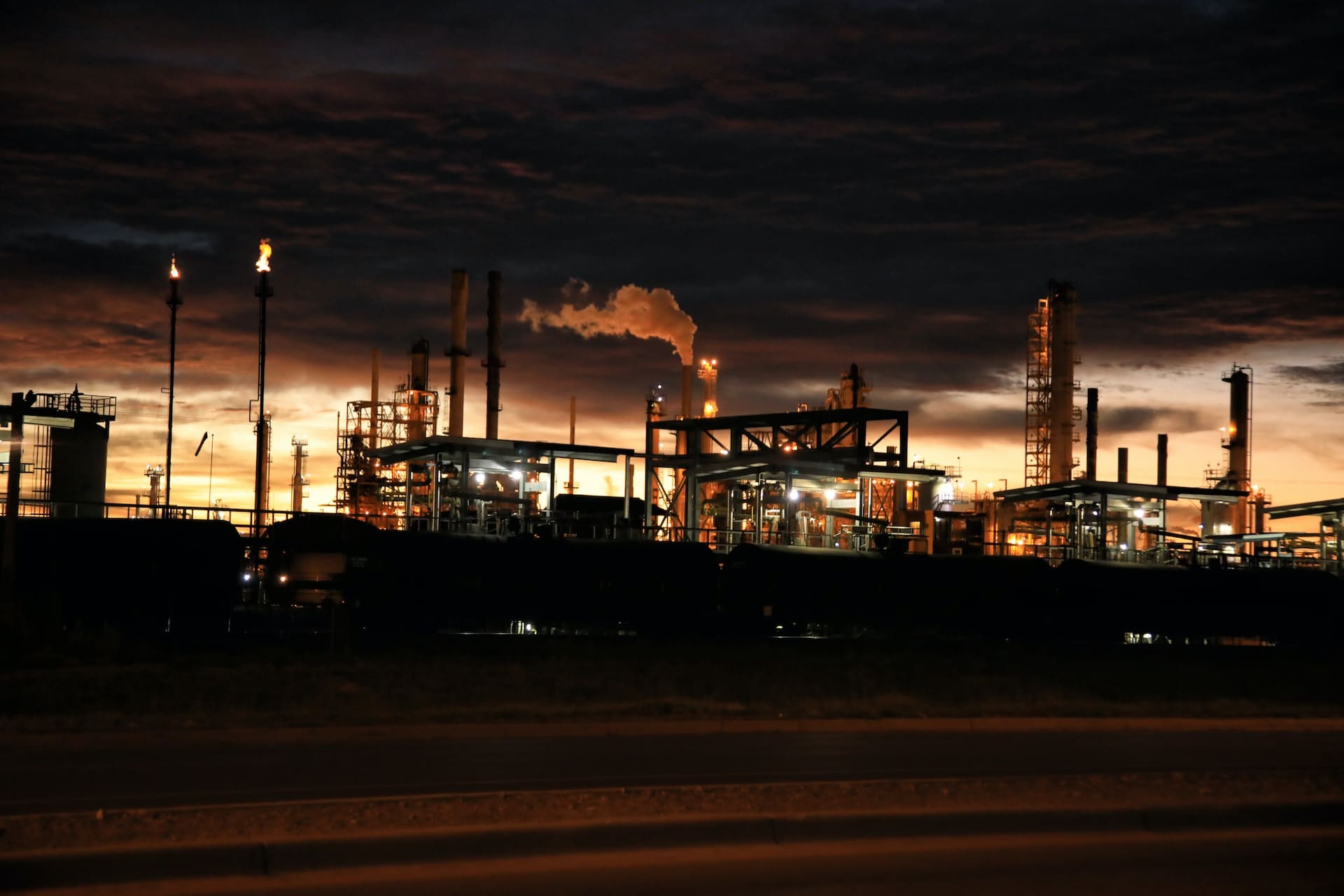
7 Powerful Root Cause Analysis Techniques and Tools
With over two decades in business – spanning strategy consulting, tech startups and executive leadership – I am committed to helping your organization thrive.
At Reliability, we’re on a mission to help enhance strategic decision-making and operational excellence through the power of Root Cause Analysis, and I hope this article will be helpful!
Our goal is to help you better understand these root cause analysis techniques by offering insights and practical tips based on years of experience. Whether you’re new to doing RCAs or a seasoned pro, we trust this will be useful in your journey towards working hard and working smart.
TL;DR
Root Cause Analysis (RCA) helps teams solve recurring problems by identifying their true source—not just the symptoms. The goal is simple: find the cause, fix it, and prevent it from happening again. But the process can be complex, and that’s where various root cause analysis techniques come into play.
