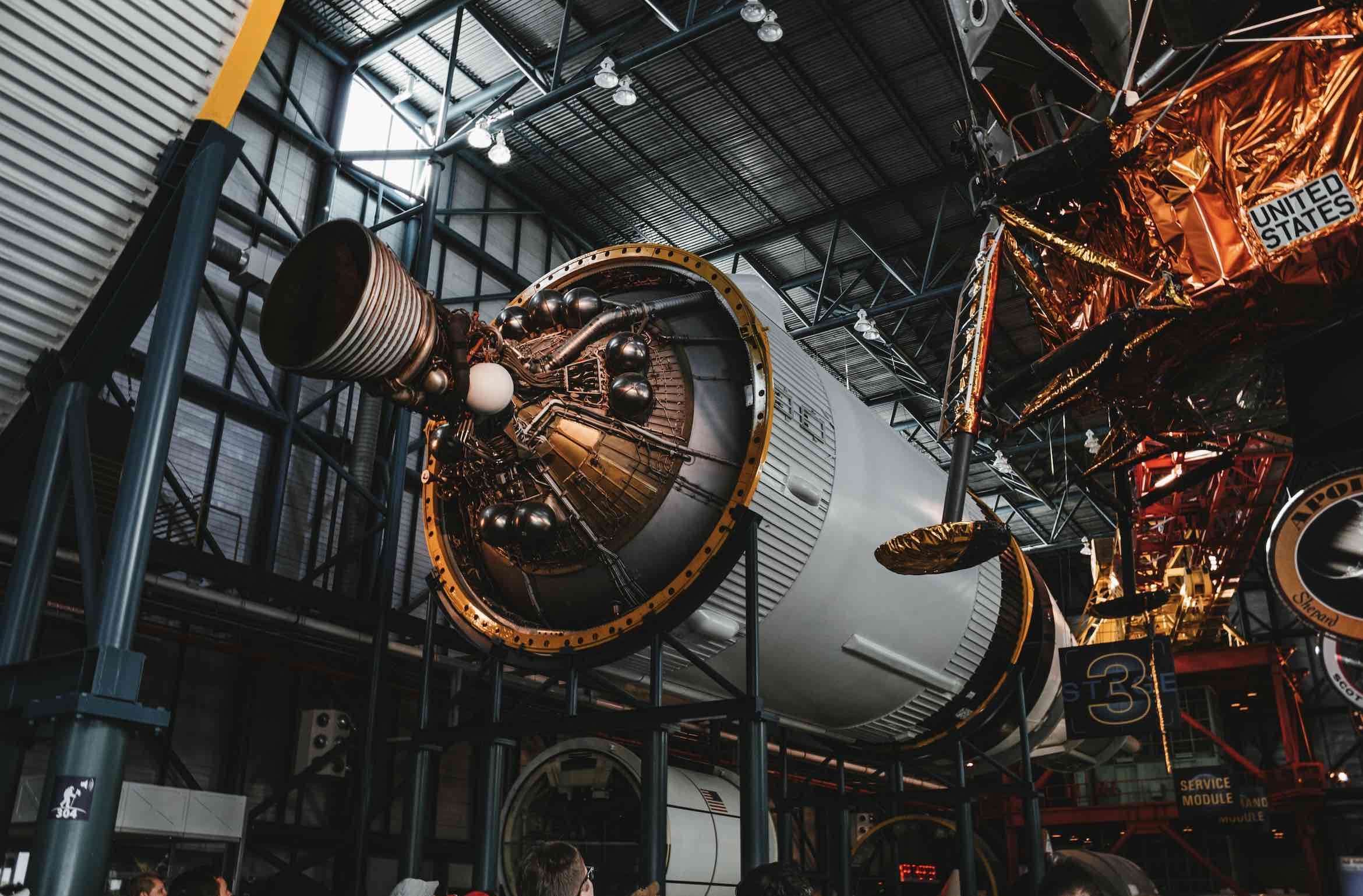
RCA in Action: The Space Shuttle Columbia Investigation
Reading Time: 3 minutes
As is typical in our manufacturing organizations, oftentimes it takes high visibility events with catastrophic consequences for a full-blown Root Cause Analysis (RCA) to be conducted. Many of us still have fresh memories of Challenger in our minds from over 17 years ago, and now we are faced with another investigation of equal (if not greater) magnitude.
