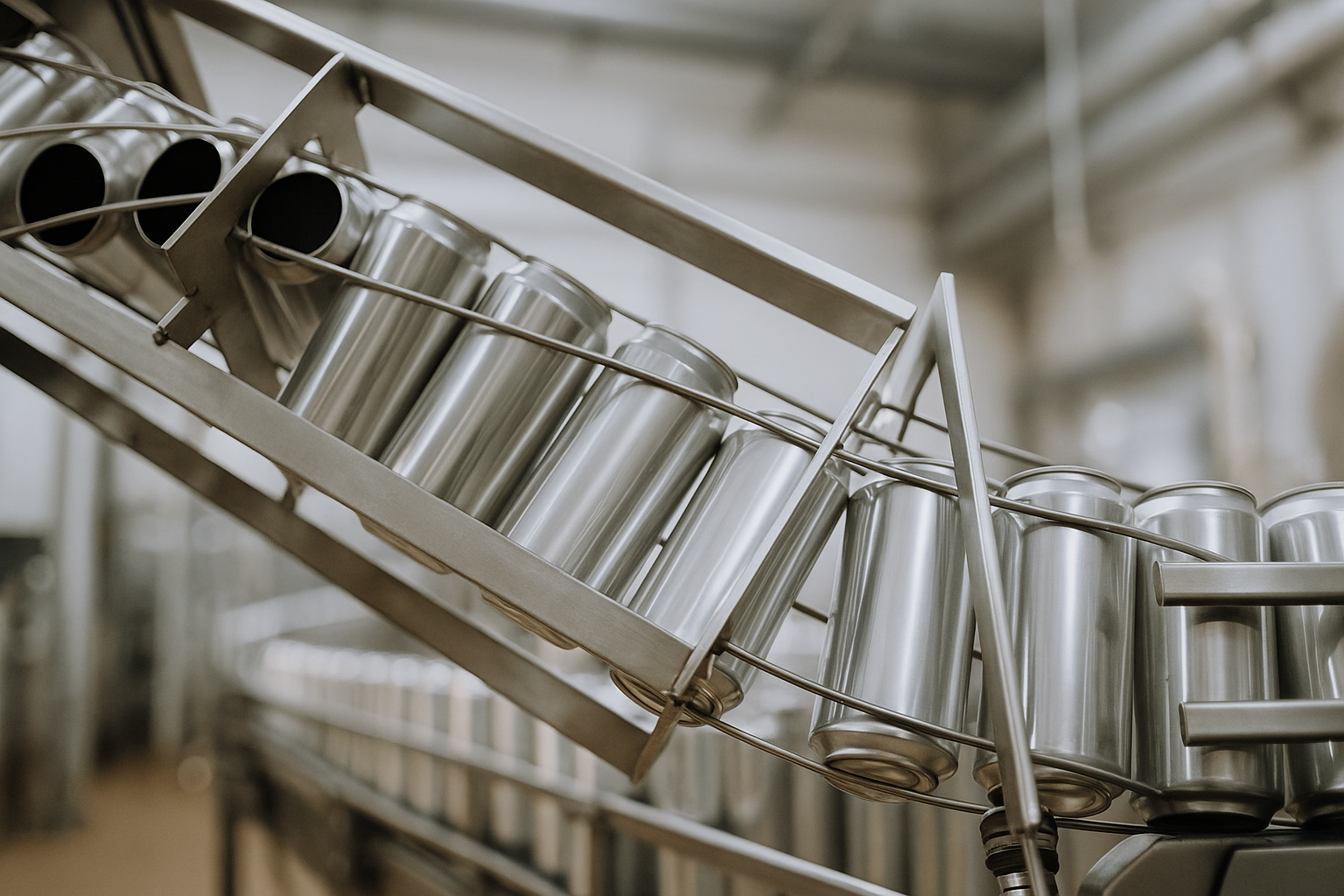
Using the 5 Whys Technique for Root Cause Analysis in Complex Environments
In today’s fast-paced business world, identifying, and solving problems efficiently is key to maintaining operational success. One method that has stood the test of time in uncovering the root cause of issues is the 5 Whys technique. Straightforward yet extremely effective, it helps teams drill down to the core of a problem by asking “why” multiple times until the root cause is apparent. However, applying the 5 Whys in complex environments—where issues are often multi-layered—requires a more structured approach.
In this blog post, we’ll explore how you can effectively use the 5 Whys technique for root cause analysis in complex settings and why it remains a go-to method for problem-solving.
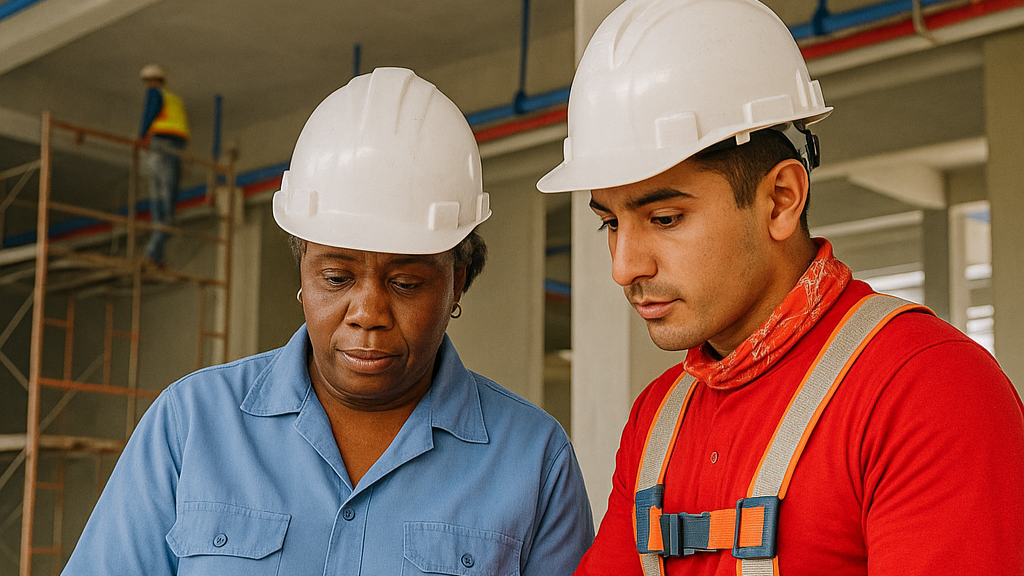
What is the 5 Whys Technique?