In this article, we break down 7 powerful root cause analysis techniques, from 5 Whys to Fault Tree Analysis, each with practical insights on when and how to use them. Whether you’re in manufacturing, IT, or healthcare, these tools can sharpen your problem-solving process and boost long-term reliability.
1. The Ishikawa Fishbone Diagram (IFD)
Named after Japanese quality control statistician Kaoru Ishikawa, the Fishbone Diagram is a root cause analysis technique designed for group discussions. It helps teams track back to the potential root causes of a problem by sorting and relating them in a structured way. The diagram resembles a fishbone, with the problem at the head and the causes branching off the spine like bones. This visualization aids in categorizing potential causes and studying their complex interrelationships.
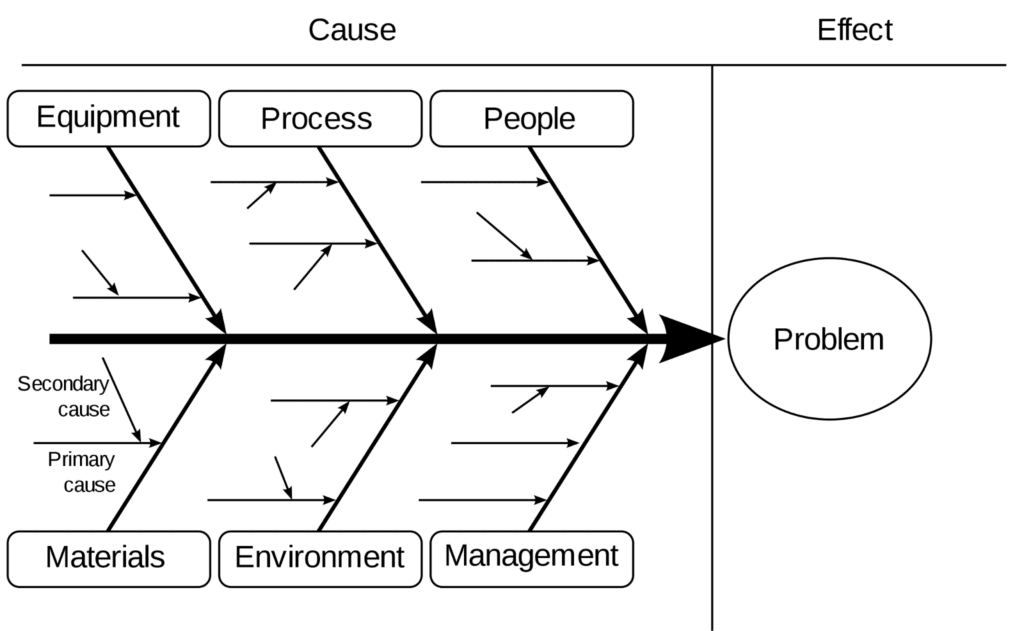
2. Pareto Chart
The Pareto Chart, rooted in the Pareto Principle, is a viable root cause analysis technique that help teams identify the most significant factors in a set of data. In most situations, 80% of problems can be traced back to about 20% of causes. By arranging bar heights from tallest to shortest, teams can prioritize the most significant factors and focus their improvement efforts where they can have the most impact.
3. 5 Whys Technique
The 5 Whys method is the epitome of root cause analysis technique simplicity when it comes to getting to the bottom of a problem. By repeatedly asking ‘why’ (typically five times), you can delve beneath the surface-level symptoms of a problem to unearth the root cause. This iterative interrogation is most effective when answers are grounded in factual evidence.

4. Failure Mode and Effects Analysis (FMEA)
When prevention is better than cure, Failure Mode and Effects Analysis (FMEA) steps in. This systematic, proactive root cause analysis technique helps teams identify where and how a process might fail. By predicting and examining potential process breakdowns and their impacts, teams can rectify issues before they turn into failures. FMEA is a three-step process that involves identifying potential failures, analyzing their effects, and prioritizing them based on severity, occurrence, and detection ratings.