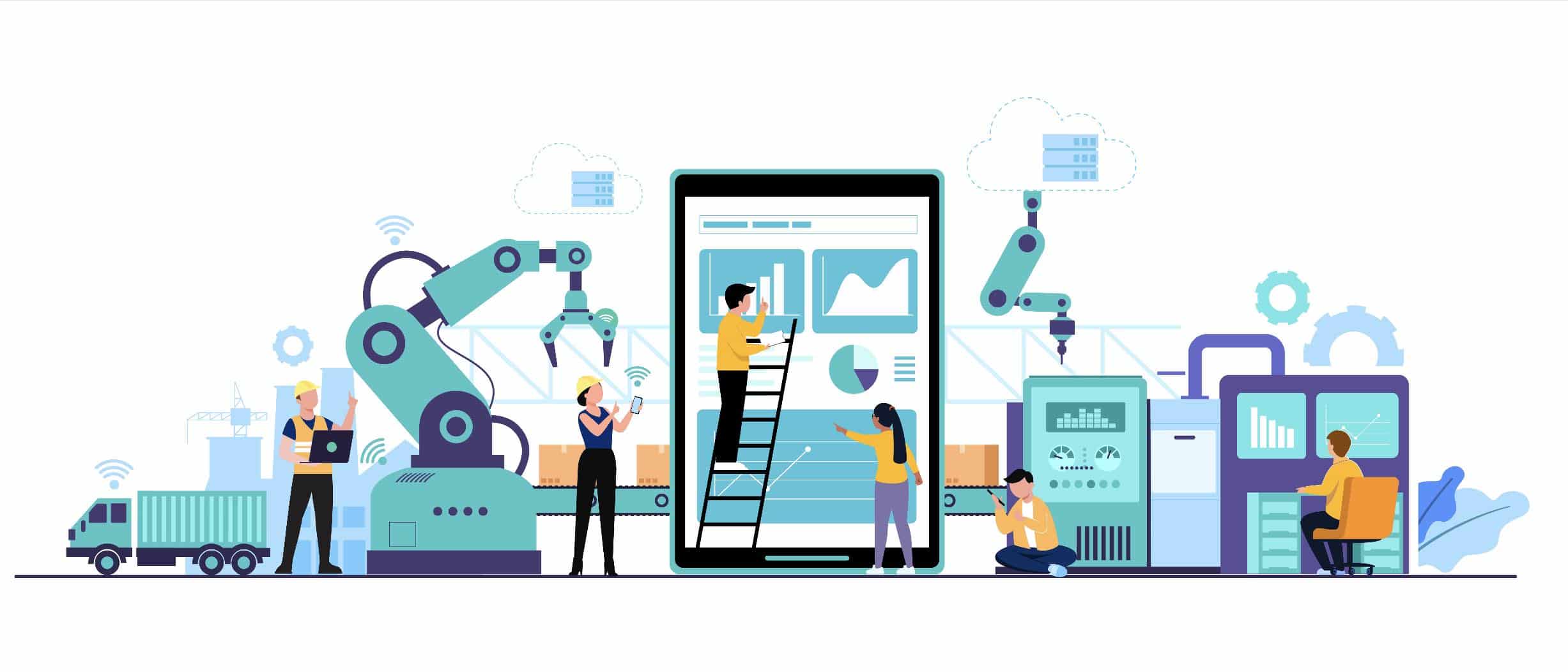
Root Cause Analysis Without Verification is Conventional Wisdom
Reading Time: 5 minutes
Root cause analyses are done every day all over the world. Organizations do root cause analysis because it is good business. From an explosion in an auto parts plant to the wrong prescription being given to a patient. Events such as these can have dramatic monetary, physical and psychological effects on an organization. To solve problems down to the true