Let us first begin by understanding the 5 Whys technique. It is a problem-solving tool developed by Sakichi Toyoda, the founder of Toyota, as part of the Lean manufacturing philosophy. It involves asking “why” repeatedly—usually five times—to discover the root cause of a problem. The idea is that each “why” gets you closer to identifying and fixing the underlying issue, rather than just treating the symptoms.
Why Use the 5 Whys Technique in Complex Environments?
Complex environments, such as large organizations, multi-step manufacturing processes, or intricate IT systems, often present problems that have multiple contributing factors. Despite its simplicity, the 5 Whys can be a valuable tool in these settings because:
- It encourages critical thinking: Repeated questioning forces teams to think beyond the obvious.
- It reveals underlying issues: Surface-level problems are rarely the true cause of an issue, and the 5 Whys helps to uncover hidden factors.
- It’s easy to use: Unlike more complicated analysis tools, the 5 Whys requires no special software or training, making it accessible to any team.
How to Apply the 5 Whys Technique in Complex Environments
While the 5 Whys is quite straightforward, applying it in a complex environment requires some adjustments to maximize its effectiveness. Here’s a step-by-step guide:
1. Define the Problem Clearly
In complex environments, the first step is ensuring that everyone is on the same page regarding the problem. A vague or poorly defined issue can lead to a misleading analysis. Use a clear, concise problem statement. For example, instead of “system failure,” specify, “The system crashed during data processing.”
2. Assemble the Right Team
In complex systems, the problem may span multiple departments or functions. Assemble a diverse team with representatives from different areas to ensure all angles of the problem are covered. Include people directly involved with the problem, as well as those with broader perspectives who can see the bigger picture.
3. Ask the First Why
Begin by asking why the problem occurred in the first place. The first answer should focus on immediate or visible causes. For example, “Why did the system crash?” Answer: “Because the database is overloaded.”
4. Ask Additional Whys (Usually Five)
For each response, ask “why” again to dig deeper into the problem. In complex environments, you may need to go beyond five whys or take different paths as multiple causes emerge.
For example:
- Why did the system crash? The database is overloaded.
- Why did the database overload? It received too many requests simultaneously.
- Why did it receive too many requests? The load balancing system malfunctioned.
- Why did the load balancing system malfunction? It wasn’t properly configured for the new traffic patterns.
- Why wasn’t it configured correctly? The team didn’t have updated traffic forecasts during the last system update.
5. Identify the Root Cause
After asking the 5 Whys, the final answer should point to the root cause of the problem. This is the core issue that needs to be addressed to prevent recurrence. For example, the root cause is the failure to update traffic forecasts during system changes, which led to improper configuration of the load balancer.
6. Develop Corrective Actions
Once you’ve identified the root cause, the next step is to implement solutions to address it. This might involve process changes, system updates, or staff training. For example, going forward, ensure that traffic forecasts are updated regularly and integrated into system updates.
7. Document and Share Findings
In complex environments, documentation is essential for knowledge sharing and preventing future occurrences of similar problems. Create a detailed report outlining the problem, the 5 Whys analysis, and the corrective actions. Use a root cause analysis template to standardize reporting across teams.
Why the 5 Whys Technique Remains Effective
Despite the challenges, the 5 Whys technique remains a valuable tool for root cause analysis in complex environments because it promotes simplicity in tackling layered problems. When used with care and a collaborative team approach, it uncovers root causes that might otherwise go unnoticed, driving real solutions to critical issues.
Conclusion
The 5 Whys technique may seem simple, but its power lies in its ability to reveal the true source of problems, even in complex environments. By asking “why” multiple times, you can peel away the layers of symptoms to find the underlying cause, enabling more effective corrective actions. Whether you’re in manufacturing, IT, healthcare, or any other industry, using the 5 Whys for root cause analysis will help you create long-term solutions, reduce recurring issues, and improve overall performance.
Are you ready to implement the 5 Whys technique in your business? Start with a well-defined problem, keep asking “why,” and watch your problem-solving skills improve!
Key Takeaways:
- The 5 Whys technique is simple yet powerful for identifying root causes.
- In complex environments, ensure you define the problem clearly and involve a diverse team.
- Be prepared to encounter multiple root causes and avoid oversimplifying.
Recent Posts
AI and Site Reliability Engineers: Lessons from the Field.
Smarter, Faster, Deeper: How AI Is Transforming Root Cause Analysis in Software and Beyond
North America’s Looming Power Shortfall: A Root Cause Analysis for the Grid—and Beyond
Preventing EV Charger Downtime: How Smart Test Strategies Act as Root Cause Analysis in Action
Root Cause Analysis Software
Our RCA software mobilizes your team to complete standardized RCA’s while giving you the enterprise-wide data you need to increase asset performance and keep your team safe.
Root Cause Analysis Training