INTRODUCTION
In the world of business, the key to sustainable growth and success lies in identifying the root causes of failures and problems. However, not all Root Cause Analysis (RCA) methods are created equal. Today, we will explore the power of PROACT, a proven and robust approach that drives incredible results for numerous companies.
Unlike superficial analyses, PROACT® RCA delves deep into the intricacies of different analytical methodologies used in the field. Traditional techniques like troubleshooting and brainstorming may be quick to implement but often fall short in providing comprehensive and reliable root cause identification. On the other hand, structured approaches like the 5-whys and fishbone diagrams offer more discipline but can be misapplied due to time constraints.
Furthermore, we will delve into the PROACT® EasyRCA software, a powerful tool that empowers analysts to conduct thorough and effective RCAs. With features like logic trees, customizable templates, cost tracking, and ROI calculators, the EasyRCA software streamlines the RCA process, making it more efficient and impactful.
To illustrate the real-world impact of the PROACT® approach, we will share compelling case studies from various industries, highlighting significant financial returns achieved through the implementation of PROACT® RCA. These examples will underscore the transformative potential of a well-executed RCA process and inspire companies seeking to improve their performance and reliability.
ARE ALL RCA THE SAME?
An RCA myth shared by many managers is that RCA methods are all the same, when in fact they are NOT.An RCA myth shared by many managers is that RCA methods are all the same, when in fact they are NOT. The range of what constitutes an effective RCA method is vast. Some RCA techniques have minimal emphasis on establishing all the ways a problem can occur. Others provide a more comprehensive set of reasons a problem occurred.
Verification of each possibility can also range from someone saying it happened (weak verification) to re-construction and testing of each possibility (strong verification). RCA methods can be shallow, or they can be robust, it depends on what the management wants to accomplish. Here are some analytical methodologies that are often grouped into the category of RCA:
Troubleshooting
When something ‘fails’ in our workplaces, do faces come to mind of the people that we immediately turn to, to make everything alright? These are our ‘heroes’ who get us back to normalcy quickly, and they get a fair amount of recognition for doing so. However, these individuals are being provided positive recognition for being great responders.
They are rarely doing any analytics to understand root causes, but they are great at implementing temporary solutions. A progressive management team, under these conditions, would be asking, “Why is this person getting so much practice at responding?” That’s where the meat is. This approach is normally attractive because it is quick, inexpensive (in the short-term) and demonstrates immediate action.
Brainstorming
We can all relate to this analytical technique. When something bad happens, we tend to put very smart people in a room who listen to a summary of what we know happened (the bad outcome). Oftentimes this description embeds hearsay as fact, and the group is accepting of this hearsay, as they move on to solutions.
So many bright people throw out disconnected ideas as to what they think happened, and then they move on to corrective actions. Usually, this approach focuses on speed to demonstrate activity, and as a result, is weak on evidence and deep analysis down to true root causes. Chances are this team will be meeting again because the failure will recur. This approach takes a little longer because we are not dealing with an individual, we are dealing with several individuals so this requires more give-and-take in discussions.
Problem Solving
This approach is very common and it is essentially brainstorming plus a structured analytical tool like 5-whys or a fishbone diagram. The ‘tool’ provides a degree of discipline as it has a series of steps and a structure to follow. This is certainly more progressive than troubleshooting and brainstorming. This approach, when applied properly, could be effective. However, in my 35+ years of this business, I find this approach is rarely applied properly.
People are usually time-constrained to hurry up, and therefore the time to collect evidence is expended. So we run with hearsay and assumption, treating them as facts. We develop and implement recommendations accordingly. Dick Swanson (Owner, Performance Management Initiatives, Inc.) says, “The irony of this association is rooted in the fact that the 5-Why approach was developed by Toyota as a tool for assembly floor supervisors to keep production moving, and not as a tool to identify deep, underlying causes of complex events”.
