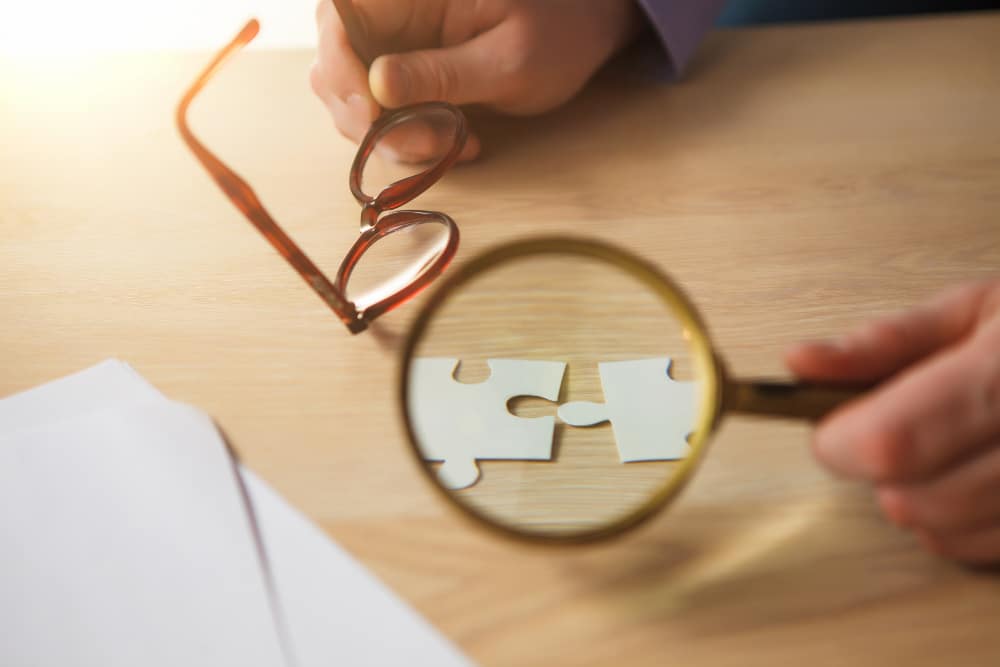
Understanding Failure Mechanisms and Components
Understanding failure mechanisms and components is a critical aspect of reliability engineering, manufacturing, and maintenance across various industries. Whether you’re dealing with machinery, electronic devices, or complex systems, the ability to identify and comprehend how and why failures occur can significantly impact performance, safety, and longevity.
This guide aims to delve into the intricacies of failure mechanisms and the components most susceptible to them. By gaining a thorough understanding of these elements, professionals can make informed decisions, improve system reliability, and take proactive steps to mitigate risks.
What are the 4 failure mechanisms?
Mechanical Failures
Mechanical failures often occur due to stress, fatigue, and corrosion. These can be further broken down into:
- Fracture: A fracture occurs when a material breaks or cracks due to an applied force. This can happen suddenly or develop over time due to fatigue.
- Fatigue: Fatigue is the weakening of a material caused by repeated cycles of stress. Over time, this can lead to cracks and ultimately, failure.
- Corrosion (wear): Wear is the gradual removal of material from a surface due to mechanical action, such as friction or abrasion.
Bridge Collapse Due to Metal Fatigue Scenario: A well-known bridge collapsed during rush hour, causing numerous casualties. Mechanism: Metal fatigue in the support beams. Analysis: Engineers found that the support beams had undergone repeated stress cycles over the years, weakening the metal and leading to fatigue cracks. Prevention: Regular inspections and material testing could have identified the weakening beams, allowing for timely replacement or reinforcement. |
Material Failures
Material failures are often caused due to poor quality, defects, or incompatibility with the environment. For instance, using a material that is not resistant to high temperatures in an environment where it will be exposed to heat or degrade faster than expected is a recipe for failure.
Material Failure in Water Pipes Scenario: A city faced a water contamination crisis. Mechanism: Corrosion in old iron pipes. Analysis: The iron pipes had corroded over time, leaching into the water supply. Prevention: Using corrosion-resistant materials or applying anti-corrosion coatings could have prevented the issue. |
Process-Related Failures
These are failures that occur due to issues in the manufacturing or operational process. For example, if a machine is not calibrated correctly, it can lead to the failure of its components.
