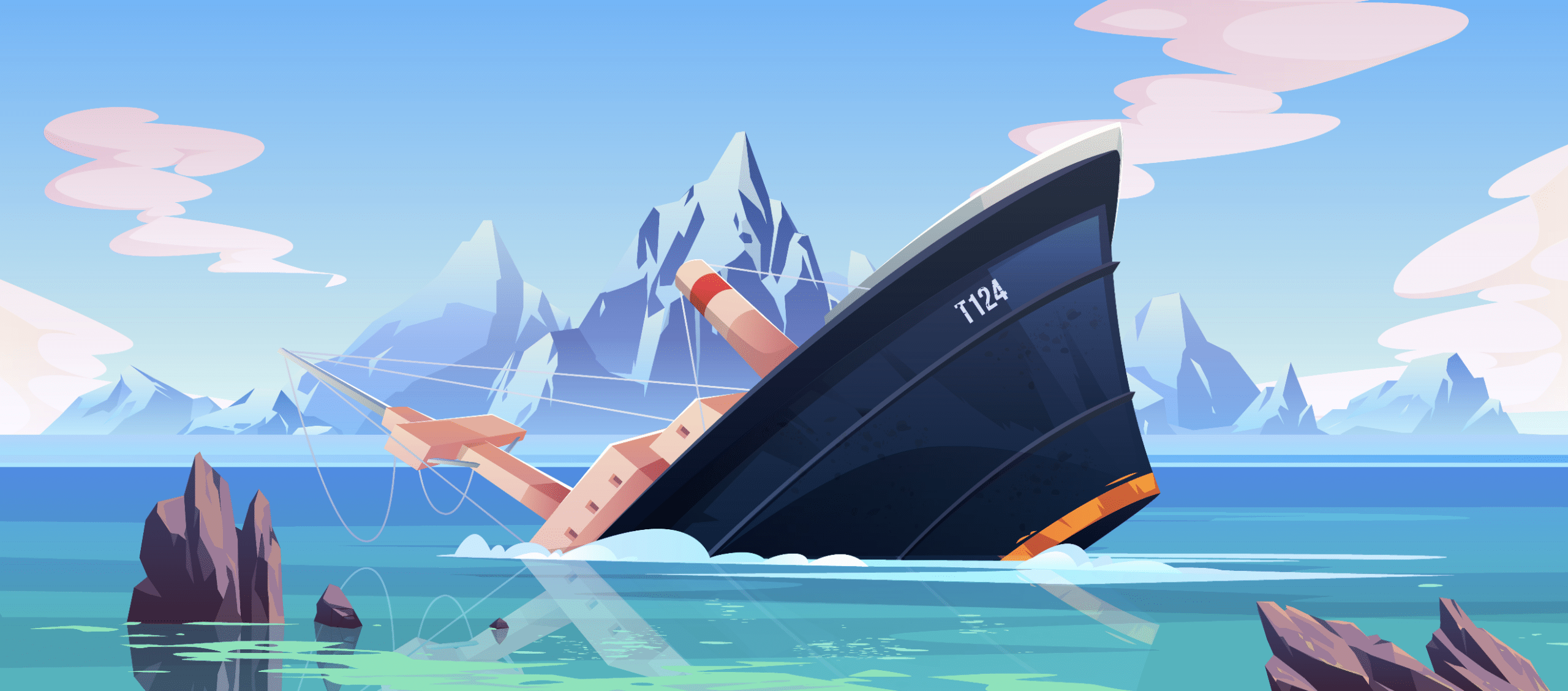
The best organizations in the world are not the ones with all the systems and procedures, all the acronyms, or even the most up to date technical solutions; instead they are the ones that are best at identifying and solving problems. Want more success? Want a better maintenance effort? Then get better at finding and solving problems.
I want to dissect the famous case of the sinking of the Titanic and show how problems, even horrible, tragic ones can be pointers to areas where some attention would improve the process, product or company before we can delve into what we have to look at how things go wrong.
We all have been told that accidents are not accidental and that mistakes are only as consequential as the design allows them to be.