I will add another potential form of RCA, used by many, which is ‘trial and error’. I do not list it with the others because I really don’t consider it an analytical process. This approach just supports the paradigm of ‘if it ain’t broke, don’t fix it!’ This is more akin to applying a crisis maintenance strategy. There really is no analytics going on, we just fix things when they break. Our approach is different, and we call it PROACT®.
WHAT IS PROACT?
PROACT is a robust Root Cause Analysis (RCA) process that can drive incredible business results for your company.PROACT is a Root Cause Analysis (RCA) process that can drive incredible business results for your company. Since its inception in the mid-80’s, the PROACT approach has helped hundreds of companies do tens of thousands of successful RCAs, resulting in large financial returns for the business.
The PROACT approach helps to identify and conduct RCAs on those events that are ‘hidden in plain sight.’ These failures happen every day, on every shift; yet their individual occurrences do not meet the threshold to trigger a formal RCA process. These failures are hidden in plain sight and often viewed as ‘a cost of doing business’. These ‘chronic failures’ are the underserved of the organization and they are truly what is eating the corporation’s lunch (bottom-line). On an annual basis, they are an organization’s most costly failures!
In the world of reliability and maintenance, the PROACT® (P3) method has emerged as a game-changer, providing a systematic approach to root cause analysis (RCA) that goes beyond identifying immediate issues. It delves deeper into the underlying causes that give rise to problems, thereby offering a comprehensive solution. This article delves into the intricacies of the PROACT® method, its multifaceted benefits, and its role in fostering operational excellence.
What Does PROACT® stand for?
The PROACT® acronym stands for the following basic, investigative process steps:
1. PReserving Evidence and Acquiring Data
Just like any of your favorite detective/investigative shows on TV, STEP #1 is to preserve the scene and to collect evidence in a very disciplined manner. In the PROACT® methodology we collect evidence based on the 5-P’s, which are data categories. They are Parts, Position, People, Paper and Paradigms. These categories make it easier to remember the types of data/evidence we have to collect.
2. Order Your Analysis Team and Assign Resources
This step is about organizing an ideal team to analyze a specific failure. This deals with roles and responsibilities of team members and more importantly, minimizes the potential of any bias between the team and the nature of the Event.
3. Analyze the Event
At this point in the investigative process we should have ample data/evidence to start with and a team who has nothing to lose or gain by the outcome of the analysis (unbiased). Now comes the critical step of Event reconstruction. PROACT® utilizes a logic tree to graphically express the event reconstruction. Proper application of a logic tree will utilize both deductive and inductive reasoning, evidence-based validation of hypotheses and identification of Physical, Human and Latent/Systemic Root Causes. Proper use of a logic tree will combine the physical sciences (physics of Event) and the social sciences (the systems and human contributions to the Event).
4. Communicate Findings and Recommendations
Theoretically at this point we have done a lot of work to identify our actionable root causes. This is about 50% of the effort to complete an effective RCA. It is at this point that we must develop and implement effective solutions to counter our identified root causes. Determining accurate and comprehensive root causes is useless, if we do not act to prevent their recurrence.
5. Track and Measure Impact for Bottom Line Results
Finally, just because we developed recommendations does not mean 1) that we implemented them and 2) that they worked. An effective RCA system will close the loop by demonstrating a benefit on the bottom-line. Each recommendation should have a performance metric tied to it, demonstrating proof that something got better. As often as possible, RCA’s effectiveness should be tied to ROI and corporate dashboards.
The PROACT® Approach is designed to help mitigate risk, optimize cost, increase performance, and contribute to exceeding Reliability goals. Whether we’re in a manufacturing setting, hospital, or school; the PROACT® process remains the same. It allows us to drill down to the root causes and implement the correct and needed changes.
