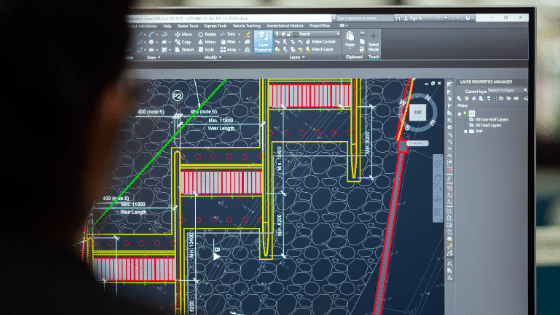
What is ‘Reliability Engineering’?
Reading Time: 3 minutes
What is ‘Reliability Engineering’? I have been very involved recently with ongoing LI discussions with respected and noted experts in the Safety community, revolving around the perceptions those in Safety have of Reliability, and vice-versa. In Safety today, there are ‘new’ approaches emerging being lead by noted Safety researchers like Sidney Dekker, Erik Hollnagel and Todd Conklin. Such ‘new’ approaches
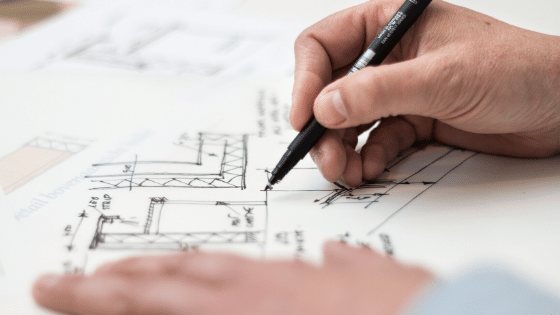
People Forget to Be Afraid…
Reading Time: 3 minutes
“Preventing process accidents requires vigilance. The passing of time without a process accident is not necessarily an indication that all is well and may contribute to a dangerous and growing sense of complacency. When people lose an appreciation of how their safety systems were intended to work, safety systems and controls can deteriorate, lessons can be forgotten, and hazards and deviations from safe
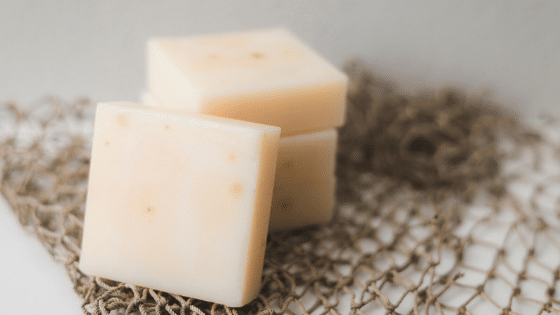
A Different View of the Swiss Cheese Model
Reading Time: 4 minutes
Much has been written about James Reason’s original Swiss Cheese Model described in his book Managing the Risks of Organizational Accidents. Figure 1 is a basic representation of this model. Many today consider this model to be obsolete because of the evolving complexity of systems due to emerging technologies. Therefore, the linearity of failure expressed in this original model, is not as
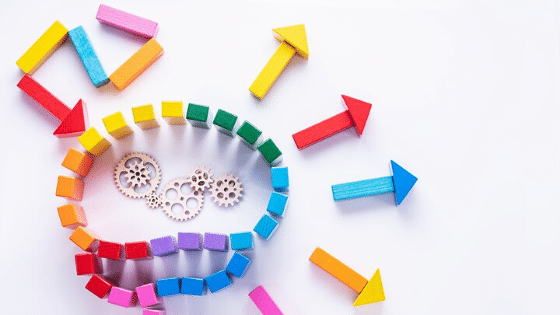
Is System’s Thinking Critical to Root Cause Analysis’s (RCA) Success?