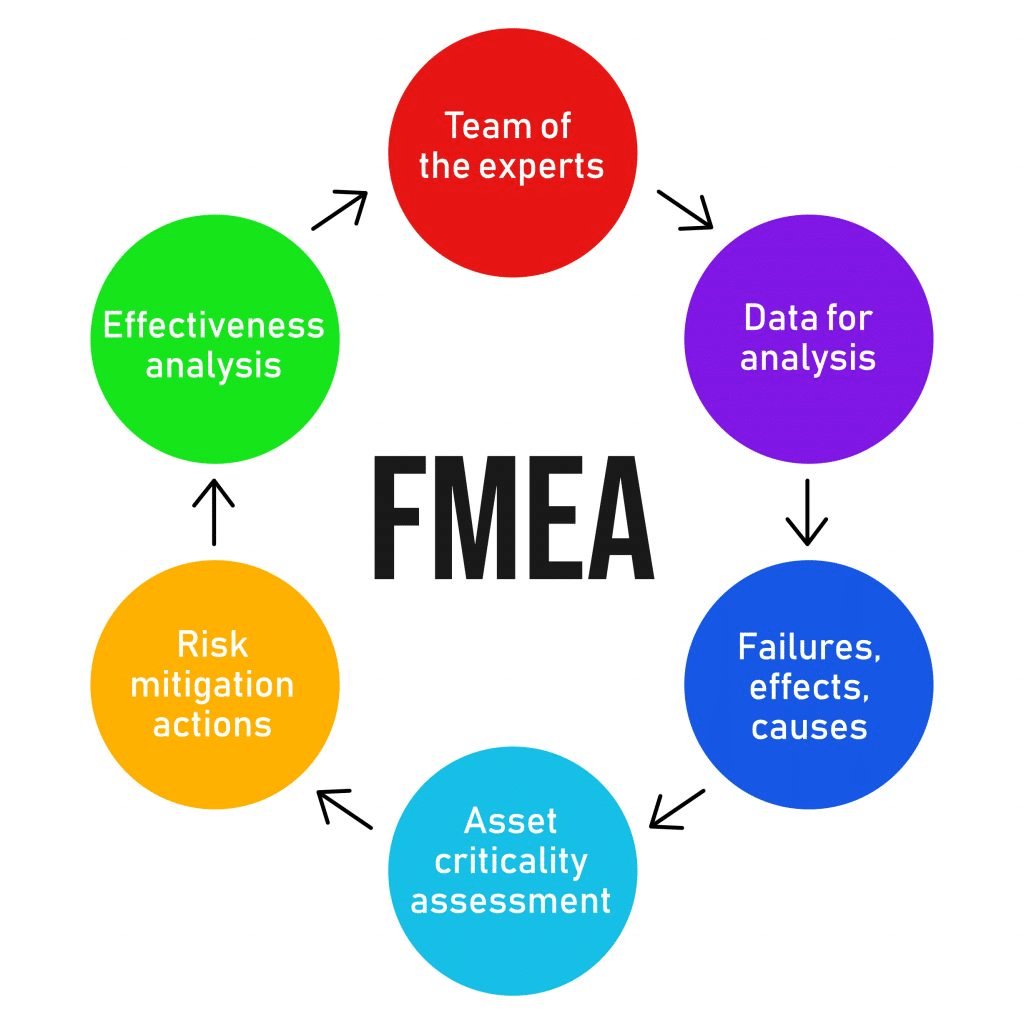
5. PROACT® RCA Method
The PROACT® RCA root cause analysis technique is a robust process designed to drive significant business results. Notably used to identify and analyze ‘chronic failures,’ which can otherwise be overlooked, this method is defined by its name:
PReserving Evidence and Acquiring Data
- Initial evidence collection step based on the 5-P’s – Parts, Position, People, Paper, and Paradigms.
Order Your Analysis Team and Assign Resources
- Assembling an unbiased team to analyze a specific failure.
Analyze the Event
- Reconstructing the event using a logic tree to identify Physical, Human, and Latent Root Causes.
Communicate Findings and Recommendations
- Developing and implementing solutions to prevent root cause recurrence.
Track and Measure Impact for Bottom Line Results
- Tracking the success of implemented recommendations and correlating the RCA’s effectiveness with ROI.
PROACT® RCA excels in mitigating risks, optimizing cost, and boosting performance, making it a valuable addition to any RCA toolkit.