Benefits of a Functional RCA Effort From A Reliability Perspective
A robust RCA effort, such as the PROACT® method, brings a plethora of benefits from a reliability perspective. The table below covers the main benefits of functional RCA:
Benefit |
Description |
Increased Equipment Availability |
PROACT® minimizes equipment downtime by identifying and rectifying root causes. |
Increased Uptime |
By averting recurring issues, the costs associated with repairs, replacements, and downtime are significantly reduced. |
Reduced Operating Costs |
Efficiently running equipment consumes less energy, leading to lower energy costs. |
Reduced Energy Costs |
PROACT® ensures equipment runs efficiently, leading to lower energy consumption and costs. |
Improved Safety & Environmental Performance |
PROACT® identifies and addresses root causes, mitigating potential safety hazards and environmental risks. |
Reduced Maintenance Costs |
Preventive measures taken as a result of RCA can reduce the frequency and extent of maintenance, leading to lower costs. |
Improved Quality and Yields |
PROACT® ensures equipment operates as intended, improving output quality and yields. |
Reduced Need for Capital Investment to Maintain Assets |
With fewer breakdowns and failures, capital investment in new equipment or extensive repairs are reduced. |
Table 1: Benefits of a Functional RCA Effort From A Reliability Perspective
THE EVOLUTION OF RELIABILITY
An RCA myth shared by many managers is that RCA methods are all the same, when in fact they are NOT.The Evolution of Reliability
Reliability has evolved from a reactive approach to a proactive one. The journey began with crisis management, where issues were addressed as they occurred. This was followed by time-based maintenance, and then condition-based maintenance, which involved monitoring equipment and addressing issues as they arose. The current stage in the evolution of reliability is the elimination of recurrence, which is a proactive approach that seeks to identify and address root causes to prevent issues from recurring. This is where the PROACT® method shines.
The following graph breaks down the evolution of Reliability:
Reliability Strategy |
What is it? |
Example |
Breakdown Maintenance (BD) |
Reactive maintenance approach where maintenance activities are performed only after a failure occurs. The focus is on restoring the system to working condition rather than preventing failures. |
If a manufacturing machine breaks down, the maintenance team will fix it or replace the faulty component to resume production. |
Planned Preventive Maintenance (PM) |
Scheduled maintenance tasks performed on equipment to prevent failures before they occur. Tasks are based on manufacturer recommendations, historical data, or industry best practices. |
Conducting routine inspections, lubrication, and component replacements on a production line to minimize the chances of unexpected breakdowns. |
Condition-Based Maintenance (CBM) |
Monitoring and analyzing real-time or historical condition data of equipment to make maintenance decisions. Detecting potential issues by tracking parameters like vibration, temperature, or fluid levels and scheduling proactive maintenance. |
Using sensors installed on a turbine to measure vibration levels. If they exceed a predetermined threshold, scheduling maintenance to avoid catastrophic failure. |
Root Cause |
Investigating the events leading up to a failure and analyzing data to determine the fundamental reasons behind the problem. Aims to identify underlying causes and implement corrective actions to prevent similar issues in the future. |
Conducting RCA on a motor failure and discovering that inadequate lubrication was the root cause, leading to a change in maintenance practices to ensure proper lubrication. |
System Precision |
Advanced stage of reliability evolution where maintenance strategies are highly optimized and tailored to specific systems. A comprehensive and holistic approach that considers system interdependencies, operational context, and risk analysis. |
Leveraging advanced techniques like reliability-centered maintenance (RCM) and data analytics to optimize maintenance plans and maximize system performance. |
Table 2: Reliability Strategies in the Evolution of Reliability
THE PROACT® (P3) MODEL
The PROACT® (P3) Model is a proactive approach to reliability and maintenance management that complements the Evolution of Reliability stages.The PROACT® (P3) Model focuses on preventing failures and optimizing maintenance strategies to improve overall system reliability. The PROACT® method is a systematic approach to RCA that involves identifying the physical, human, and latent root causes of a problem. It sets the stage for leveraging RCA by focusing on three key areas: the root system, the analysis, and the knowledge base.
