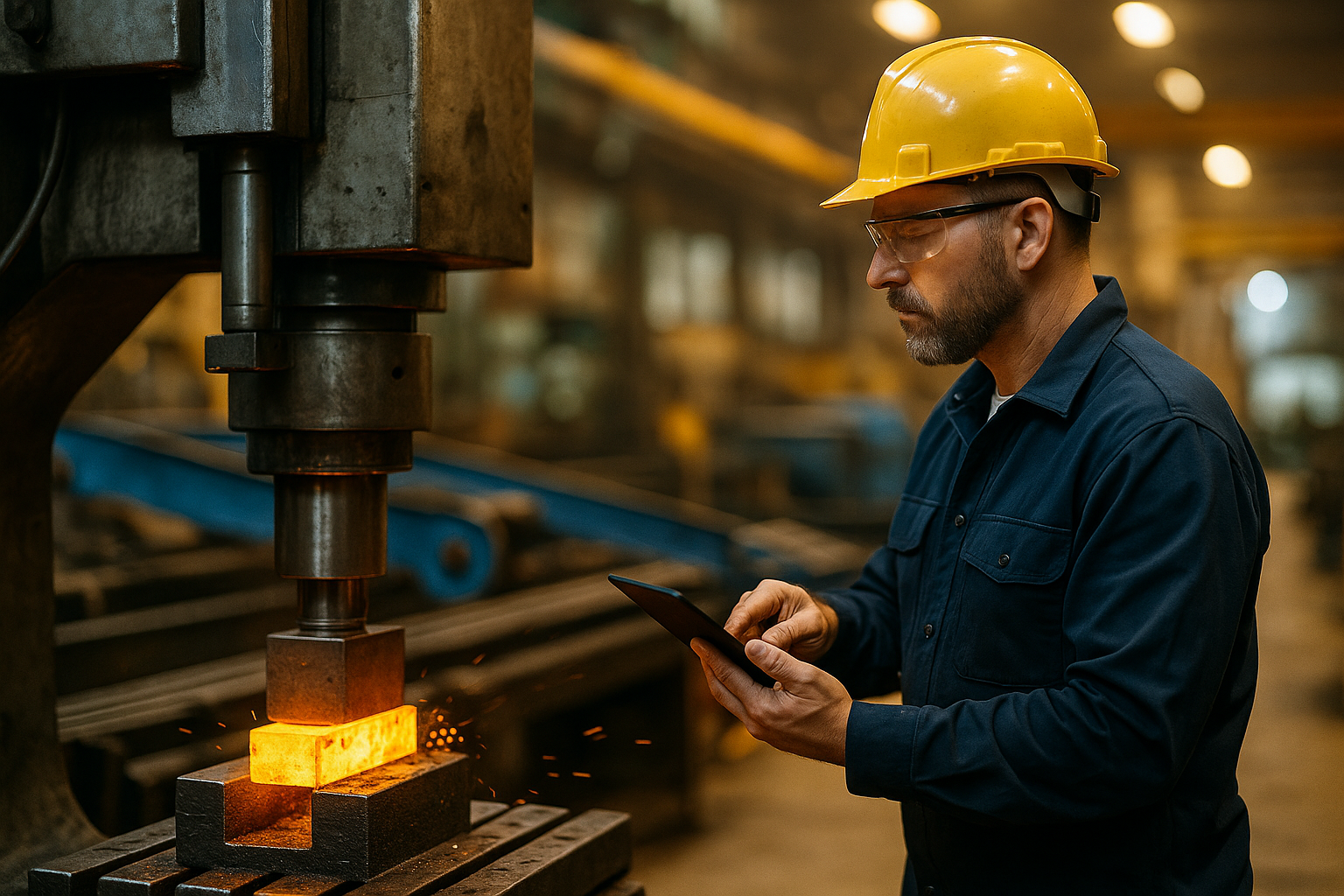
The Role of a Reliability Engineer in the Industrial and Manufacturing Sectors
In industries such as manufacturing, pharmaceuticals, and energy, equipment reliability is critical to maintaining efficiency, reducing downtime, and ensuring workplace safety. The Reliability Engineer plays a crucial role in achieving these objectives by focusing on preventive maintenance, failure analysis, and continuous improvement strategies.