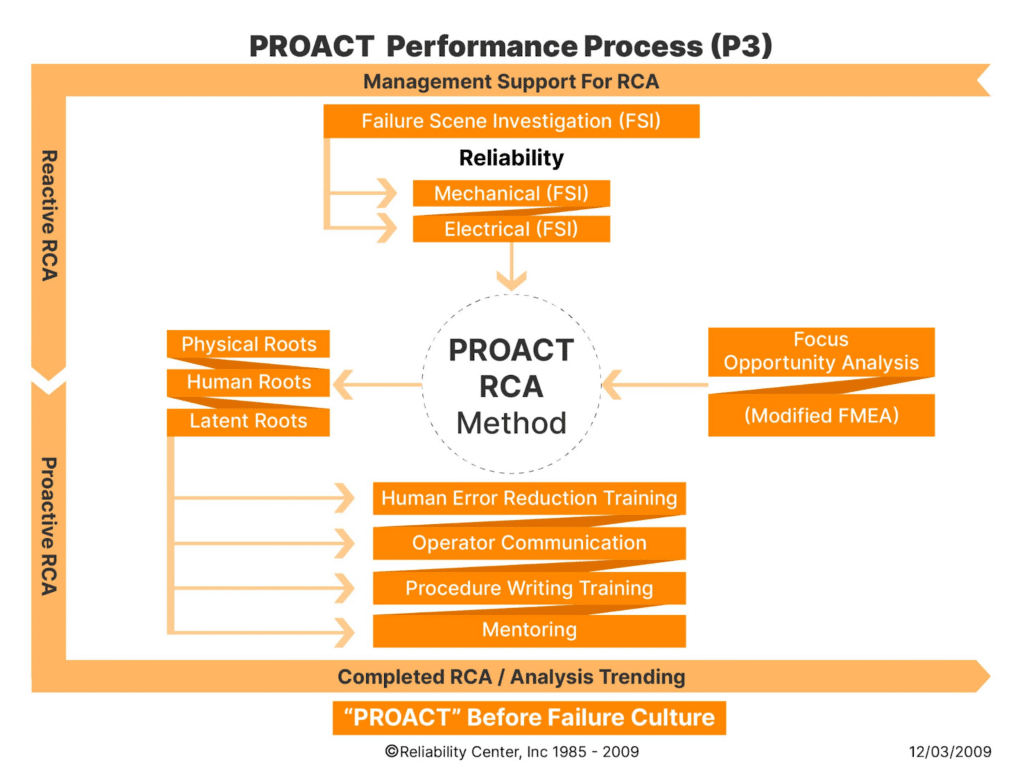
6. Affinity Diagram
The Affinity Diagram is a powerful root cause analysis technique/tool for dealing with large amounts of data. It organizes a broad range of information into groups based on their natural relationships, creating a clear, visual representation of complex situations. It’s particularly beneficial for condensing feedback from brainstorming sessions into manageable categories, fostering a better understanding of the broader picture.
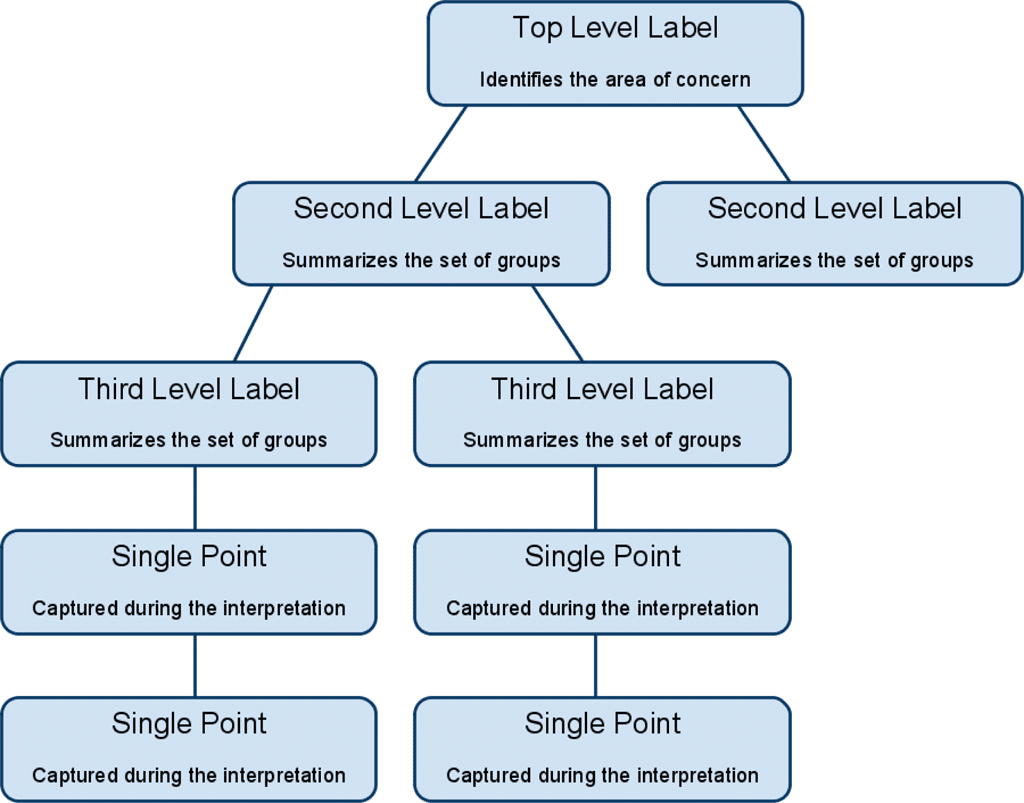
7. Fault Tree Analysis (FTA)
Fault Tree Analysis (FTA) is a top-down, deductive failure root cause analysis technique that explores the causes of faults or problems. It involves graphically mapping multiple causal chains to track back to possible root causes, using a tree-like diagram. FTA is particularly useful in high-risk industries, such as aerospace and nuclear power, where preventing failure is crucial.