Accidents are almost always a series of events (sometimes an improbable series) that add up to the accident. The string of events might look like this: The pedestrian was wearing black at night, it was rainy, the tires were bald, the driver was tired, the driver was late for a delivery, and at that moment he changed stations on the radio the pedestrian tripped on a log and fell toward the street. What we say is that if any of those circumstances were different, avoided or mitigated, the accident might not have happened.
What about the consequences of an event? If we blow an engine on most interstates, we can steer onto the shoulder and slow, then stop the rig. In most cases, there will be no loss of life or additional loss of property (beyond the engine).
But what if the engine powers a Piper 175 (single-engine)? Or what if the engine fails in a hospital’s backup generator during a power outage? Then the consequences are dire. Our design’s multiple levels of robustness are what protect us from harm. The hospital’s generator has frequent PMs and extensive annual work to make sure it starts and runs. The Piper has redundancy in the systems that could be a source of failure (ignition, fuel pumps, etc.). An airplane has what is said to be a defense in depth. Many things have to go wrong for the plane to be lost. The Titanic lacked a defense in depth and suffered a series of catastrophic problems.
But how are problems good? We’ll simplify the case to make it clear.
Everyone knows that we have policies and procedures that are outmoded, not followed accurately, not understood, mistaken, and ignored. Which ones of these are dangerous? Which ones of these that, if followed, would improve the safety or effectiveness of our businesses? Having a problem and determining the causes and effects answers some of these questions.
The Titanic was 882 feet 9 inches (269.1 m) long and 92 feet 0 inches (28.0 m) abeam, the tonnage 46,328, and the height from the water line to the boat deck of 59 feet (18 m). The Titanic was the largest ship of the day. Currently, for comparison, the Oasis of the Seas is the largest ship which displaces almost 225,282 tons.
April 14, 1912, The Titanic struck an iceberg and within hours sunk. Of a total of 2,223 people aboard only 706 survived and 1517 people perished and the ship was lost. The total lifeboat capacity was 1,178 people (which was more than the regulations at the time).
If we look at the causes, we can see engineering and design issues, procedure issues, lapses in judgment, and lapses in the laws and statutes that govern maritime affairs.
Of course, one complaint is that we have 20/20 hindsight. The same process could be used for any event happening today (to use the problem to improve our businesses). To see this, think of an airplane crash and the investigation which issues directives, changes to procedures that occur. The second complaint which is probably true, is that our advanced technology tells us things that would not have been known in 1912. Also, us knowing that the ship sank gives us an edge. The truth is that our solutions might not have even occurred to the people of that era.
At 11:40 PM, the ship hit the iceberg with a glancing blow to the starboard side which caused buckling in the hull plates along with the first five compartments. The seams of the plates popped open (only an inch or two) for almost 300 feet. The length of the slice allowed water to rush in.
Metallurgists say that the plates were brittle at the low temperatures of the North Atlantic, and a different alloy would have been able to take the stress of the slicing blow against the iceberg. Other Metallurgists say that the rivets were substandard (rivets that were retrieved from the wreck were occluded with slag) and had they bought and installed suitable rivets correctly, the plates would have held. Let’s accept them as among the causes.
Experts say that two major design flaws saved money in the manufacture. One was the walls of the watertight compartments did not extend to the ceiling. They were well above the water line and no one thought that would be an issue. It turned out to be pivotal in the speed of the sinking.
The second piece of dicey engineering was the size of the rudder. The ship had a rudder designed for a much smaller ship. After the iceberg watch called out (the watch was late in seeing the iceberg) that there was an iceberg to the starboard, the ship started to turn but couldn’t turn fast enough to avoid the collision. The glancing blow was much worse than a straight head-on collision (which the ship could have survived). So we have two engineering causes.
Several procedures were causes to the accident. The first one was when the iceberg was sighted, the bridge called for reversing the engines. Only 2 of the three propellers could be reversed. That caused turbulence and cavitation. The small rudder located in the middle of this mess was rendered even more useless by all the turbulence. Ship experts say if the engines were just slowed, the rudder would have been adequate. The second issue is that on a maneuver like that, the bridge should have turned toward the iceberg at the last minute to bring the back of the ship out and around the berg.
