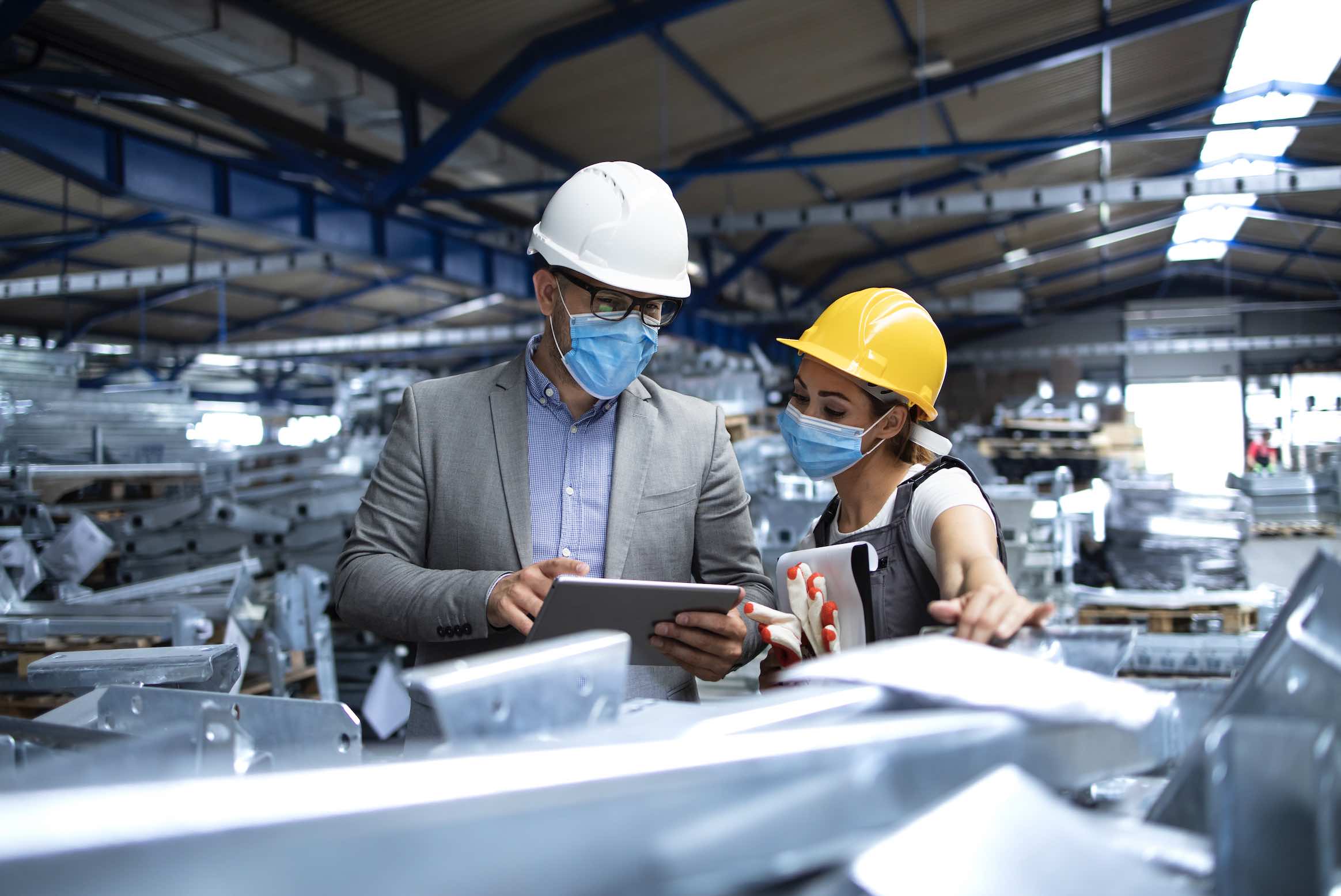
A Beginners Guide To Root Cause Analysis (RCA) 2024
When issues arise within a company, there are a number of ways to problem solve. Root Cause Analysis (RCA) is an effective method to identify and solve problems in business by determining the underlying inefficiencies or imperfections and taking the necessary steps to address them to prevent the problem from arising again.
Root Cause Analysis (RCA) can be an effective tool for any business and is widely used in industries such as oil and gas, engineering, healthcare, aviation, and IT operations. RCA works backward in an attempt to zero in on the potentially minor errors that are causing or could cause major concerns.
WHAT IS ROOT CAUSE ANALYSIS (RCA)?
Root cause analysis (RCA) is a systematic problem-solving technique used to identify the underlying causes of a particular issue or problem, rather than addressing only its symptoms. It involves a structured approach to investigating and understanding why something happened, with the goal of preventing its recurrence.
The term ‘RCA’ (Root Cause Analysis) is quite vague, misleading and easily misinterpreted by those who are not immersed in its use. It is a useless and counter-productive term because there is no universally accepted, standard RCA definition. Therefore, any process/tool someone is using to solve a problem is likely to be labelled as ‘RCA’.
It could be troubleshooting, brainstorming and/or some other more structured problem solving approaches such as 5-Whys, fishbone diagrams, causal factor trees and/or logic trees.