Leverage the Root System
The root system in the PROACT® method comprises physical, human, and latent root causes.
- Physical Root Causes: These are the direct consequences of decision-making. They are tangible and can include components and indications such as mechanical vibrations.
- Human Root Causes: These are decision errors. They are the actions (or inactions) that trigger the physical roots to surface.
- Latent Root Causes: These are cultural barriers or perceived flaws, organizational or system flaws. They are the support systems that affect behavior, including policies and procedures, training systems, incentive systems, supervision, accountability systems, and purchasing habits.
Component |
Description |
Example |
Physical Root Causes |
Direct consequences of decision-making, tangible components, and indications. |
Mechanical vibrations due to improper torque application. |
Human Root Causes |
Decision errors, actions (or inactions) that trigger the physical roots to surface. |
Deciding not to use a torque wrench because in the past, the supervisor gave positive recognition for getting the job done fast. |
Latent Root Causes |
Cultural barriers or perceived flaws, organizational or system flaws, support systems that affect behavior. |
Inadequate training on equipment maintenance caused incorrect procedures, leading to premature equipment failure and increased downtime. |
Table 3: Components of the PROACT® Root System and Examples
Leverage The Analysis
The analysis in the PROACT® method involves identifying the root causes and determining how they contributed to the problem. For example, a worker may have decided not to use a torque wrench because in the past, the supervisor gave positive recognition for getting the job done fast. This is a human root cause that led to a physical root cause (improper torque applied), which resulted in a problem (equipment failure).
Another example could be an operator deciding to overfill a tank instead of filling it three quarters full as required by procedure. This decision, made to save time by skipping a step, is a human root cause that could lead to a physical root cause (overfilled tank), potentially resulting in a problem (spillage, equipment damage, or safety hazard).
Leverage the Knowledge Base
The knowledge base in the PROACT® method refers to the collective understanding and experience of the organization. By leveraging this knowledge base, organizations can better identify potential root causes and develop effective solutions. This involves sharing and learning from past experiences, training, and best practices.
Supporting Operational Excellence
The PROACT® method supports operational excellence by promoting a culture of continuous improvement. By identifying and addressing root causes, organizations can prevent recurring issues, improve efficiency, and enhance performance. This proactive approach to problem-solving encourages a mindset of prevention rather than reaction, fostering a culture that values quality, safety, and efficiency.
PROACT® Method Components |
Impact on Operational Excellence |
Physical Root Causes |
Prevents equipment failure and increases uptime |
Human Root Causes |
Reduces human errors and improves safety |
Latent Root Causes |
Addresses systemic issues and improves overall efficiency |
Analysis |
Provides insights for continuous improvement |
Knowledge Base |
Enhances organizational learning and problem-solving capabilities |
Table 4: The PROACT® Method and its Impact on Operational Excellence
PROACT® EASYRCA SOFTWARE
Our RCA software called EasyRCA allows analysts to conduct RCAs on any undesirable event or incident.Once we properly identify our root causes, we can make the appropriate corrective actions in the system, and communicate with our entire team.
1. Logic Trees
Logic Trees are tools that help us recreate the event backwards in time, allowing us to understand the root causes of our undesirable outcomes. Our PROACT® Software includes easy to use logic trees to help us think through events and drill down to the root causes behind them. Our logic trees allow analysts to fill in their Event and eventually uncover the Latent Roots of the event (or the underlying reasons for the improper decisions that were made that day).