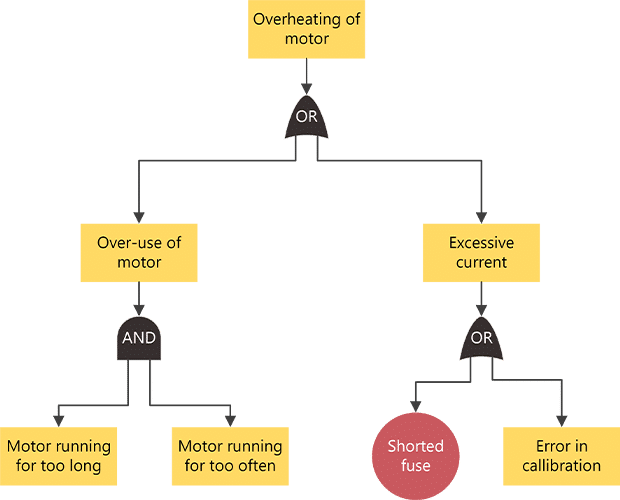
Each root cause analysis technique provides a unique approach for viewing and understanding problems, helping you pinpoint the root cause more effectively. The key is to choose the right root cause analysis tool by having an in-depth understanding of the problem at hand, which can significantly enhance your team’s problem-solving capabilities.
Power up your root cause analysis analysis with our EasyRCA and revolutionize your problem-solving process. Start Your Free Trial.
Technique | Key Advantage | Ideal Usage |
Ishikawa Fishbone Diagram | Visual representation of complex relationships | When there are many possible causes to a problem |
Pareto Chart | Prioritizes problem areas based on impact | When trying to identify the most significant causes |
5 Whys | Simple, iterative problem-solving technique | When the problem is straightforward and the solution is not immediately apparent |
FMEA | Proactive, preventative approach | When addressing complex processes that could lead to serious consequences if failed |
PROACT® RCA Method | Comprehensive, result-driven approach | When dealing with chronic, recurrent failures |
Affinity Diagram | Groups large data into manageable categories | When trying to find patterns and connections in large amounts of data |
Fault Tree Analysis (FTA) | Visual mapping of causal chains | When working in high-risk industries where prevention is crucial |
Closing thoughts
In conclusion, the root cause analysis techniques presented offer a diverse set of tools to help organizations address problems and inefficiencies effectively. From visual representations like the Ishikawa Fishbone Diagram and Pareto Chart to more proactive approaches such as the 5 Whys and Failure Mode and Effects Analysis (FMEA), each technique provides a unique perspective on identifying and mitigating root causes.
The PROACT® RCA Method stands out for its comprehensive process, particularly suited for chronic failures. Additionally, the Affinity Diagram and Fault Tree Analysis (FTA) contribute valuable insights by organizing data and exploring causal chains, respectively. Leveraging these techniques strategically enhances a team’s problem-solving capabilities, enabling them to make informed decisions and drive continuous improvement.
I hope you found these 7 powerful root cause analysis techniques/tools insightful and actionable! Stay tuned for more thought-provoking articles as we continue to share our knowledge. Success is rooted in a thorough understanding and consistent application, and we hope this article was a step in unlocking the full potential of Root Cause Analysis for your organization.
Reliability runs initiatives such as an online learning center focused on the proprietary PROACT® RCA methodology and EasyRCA.com software. For additional resources, visit our Reliability Resources. Alternatively, schedule an appointment with one of our experts to know more.
Recent Posts
AI and Site Reliability Engineers: Lessons from the Field.
Smarter, Faster, Deeper: How AI Is Transforming Root Cause Analysis in Software and Beyond
North America’s Looming Power Shortfall: A Root Cause Analysis for the Grid—and Beyond
Preventing EV Charger Downtime: How Smart Test Strategies Act as Root Cause Analysis in Action
Root Cause Analysis Software
Our RCA software mobilizes your team to complete standardized RCA’s while giving you the enterprise-wide data you need to increase asset performance and keep your team safe.
Root Cause Analysis Training