Reading Time: 11 minutes
Is System’s Thinking Critical to Root Cause Analysis’s (RCA) Success? Put another way, can RCA be successful without the incorporation of system’s thinking? What prompted this question was that according to Drs. Leveson and Dekker in their 2014 paper Get To The Root of Accidents, systems thinking is not currently utilized in the application of RCA. In this paper they cite:
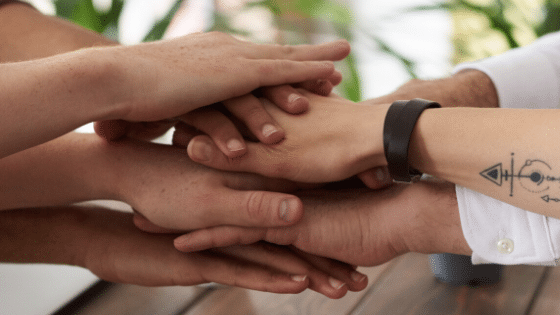
Why Can’t Learning Teams (LT) & RCA Teams be Friends?
Reading Time: 7 minutes
Why Can’t Learning Teams (LT) and RCA Teams be Friends? A Little History About How I Came Across Learning Teams. A little over three years ago I was asked to speak at a conference that was entitled, Human Performance, Root Cause and Trending or HPRCT (great conference BTW and I encourage you to attend). This was a different world for me as I typically
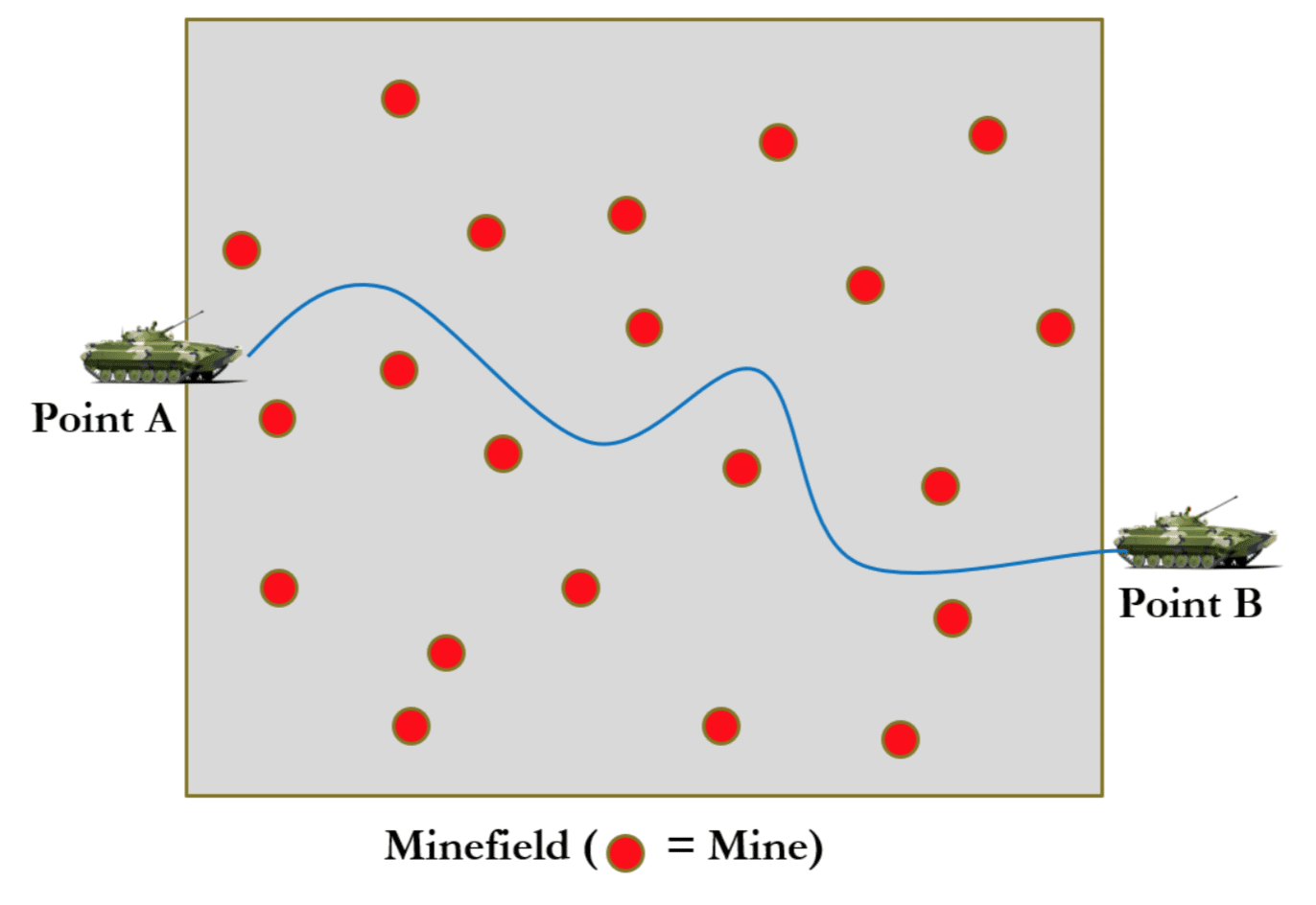
What Does It Mean to Be ‘Safe’?