Various regulatory agencies have their own such definitions, as do corporations and companies. However, when definitions differ between agencies, corporations and industries, it is hard to measure the effectiveness of ‘RCA’ across the board, because everyone considers whatever they are doing, as ‘RCA’.
BASIC STEPS OF ROOT CAUSE ANALYSIS
These are the general steps involved in Root Cause Analysis. Keep in mind that specific methodologies and tools may vary depending on the context and industry.
- Define the Problem: The first step in Root Cause Analysis is to clearly define the problem or issue that needs to be addressed. It’s important to have a precise understanding of what went wrong and what the impact of the issue is.
- Gather Data: In this step, you collect relevant data and information about the problem. This may involve reviewing documents, conducting interviews, and examining processes or systems that are related to the issue. A thorough investigation is conducted with all relevant evidence in order to complete the following three steps:
- Identifying contributing factors
- Ranking factors by likelihood of causing the problem
- Classifying these factors into groups representing correlation, contribution, or “root cause” status
- Identify Root Causes: Once you have gathered data, you analyze it to identify the root causes of the problem. Root causes are the underlying factors that contributed to the issue. Techniques such as the “5 Whys” method or Fishbone Diagrams (Ishikawa Diagrams) are commonly used to uncover root causes.
- Develop and Implement Solutions: After identifying the root causes, the next step is to develop and implement solutions to address those root causes. These solutions should be designed to prevent the problem from recurring. It’s important to monitor the effectiveness of the solutions and make adjustments if necessary.
Additionally, incorporating lean six sigma green belt training and RCA can further enhance your ability to improve business processes and effectively implement Root Cause Analysis.
RCA METHODS
There are a variety of tools and methods to apply root cause analysis and the most effective tool may vary based on industry, company, the nature of the problem, etc. logic tree identifies the following common tools:
- 5 Whys is a popular tool that looks for the hidden cause by continuing to ask the question “why?” Though 5 is not always the magic number, it is often around the fifth “why” that the hidden cause is discovered.
- Fishbone is a cause and effect diagram that identifies multiple possible causes that could have led to the identified problem.
- A flowchart maps out all the steps of a process through different departments in an effect to identify where an error could have occurred.
- A Pareto chart is based on the premise that eighty percent of effects is caused by twenty percent of causes. It involves prioritizing possible causes based on likelihood of causing the identified problem.
4 KEY PRINCIPLES OF ROOT CAUSE ANALYSIS
The Washington State Department of Enterprise Services highlights four key principles involved in Root Cause Analysis:
1. There is usually more than one root cause for a problem
By making broad assumptions about what might be going wrong with business, an entire investigation can be derailed as you hone in one factor instead of investigating all potential contributing factors. RCA does not presume there is only one contributing factor but seeks to evaluate all factors that could be contributing to the systemic issue.
2. RCA is performed most effectively when accomplished through a systematic process with conclusions backed up by evidence
While it may be easy to identify a contributing factor and assume that is the root cause, RCA steers clear of a shallow investigation and looks at the entire system of “roots” as potential causes. RCA involves gathering quality evidence, not hearsay or unquantifiable data. RCA is not intended to be completed as a one man show, but rather a team effort that includes members from each potentially contributing department of the company.
3. The focus of the investigation should be “WHY the event occurred” not “WHO made the error.”
The goal of RCA is not to point fingers at an individual or department who made an error, but to identify systems that can be improved for overall the productivity of the company. RCA places the focus on why the event occurred by going step by step through each process leading up to the problem and evaluating all potential factors in play. The emphasis is on process improvement not on accusations.
4. Focusing on corrective measures of root causes is more effective than simply treating the symptoms of a problem or event
Unlike many problem solving methods that treat the symptom of a problem, Root Cause Analysis gets to the underlying “root” of the problem but investigation does not end at identification of root cause. Once one or more root causes are identified, corrective action is taken in order to prevent the problem from occurring again. RCA can also be used as a method in proactive management- identifying underlying errors before a problem has manifested.
WHAT RCA TOOLS DO WE RECOMMEND?
While one can theoretically perform RCAs with sticky notes or on a blank excel sheet, simple tools designed for maximizing impact can be highly effective in taking your RCA game to the next level. EasyRCA is our software offering that is the culmination of 50+years experience in hands-on Reliability training and consulting. It is designed to get your organization to the root of the problem as quick as possible and without any training needed. EasyRCA is cloud-based, designed for team collaboration, and adaptable to multiple RCA methodologies to fit your company’s needs. Leadership can always view progress in real-time and teams can send off reports anytime with 1-Click professional formatting. Visit EasyRCA.com to learn more and book a Free Demo!
Recent Posts
UK Retail Cyberattacks: What M&S, Harrods & Co-op Reveal About Cybersecurity and Root Cause Analysis
Richmond Water Crisis Exposes Infrastructure Vulnerabilities: Why RCA Is Key to Long-Term Solutions
Introducing RCA Turbo: Instant Root Cause Analysis with a Snap or a Sentence
Unpacking the Iberian Peninsula Blackout: How Root Cause Analysis Can Illuminate Grid Vulnerabilities
Root Cause Analysis Software
Our RCA software mobilizes your team to complete standardized RCA’s while giving you the enterprise-wide data you need to increase asset performance and keep your team safe.
Root Cause Analysis Training