Pharmaceutical Product Contamination Scenario: A batch of a pharmaceutical product was recalled due to contamination. Mechanism: Failure in the sterilisation process. Analysis: The sterilisation process was not carried out correctly, leading to bacterial contamination. Prevention: Strict adherence to sterilisation protocols and regular equipment checks could have prevented the contamination. |
Human-Induced Failures
Sometimes, failures occur due to human error, such as poor maintenance or incorrect operation of machinery.
Airplane Crash Due to Pilot Error Scenario: An airplane crashed shortly after takeoff, resulting in loss of lives. Mechanism: Pilot error. Analysis: The pilot incorrectly interpreted the flight data, leading to wrong manoeuvres. Prevention: More rigorous training and better-designed user interfaces for flight systems could mitigate the risk of such errors. |
How does understanding the components help us succeed?
Understanding the components involved in a system is equally important. Each component has its own set of failure mechanisms, and understanding these can help in better system design and maintenance. It allows you to examine what worked or what didn’t even more so than success. It can foster your critical and analytical thinking skills, allowing you to innovate, redirect and try another way to execute something the next time.
Hardware Components:
In machinery, this could be gears, bearings, and electrical components. Regular maintenance checks can help prevent failure. Following are examples of hardware components that could be involved in a failure.
- Gears: Wear and tear can lead to misalignment or breakage. Lubrication and regular inspections can extend lifespan.
- Bearings: These are prone to fatigue and corrosion. Regular cleaning and lubrication can help.
- Electrical Components: Overheating and short-circuits are common issues. Ensuring proper electrical load and insulation can mitigate risks.
Software Components
Algorithms, databases, and user interfaces need to be robust and free of bugs to prevent software failure. The examples of softwarte components that can be involved are:
- Algorithms: Inefficient algorithms can lead to performance bottlenecks.
- Databases: Poorly managed databases can result in data loss or corruption.
- User Interfaces: Bugs in the UI can lead to poor user experience and potential operational errors.
Material Components
The quality of materials used in construction or manufacturing can significantly impact the likelihood of failure.
- Metals: Susceptible to corrosion and fatigue.
- Plastics: May degrade over time, especially when exposed to UV light or chemicals.
- Composites: Can delaminate or suffer from internal stresses.
Human Components
Training and oversight can reduce the risk of human error, which is often a significant component in failure.
- Training: Lack of training can result in operational errors.
- Oversight: Lack of supervision can lead to mistakes going unnoticed.
- Fatigue: Overworked staff are more likely to make errors.
Process Components
The steps involved in manufacturing or any operational chain can be points of failure if not adequately managed.
- Workflow: Inefficient workflows can lead to bottlenecks and errors.
- Quality Control (QC): Lack of QC steps can result in defective products.
- Documentation: Poor documentation can lead to misunderstandings and errors.
How can failure be prevented?
Understanding failure mechanisms and components is not just about identifying what went wrong but also about taking steps to prevent future failures. Understanding failure mechanisms and components is indeed the first step towards preventing future failures.Here are some preventive measures after understanding the failure mechanisms and components involved:
Regular Maintenance
- Scheduled Inspections: Regularly inspect all components for signs of wear, corrosion, or other potential issues.
- Predictive Maintenance: Utilise data analytics and machine learning to predict when a component is likely to fail, allowing for timely replacement or repair.
- Calibration: Ensure that all measurement devices are calibrated correctly to prevent errors that could lead to failure.
Benefits of Regular Maintenance: Extends the lifespan of machinery and components.Reduces the likelihood of unexpected breakdowns.Saves costs in the long run by preventing catastrophic failures. |
Quality Control
- Material Testing: Conduct tests on materials to ensure they meet the required standards for strength, durability, and other relevant metrics.
- Batch Sampling: Randomly sample components from each production batch for quality assurance tests.
- Supplier Audits: Conduct regular audits of suppliers to ensure their products meet your quality standards.