Reading Time: 6 minutes
So what does it mean to be ‘safe’? Is a company ‘safe’ because they have not had an OSHA recordable injury in say over a one year period? Does that mean they will continue to be ‘safe’ in the next year? Does it mean they are at a higher risk of an incident in the near term, because they weren’t
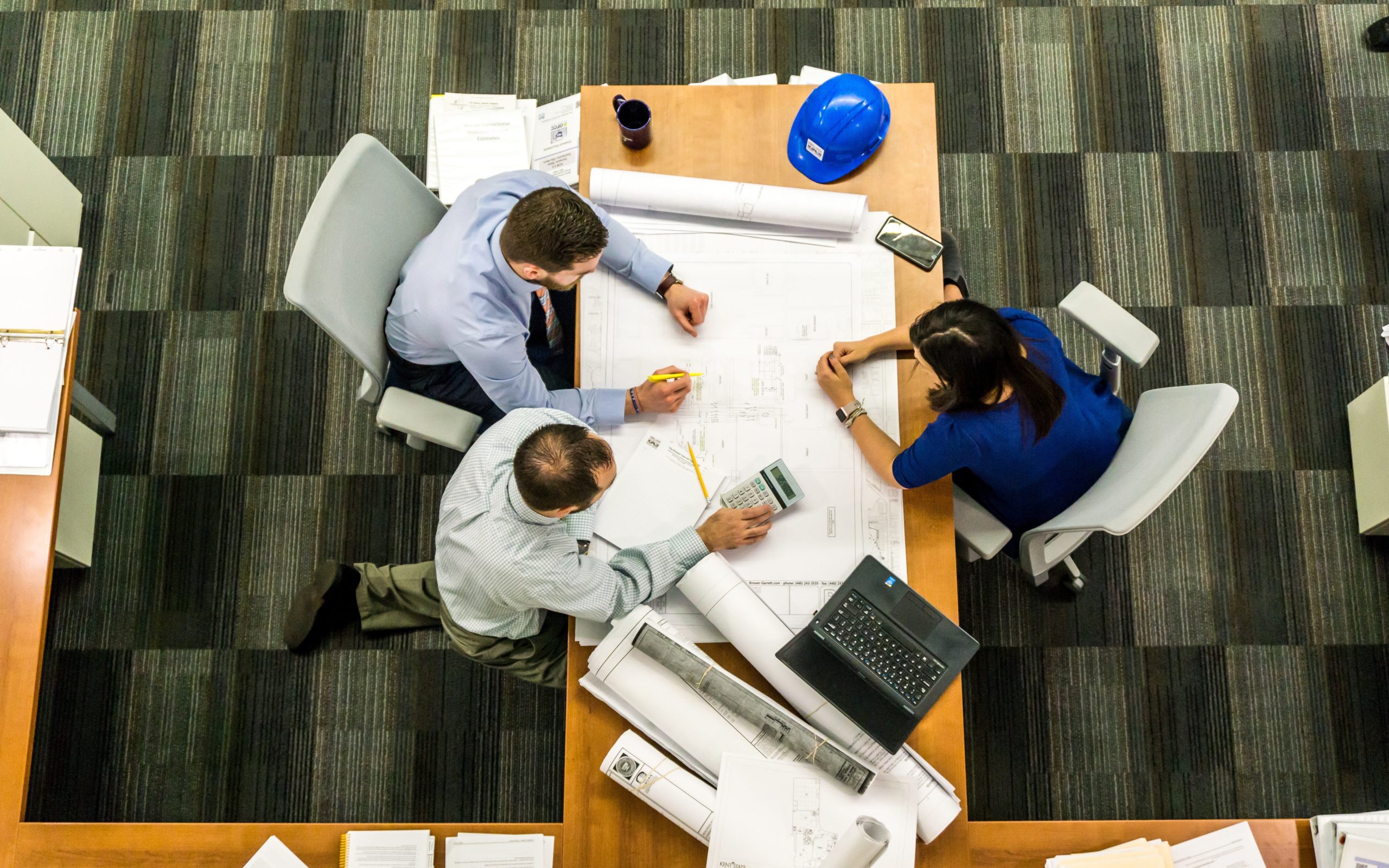
Do Learning Teams Make RCA Obsolete?
Reading Time: 2 minutes
Originally published August 31, 2017.
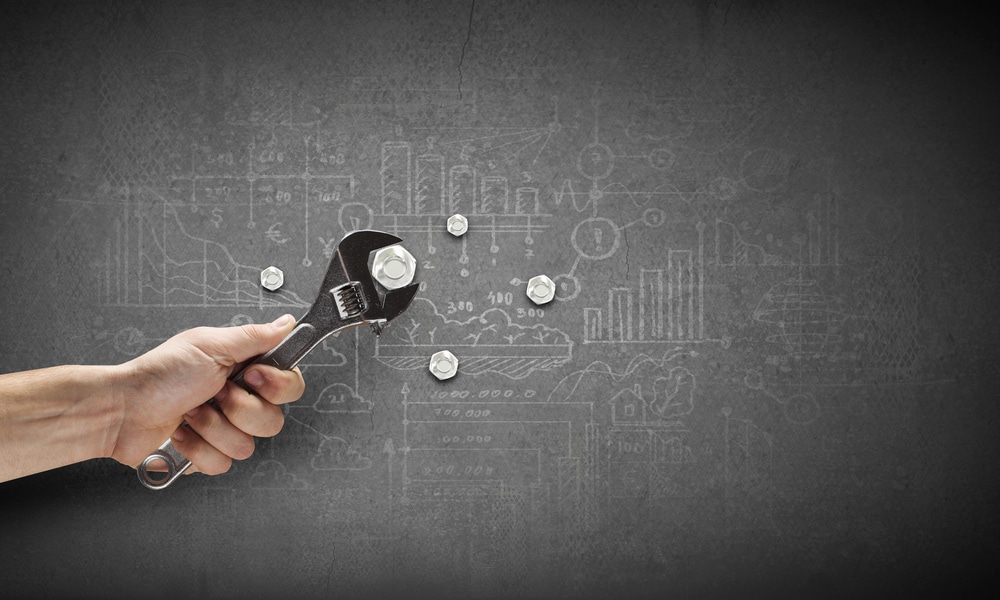