Event = Undesirable Outcome
Mode = Factual Observation that Needs to be Explained
Hypothesis = Educated Guesses
Physical Root = Physical, Observable Consequence of Decision
Human Root = Decision Error
Latent Root = Reasoning or Rationale for Decision
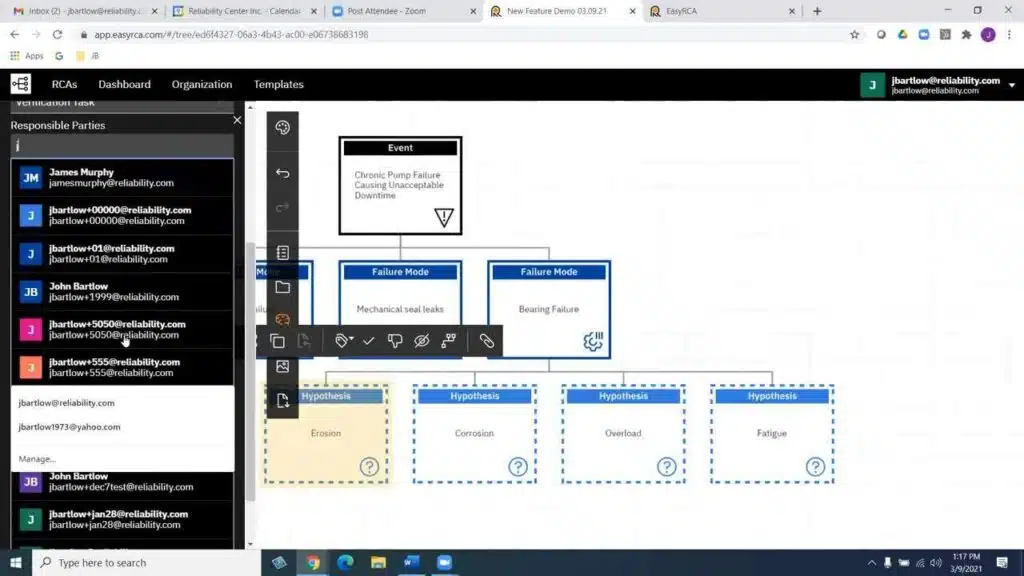
2. PROACT® Templates/RCA Knowledge Libraries
These are warehouses of cause-and-effect relationships aggregated from past analyses inside and outside the company, available OEM troubleshooting flow diagrams and other public domain resources. There are Industrial and Healthcare templates available that adapt to whichever RCA process the team is currently using (i.e. cause & effect, form-based, fishbone diagram, 5-whys, logic tree). The Templates only work correctly with the PROACT® Logic Tree. Search templates for hypotheses that you might have missed and easily incorporate them into your current analysis. Such libraries consist of templates for Mechanical, Electrical, Quality, Safety, and Human Error/Human Performance.
3. Cost Tracking
This allows our team to easily record all the costs associated with performing an RCA and compare numbers with the benefit realized as a result of our corrective actions to calculate our ROIs.
4. The PROACT® ROI Calculator
We developed the PROACT® ROI Calculator to enable those on the front lines to quickly make a business case for conducting an RCA on a chronic failure. Our RCA ROI calculator can instantly produce a line item justification based on the simple calculator of:
FREQUENCY OF OCCURRENCE/YR x IMPACT/OCCURRENCE (Manpower $ + Material $ + Downtime $)
5. Task Reminder Emails
These emails are sent to team members upon task assignment, and the appropriate management owner is copied on overdue alerts.
6. Customizable Company Branded Reports
Customizable Company Branded Reports can be created at any time for printing or saving as a pdf for implementation and future use. Customizable reports can be made for reporting to team members or for the Board of Directors, as each is interested in different information.
HOW DOES IT IMPACT ROI?
(PROACT® CASE STUDIES)
Are we reporting our RCA ROI’s back to our leaders to justify the existence of our RCA system? Our documented average ROI for our case study database is over 600%. Here are a few specific examples showing the financial impact the PROACT® approach can have on real businesses. These cases were published in our text entitled ‘Root Cause Analysis: Improving Performance for Bottom-Line Results’.
This means that in order for us to be able to publish these cases, the company legal department had to approve. For these reasons I would consider these numbers conservative! I also want to reiterate that these are NOT our successes, they are the successes of these teams and their corporations. In the end, ‘an analysis is only as good as the analyst’!
