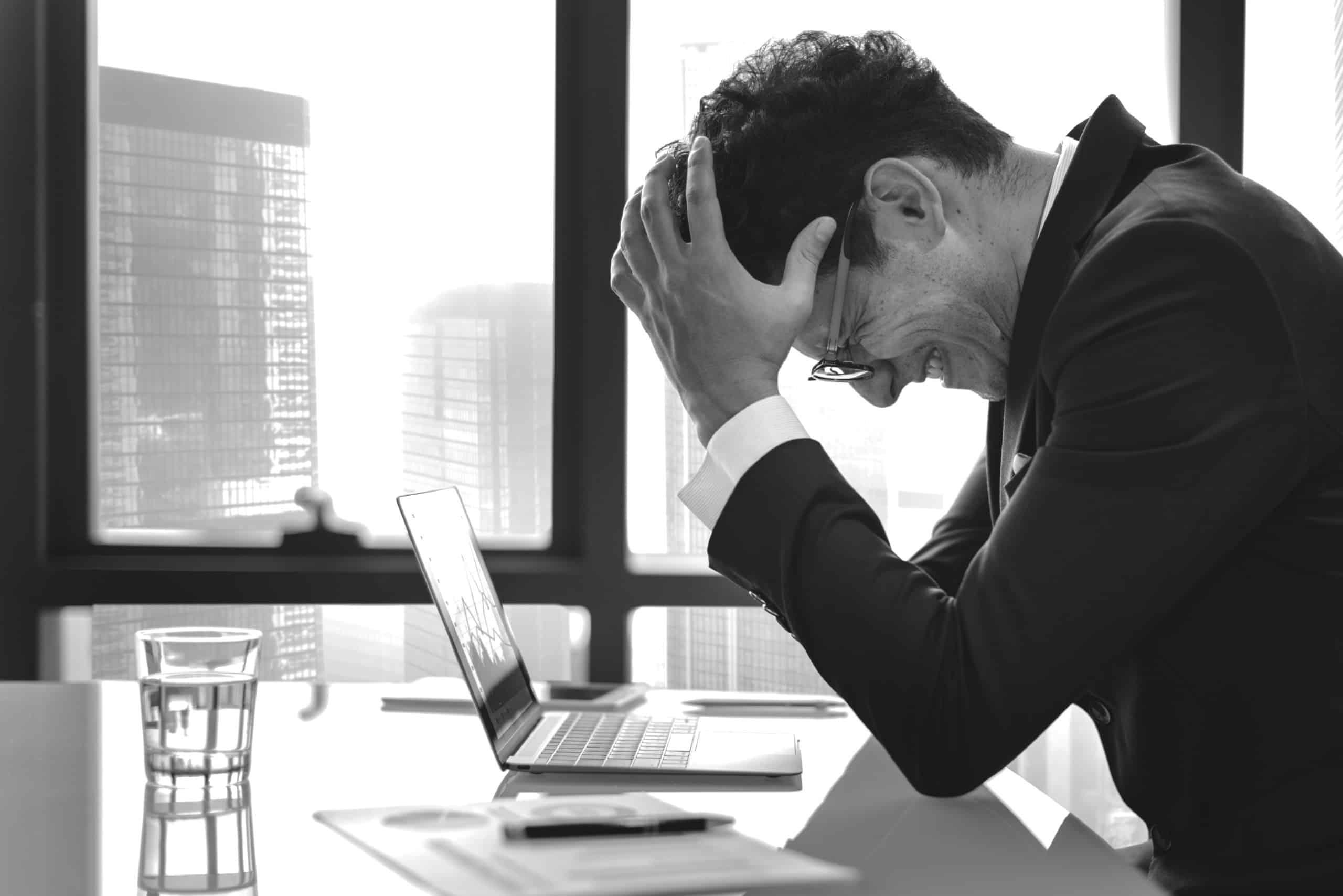
Are We Crazy About Mistakes?
First, a question: What is the difference between a child hitting a pitch and the ball breaking a neighbor’s window and the child throwing the ball at the window and breaking it? One was a mistake and the other was a conscience act. In maintenance the first act, a mistake is a learning experience and requires little or no action from management. The person will be more careful on their own. The second act requires stiff and swift action from parents (the management).