Understanding the Basics of Grease
Reading Time: 6 minutes
Since lubricating oil can oxidize, so can the base oil in grease. When the grease oxidizes, it usually darkens; there is a build-up of acidic oxidation products, just as in other lubrications. These products can have a destructive effect on the thickener, causing softening, oil bleeding, and leakage. Because grease does not conduct heat easily, serious oxidation can begin at
Defining & Achieving the Reliability Culture
Reading Time: 31 minutes
There is nothing more difficult to take in hand, more perilous to conduct, or more uncertain in its success than to take the lead in the introduction of a new order of things, because the innovator has for enemies, all of those who have done well under the old conditions, and luke-warm defenders in those who will do well under
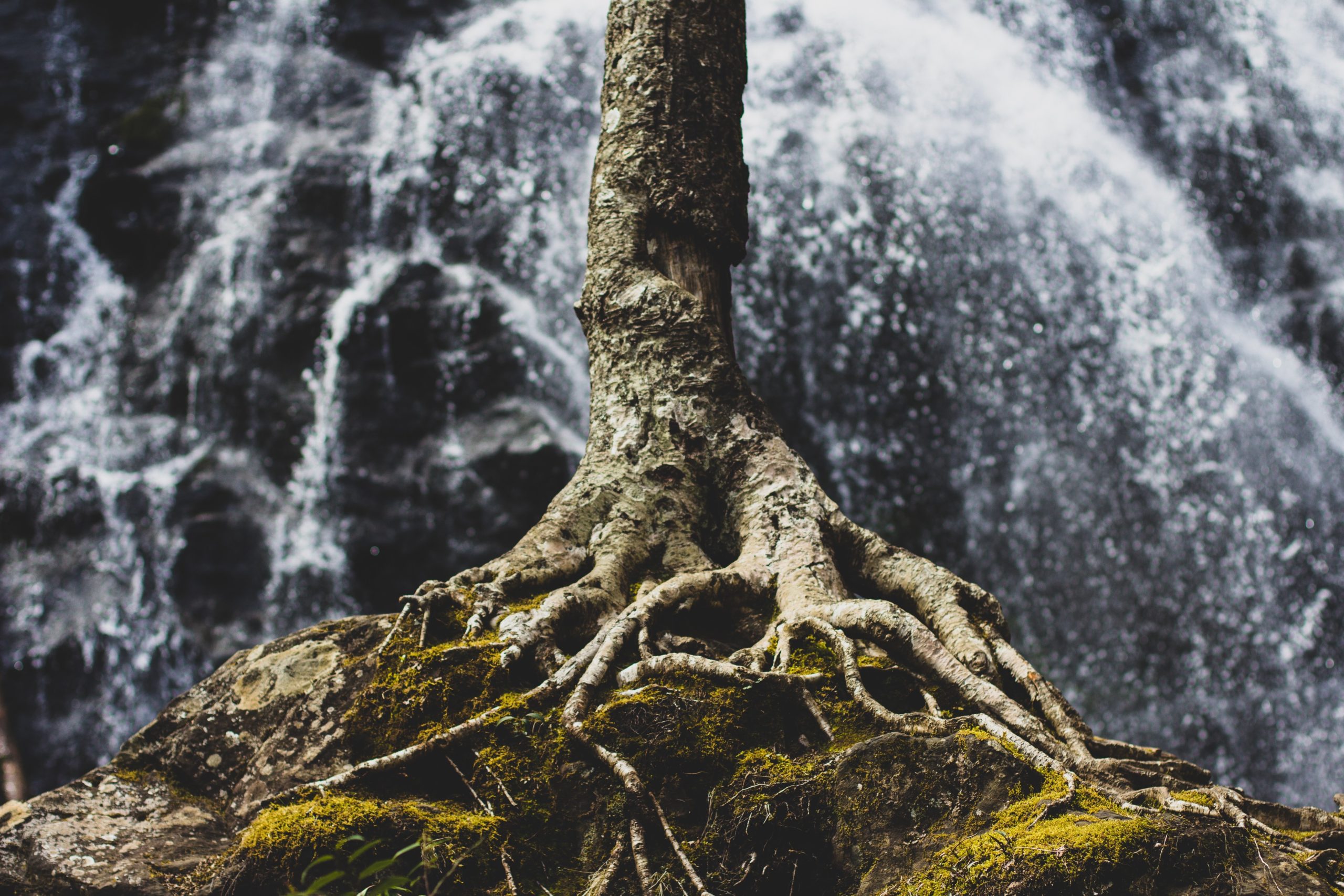
Root Cause Analysis vs. Shallow Cause Analysis: What’s the Difference?