Finally, we have the problem of seeing the iceberg too late. The ship was going like gangbusters to make its inaugural voyage a quick one. At 22 knots, it was thought that any icebergs big enough to hurt the ship would be seen well ahead of time. Two watches were in the crow’s nest without binoculars. Other ships of the day used iceberg watches on the ship’s bow. The Titanic captain didn’t think this was necessary.
There were other causes, but let’s stick to these few. The crazy thing is that if any of these (and other) causes had been eliminated or mitigated, the Titanic would be another big ship from the turn of the century. It would not have become famous. It would not have sunk or if it had there would have been enough time for a rescue.
The tragedy caused a firestorm of publicity, and inquiries were immediately started in both the US and England. The point is that the inquiries solved problems that were there but until this incident unrecognized. These problems left unexamined, would have resulted in possibly numerous tragedies. The findings and changes to the law, design and maritime procedures from the causes found by these inquiries have made traveling by ship an order of magnitude safer for everyone. In this way, the tragedy leads the way to a complete review of the vessel, its systems, and the whole maritime industry. Many problems were found and most were fixed.
Some of the problems of the Titanic were fixed by regulation and others by interested parties alerted to the existence and nature of the problem.
Problems & Solutions
- Steel alloy of plate -> Improved hull designs and major gains in Metallurgy solved the brittleness problem by WW1
- Waterproof compartments -> Improved bulkhead design (watertight to ceiling)
- Rudder size -> Improved rudder standards
- Maneuver strategy -> Better training, better communications
- Speed -> Better regulations and rules in adverse conditions
- Watch -> Make sure they have the tools they need, and they are located correctly
Of course, not sinking is the best outcome for safety. But if you do sink what changes were made to avoid the terrible loss of life:
- Lifeboats -> Adequate lifeboats for all people aboard
- Better life jackets -> Improved life-vest design
- Safety drills -> The holding of safety drills
- Communications improvements -> New policies and procedures and 24-hour radio coverage so that help will come as soon as possible
Next time you have a problem (big like the Titanic or small one like a tire blew out), uncover the causes and use them as a viewing platform to look at your whole operating situation. DuPont does this and finds an 11:1 Return on Investment from finding and fixing the causes of its problems.
My thanks to Mark Galley, Principal of ThinkReliability for some of the information and approach to the Titanic sinking and to Bill Holmes, President RCA RT Melbourne, Australia
About the Author
Joel Levitt is a leading trainer of maintenance professionals. He has trained more than 15,000 maintenance leaders from 3000 organizations in 20+ countries in over 500 sessions. Since 1980 he has been the President of Springfield Resources, a management consulting firm that services clients of all sizes on a wide range of maintenance issues.
He has 25 years of experience in many facets of maintenance including process control design, source equipment inspector, electrician, field service technician, maritime operations and property management. Prior to that, Levitt worked for a CMMS vendor and as an owner/manager in manufacturing.
He is a frequent speaker at maintenance and engineering conferences and has written 10 popular maintenance management texts. He has also published over 6 dozen articles on the topic. Levitt has served on the safety board of ANSI, Small Business United, National Family Business Council and on the executive committee of the Miquon School. He is a member of AFE and Vice President of the Philadelphia chapter.
Joel can be contacted at [email protected] or http://www.maintenancetraining.com/home
Recent Posts
AI and Site Reliability Engineers: Lessons from the Field.
Smarter, Faster, Deeper: How AI Is Transforming Root Cause Analysis in Software and Beyond
North America’s Looming Power Shortfall: A Root Cause Analysis for the Grid—and Beyond
Preventing EV Charger Downtime: How Smart Test Strategies Act as Root Cause Analysis in Action
Root Cause Analysis Software
Our RCA software mobilizes your team to complete standardized RCA’s while giving you the enterprise-wide data you need to increase asset performance and keep your team safe.
Root Cause Analysis Training