1. North American Paper Mill: North America
During a two year period, there were 19 failures on thick stock pumps on A and B units in the Bleach Room. Several attempts had been made to implement corrective actions for the pumps but ultimately failures were still occurring. Thick stock pumps are a big ticket item ranging from $60,000 to $120,000 per rebuild due to the tight clearances and amount of material it takes to machine the pumps. It was determined by maintenance that the pumps could be rebuilt in-house in the bleach room maintenance shop. This has been very successful and has cut the cost of maintenance dramatically and has proven to have had greater reliability. Performing the rebuild by internal millwrights has brought ownership and pride of the repairs and operations of the thick stock pumps. Although production loss was not used in the Opportunity Analysis (OA) for these failures, it would have been a significant factor in the loss equation for these events.
There are substantially less failures on these critical pumps and defects are caught before they cause catastrophic problems. In-house rebuild of pumps has resulted in greater ownership and pride in the performance of the pumps. Maintenance costs today are approximately $25,000 compared to roughly $500,000 during the previous two year time frame.
- Estimated Cost of Performing the Analysis: $20,000
- Approximate Savings:$700,000 per year
- Reduced account receivables and improved organizational effectiveness.
- Estimated ROI: 3500%
2. Eastman Chemical: World Headquarters, Kingsport, TN
Eastman Chemical senior management realized their level of customer complaints had not shown significant reduction during the past few years. This was troubling, given that Eastman had a strong history of continual improvement performance in their processes. Furthermore, one of the key objectives of Eastman’s Customer Complaint Handling Process was to investigate and identify the cause of complaints – evidently the complaint investigations were not as effective as expected.
- Elimination of half of Eastman’s level of customer complaints.
- Equated to about $2,000,000 on reduced complaint handling costs, reduced waste and rework.
- Reduced operating and maintenance costs from improved process and equipment reliability.
- Reduced account receivables and improved organizational effectiveness.
3. Lyondell-Citgo
Recurrent failures of vacuum column bottom pumps. Both pumps came on-line at the same time. The Mean Time Between Failure (MTBF) was very poor at three (3) months. Failures of mechanical seals, thrust bearings, impellers and case wear rings were very common. Most of the failures occurred at start-up. The system operates with one pump as a primary pump and the other as a spare pump. Different attempts to correct the above problems failed. There was not a good understanding of the causes of these failures and most important how they correlated to each other. At times, both pumps would not be available. The impact on production and the excessive maintenance costs resulted in management appointing a Root Cause Analysis (RCA) team to find and implement final solutions to these problems.
- Estimated Cost to Conduct RCA: $40,000
- Estimated Returns from RCA: $7,150,000
- Return On Total Investment: ~17,900%
CONCLUSION
The PROACT® (P3) method offers a comprehensive approach to root cause analysis. By identifying and addressing the physical, human, and latent root causes, it enables organizations to prevent recurring issues, reduce costs, and improve performance. By leveraging the root system, the analysis, and the knowledge base, the PROACT® method supports operational excellence and promotes a culture of continuous improvement. In the evolving reliability landscape, the PROACT® method is a powerful tool for proactive problem-solving and sustained success. With the keyword ‘PROACT’ in mind, it's clear that this method is a cornerstone of modern reliability and maintenance strategies.
Recent Posts
AI and Site Reliability Engineers: Lessons from the Field.
Smarter, Faster, Deeper: How AI Is Transforming Root Cause Analysis in Software and Beyond
North America’s Looming Power Shortfall: A Root Cause Analysis for the Grid—and Beyond
Preventing EV Charger Downtime: How Smart Test Strategies Act as Root Cause Analysis in Action
Root Cause Analysis Software
Our RCA software mobilizes your team to complete standardized RCA’s while giving you the enterprise-wide data you need to increase asset performance and keep your team safe.
Root Cause Analysis Training