Reading Time: < 1 minute
Does regulatory compliance with RCA guidelines ensure operational reliability? Operational Reliability involves the aggregation of Equipment, Process and Human Reliability methods and techniques. What is the difference between troubleshooting, problem solving and root cause analysis? Are the outcomes different when we use The 5-Whys, The Fishbone or a Logic Tree? Can deficiencies in our approach to RCA increase the risk
‘Fantasy’ Maintenance: The Illusion of Best Practices
Reading Time: 4 minutes
The following article was published in Plant Services earlier this year with the title, “Don’t get stuck in reactive mode – The world of fantasy maintenance is calling you”. The alias of the author is Captain Unreliability, so all credit should go to the Captain :-).
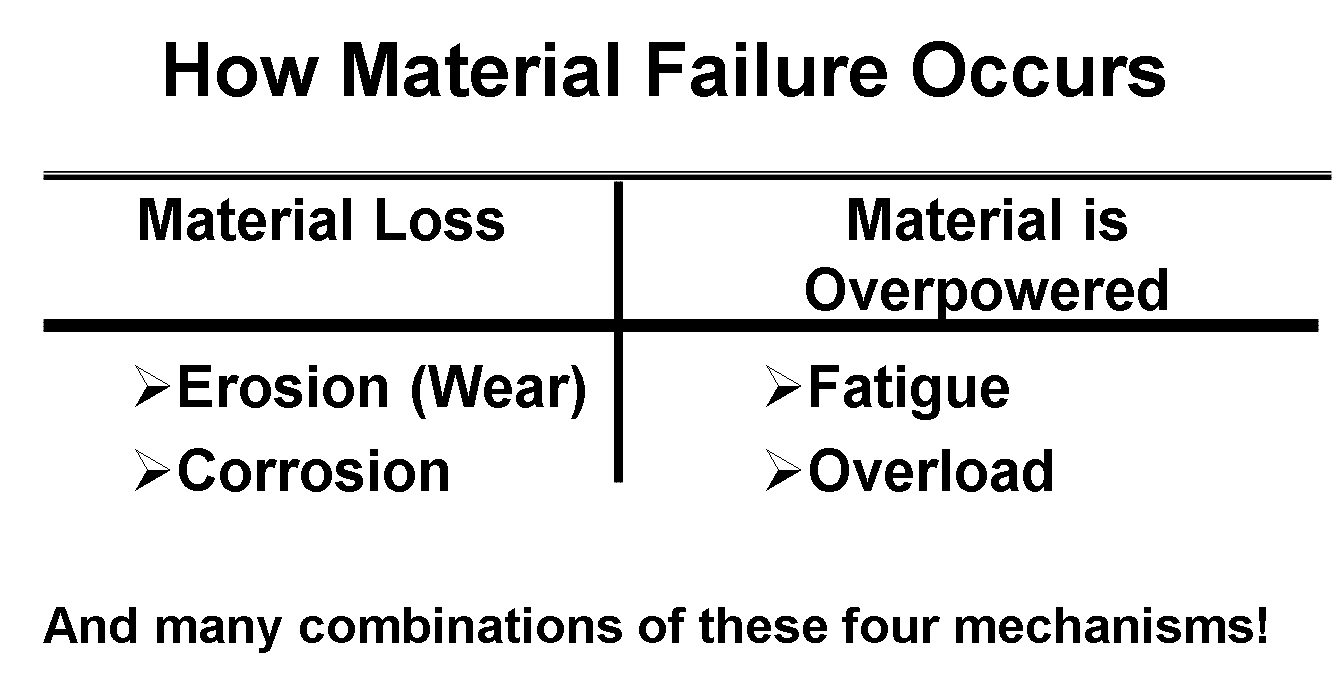
Fatigue & Overload: Part II, 4 Mechanisms of Component Failure
Reading Time: 4 minutes
Author’s Note: I want to reiterate that this Series about reading the basic fracture surfaces, is for novices who often come into contact with such failed components. This Series is about the basics (101), and is intended to give readers an appreciation for the value of such ‘broken’ parts to an effective investigation/RCA. While this information will be rudimentary to