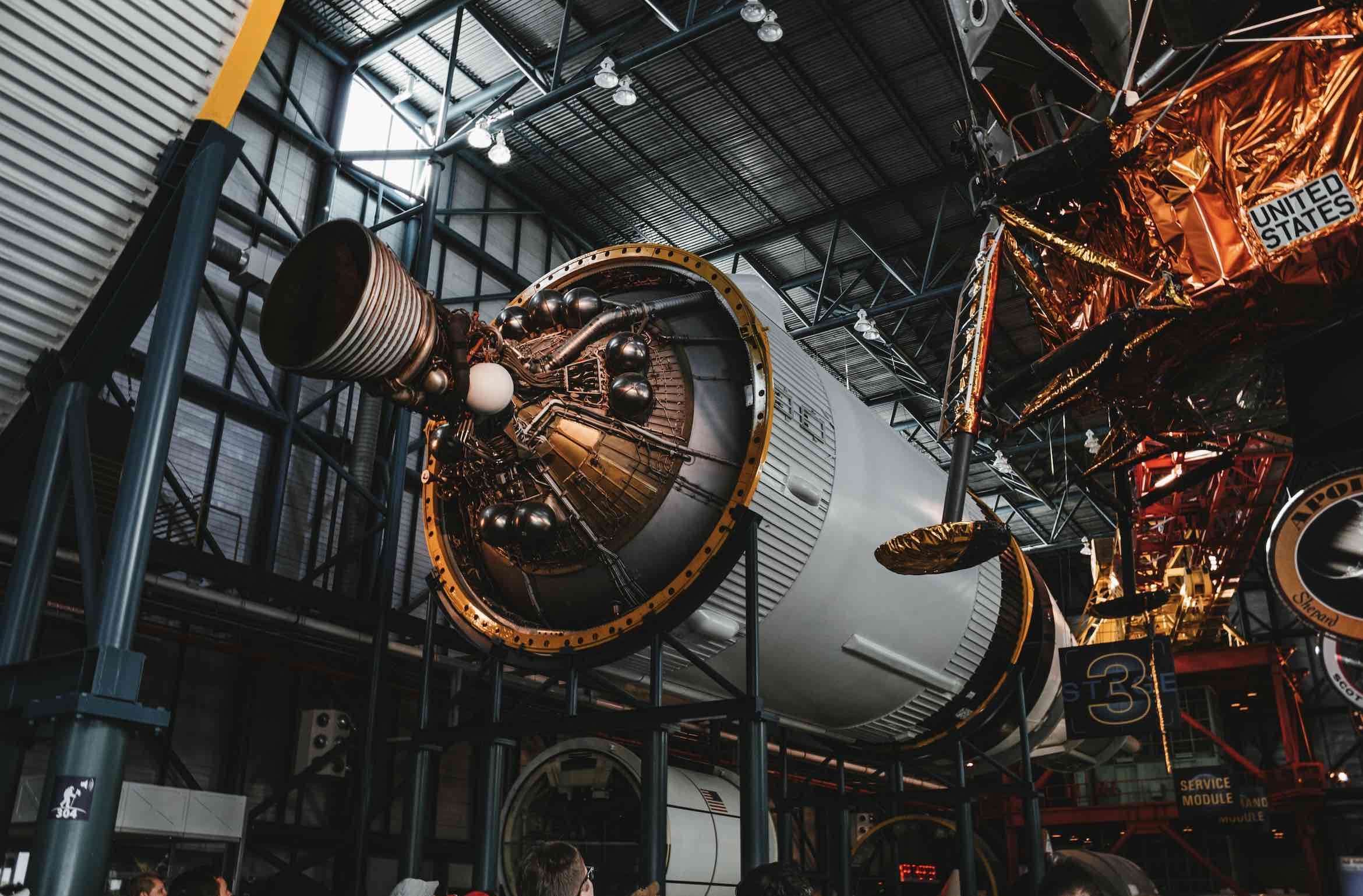
RCA in Action: The Space Shuttle Columbia Investigation
As is typical in our manufacturing organizations, oftentimes it takes high visibility events with catastrophic consequences for a full-blown Root Cause Analysis (RCA) to be conducted. Many of us still have fresh memories of Challenger in our minds from over 17 years ago, and now we are faced with another investigation of equal (if not greater) magnitude.