Benefits of Quality Control: Ensures that all components are up to standard, reducing the risk of failure.Builds customer trust by ensuring a high-quality end product.Helps in identifying issues at the source, making it easier to implement corrective measures. |
Proper Design
- Failure Modes and Effects Analysis (FMEA): Use FMEA to identify potential failure modes and design features to mitigate them.
- Redundancy: Design backup systems or components that can take over in case of a failure.
- Safety Margins: Design systems to operate safely under conditions more extreme than they are likely to encounter.
Benefits of Proper Design: Reduces the risk of failure by designing with potential failure modes in mind.Enhances system reliability by incorporating backup systems.Provides a buffer against unexpected stressors or operating conditions. |
By combining these preventive measures, you can create a comprehensive strategy for reducing the risk of failure in your systems. This not only improves reliability but also contributes to safety and efficiency, ultimately adding value to your end product or service.
How does Reliability engineering play a role in this process?
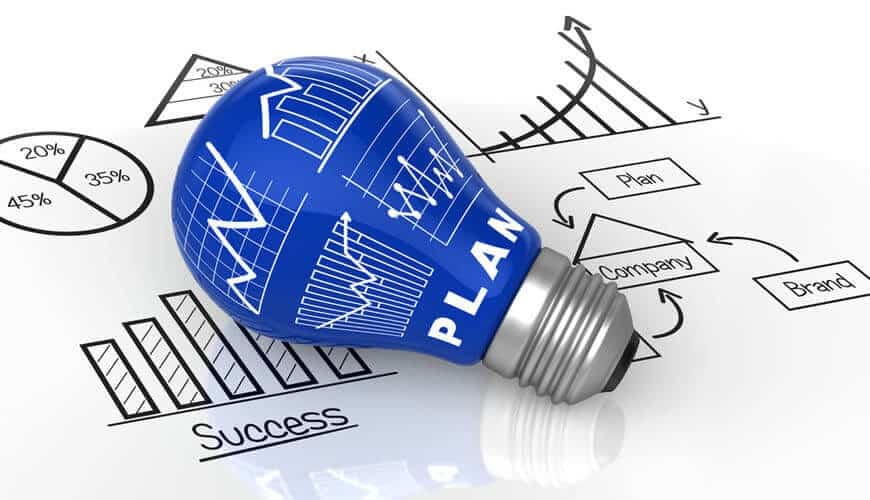
Reliability engineering plays a crucial role in enhancing system robustness, reducing failures, and ensuring efficient operations. Here are the three key aspects of reliability engineering can help with failure mechanisms and components:
System Design and Risk Prioritisation
Reliability engineering starts at the conceptual stage, incorporating robust design features that mitigate potential failure modes. Tools like Failure Modes and Effects Analysis (FMEA) are used to identify and prioritise risks, ensuring that the system is inherently more reliable from the outset.
Data-Driven Maintenance and Prediction
By applying statistical models to historical and real-time data, reliability engineering can accurately predict when a component is likely to fail. This data-driven approach enables timely preventive maintenance, reducing downtime and extending the lifespan of components.
Continuous Improvement and Compliance
Reliability engineering is an ongoing process that involves continuous monitoring and root cause analysis. This not only helps in updating reliability models but also ensures that systems remain compliant with industry regulations, thereby reducing legal risks and improving overall quality.
Reliability engineering provides a comprehensive framework for designing more robust systems, enabling data-driven maintenance strategies, and facilitating continuous improvement and regulatory compliance.
Recent Posts
UK Retail Cyberattacks: What M&S, Harrods & Co-op Reveal About Cybersecurity and Root Cause Analysis
Richmond Water Crisis Exposes Infrastructure Vulnerabilities: Why RCA Is Key to Long-Term Solutions
Introducing RCA Turbo: Instant Root Cause Analysis with a Snap or a Sentence
Unpacking the Iberian Peninsula Blackout: How Root Cause Analysis Can Illuminate Grid Vulnerabilities
Root Cause Analysis Software
Our RCA software mobilizes your team to complete standardized RCA’s while giving you the enterprise-wide data you need to increase asset performance and keep your team safe.
Root Cause Analysis Training