Second, a story: A massive shutdown in one of the tar sand projects ran without a lost time safety incident. On the last day an engineer was walking whilst looking at a drawing, tripped, fell forward and got a compression fracture in the wrist. The engineer did an unsafe act. Again a talking to is enough since the act itself will provide the training. You can rest assured that there is one engineer who will be more careful in the future.
When a mistake happens, the knee jerk reaction is to find out whom to blame and sack them. Sacking them makes us feel we have done our duty, rooted out the problem and we have returned the shop floor to a safe condition. Have we? Does this action really protect the rest of the people, the product or the organization?
How does your firm view mistakes? Have good workers sacked because of a lapse of judgment? I recently read a book titled Managing Maintenance Error by James Reason and Alan Hobbs (2006) that has me thinking about mistakes and errors.
It led me back in time when I was a field service electronics technician. At the end of one day I was in a hurry because it was a Friday and the traffic would start to get really bad unless I left soon. I was re-assembling a panel and pushed it into place. I didn’t notice one of the connections came loose. That wire conducted 110V through all the CMOS (this was a long time ago) circuits burning everything out. I was shattered but not fired. I can tell you I was 10 times more careful after that. After all, don’t they tell you that experience comes from making mistakes? If we were in a class I would ask who here in this class ever did something stupid like I did? I would say if you ever carried tools your hand is either up or you are lying!
There was a story about Henry Ford Sr. One of his engineers made a bad design error and cost the company millions of dollars. The engineer loved his job and was miserable. He returned to his desk to clean it out when Ford walked by asking him what he was doing. When he answered “Saving you the effort of sacking me” Ford told him, in no uncertain terms, that he wasn’t going anywhere. Ford said “I just paid millions educating you, you are not going anywhere!”
The Reason and Hobbs book says that mistakes are inevitable. They say that most of the exhortations toward zero defects (impossible), zero mistakes (impossible) actually make the situation worse. Unlike common wisdom on this, some of the worst accidents have been mistakes by quality, experienced, dedicated, long term workers having a lapse of judgment.
If that is the case then we have a problem; how do we deal with this? The first step is to realize that errors occur. We have to sort out honest mistakes (that are teaching moments) from intentional mistakes (which may become disciplinary issues). We have to investigate the conditions that made the mistake more likely. Some of the conditions that promote mistakes include intense pressure to complete jobs, long hours, unrelated fatigue, sickness, prescription and over the counter drugs, bad lighting, improvised tools and materials, uncomfortable working conditions (cold or hot), lack of specific training, etc.
The follow up question is how good our organization is at learning from past mistakes and near misses. Are they written into simple narratives and put into case studies and are required reading? Are old mistakes studied and are the conditions that caused them eliminated or mitigated?
About the Author
Joel Levitt is a leading trainer of maintenance professionals. He has trained more than 15,000 maintenance leaders from 3000 organizations in 20+ countries in over 500 sessions. Since 1980 he has been the President of Springfield Resources, a management consulting firm that services clients of all sizes on a wide range of maintenance issues.
He has 25 years of experience in many facets of maintenance including process control design, source equipment inspector, electrician, field service technician, maritime operations and property management. Prior to that, Levitt worked for a CMMS vendor and as an owner/manager in manufacturing.
He is a frequent speaker at maintenance and engineering conferences and has written 10 popular maintenance management texts. He has also published over 6 dozen articles on the topic. Levitt has served on the safety board of ANSI, Small Business United, National Family Business Council and on the executive committee of the Miquon School. He is a member of AFE and Vice President of the Philadelphia chapter.
Joel can be contacted at [email protected] or http://www.maintenancetraining.com/home
Recent Posts
UK Retail Cyberattacks: What M&S, Harrods & Co-op Reveal About Cybersecurity and Root Cause Analysis
Richmond Water Crisis Exposes Infrastructure Vulnerabilities: Why RCA Is Key to Long-Term Solutions
Introducing RCA Turbo: Instant Root Cause Analysis with a Snap or a Sentence
Unpacking the Iberian Peninsula Blackout: How Root Cause Analysis Can Illuminate Grid Vulnerabilities
Root Cause Analysis Software
Our RCA software mobilizes your team to complete standardized RCA’s while giving you the enterprise-wide data you need to increase asset performance and keep your team safe.
Root Cause Analysis Training