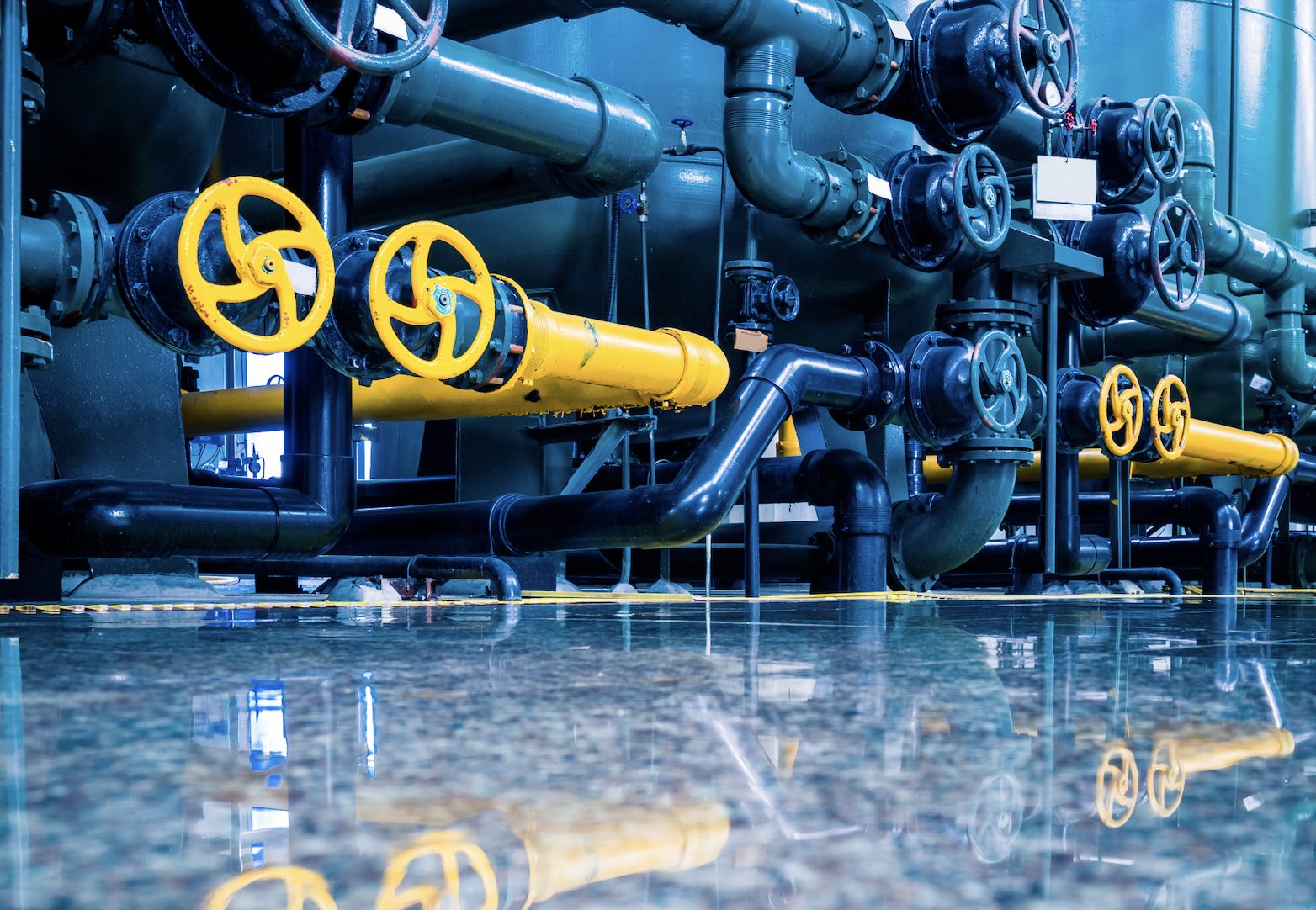
Hidden Treasure: Eliminating Chronic Failures Can Cut Maintenance Costs Up To 60%
Reading Time: 4 minutes
Every year, U.S. industry spends well over $300 billion on plant maintenance and operations. An estimated 80% of these dollars are expended to correct chronic failures of machines, systems, and people that occur daily, even hourly, in plants across the country.