We can watch this investigation unfold in the media, as those unfamiliar with the technical approach of RCA clamor for answers as to the cause. The public appetite for information is a significant pressure on such an investigation. However, the investigators know they must stick to the discipline of the investigation method if their results are to be factual and credible.
This was clearly evidenced in Ron Dittemore’s (Shuttle Program Manager) comments below:
“DITTEMORE: I have been very careful through this entire week not to draw conclusions. It’s a very tempting thing to do. You want to draw conclusions as quick as you can based on the information. And I know you; many of you have succumbed to that temptation also.
But you can’t do that. We have been in this business long enough to know that you go down that merry path of making a judgment or a rush to judgment and you will be fooled. You need to go through the process. You need to gather the data. You need to correlate all the data, the time frames, the evidence, the photos, the way the system behaved. And you need to do it under the scrutiny of a microscope for you to get the right answer.
And even though it’s a temptation for us to try to make a judgment, our experience has shown that you should not. And we will not until we get all the data together and are able to come tell you what we believe this information represents as far as a root cause(s). “
This statement should be etched in every analyst’s memory, as it depicts the correct way to conduct such an investigation. For some reason, the media and the general public believe that there is always one (1) cause to such events. They do not realize that there is a sequence of events that occur in series and parallel that form a “chain” until the undesirable outcome occurs. These series of events require extensive data collection in order to prove or disprove various hypotheses. RCA is nothing short of the scientific method used in uncommon circumstances.
Part of the public’s perception of this one (1) cause paradigm has to come from the media’s portrayal of such events. Think back to Challenger, all that most of the public remembers was something about the O-rings. They did not hear as often about the poor decisions that were made due to the pressures that were there that day in order to launch. The public did not hear as often about the fact that the O-ring design deficiency was known about for years and was evidenced on 15 of the previous 25 missions at that time.
ROOT cause analysis involves getting past physical roots and understanding why bad decisions are made that lead to such events.
Columbia is no doubt another tragedy in American space history, but as in the past we must use these tragedies to learn from and to prevent similar occurrences in the future. Whether we work in a manufacturing plant, a hospital or at NASA, the fact remains that we are all humans working in different systems. Because the human is flawed, we are not error-free. It is hard to believe that those that cast stones so early in the investigation have not been guilty of similar poor decision making in the past no matter what organization they work in!
As in all TRUE investigations, let the facts guide the analysis not the public demand for quick answers.
About the Author
Robert (Bob) J. Latino is former CEO of Reliability Center, Inc. a company that helps teams and companies do RCAs with excellence. Bob has been facilitating RCA and FMEA analyses with his clientele around the world for over 35 years and has taught over 10,000 students in the PROACT® methodology.
Bob is co-author of numerous articles and has led seminars and workshops on FMEA, Opportunity Analysis and RCA, as well as co-designer of the award winning PROACT® Investigation Management Software solution. He has authored or co-authored six (6) books related to RCA and Reliability in both manufacturing and in healthcare and is a frequent speaker on the topic at domestic and international trade conferences.
Bob has applied the PROACT® methodology to a diverse set of problems and industries, including a published paper in the field of Counter Terrorism entitled, “The Application of PROACT® RCA to Terrorism/Counter Terrorism Related Events.”
Recent Posts
UK Retail Cyberattacks: What M&S, Harrods & Co-op Reveal About Cybersecurity and Root Cause Analysis
Richmond Water Crisis Exposes Infrastructure Vulnerabilities: Why RCA Is Key to Long-Term Solutions
Introducing RCA Turbo: Instant Root Cause Analysis with a Snap or a Sentence
Unpacking the Iberian Peninsula Blackout: How Root Cause Analysis Can Illuminate Grid Vulnerabilities
Root Cause Analysis Software
Our RCA software mobilizes your team to complete standardized RCA’s while giving you the enterprise-wide data you need to increase asset performance and keep your team safe.
Root Cause Analysis Training