What is a Reliability Engineer?
A Reliability Engineer is a professional dedicated to improving asset performance by minimizing equipment failures and maximizing operational efficiency. Unlike traditional maintenance personnel who primarily address reactive repairs, Reliability Engineers take a proactive approach by using data-driven techniques to prevent failures before they occur.
Key Responsibilities of a Reliability Engineer
- Failure Mode and Effects Analysis (FMEA): Reliability Engineers conduct FMEA to identify potential failure points in machinery and develop strategies to mitigate risks before they lead to costly breakdowns.
- Predictive and Preventive Maintenance: Using tools like vibration analysis, thermal imaging, and ultrasonic testing, Reliability Engineers anticipate equipment failures and schedule maintenance activities to extend asset lifespan.
- Root Cause Analysis (RCA): When failures do occur, Reliability Engineers perform root cause analysis (RCA) to determine why an issue happened and implement corrective measures to prevent recurrence.
- Asset Lifecycle Management: From equipment acquisition to decommissioning, Reliability Engineers ensure that assets are managed efficiently to maximize return on investment.
- Collaboration with Operations Teams: Reliability Engineers work closely with maintenance teams, operators, and production managers to implement best practices that improve system reliability and reduce unexpected downtime.
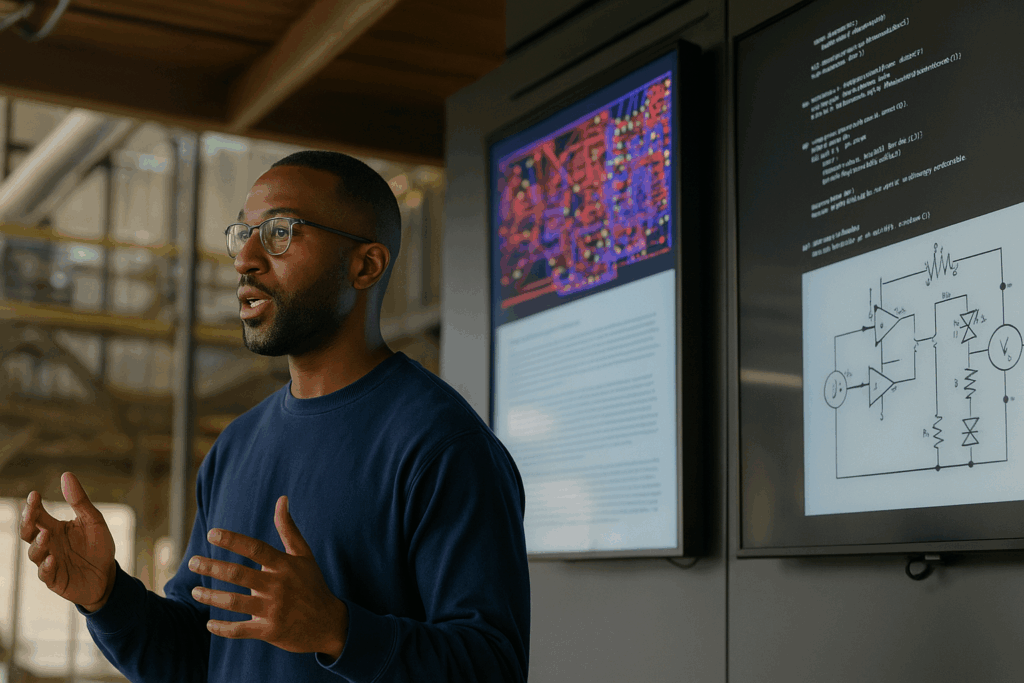
The Impact of Reliability Engineers on Business Operations
Through the work of Reliability Engineers, businesses can significantly reduce unplanned downtime, lower maintenance costs, and increase production efficiency. Reliability Engineers contribute to the long-term success of industries by ensuring that critical systems operate at peak performance while maintaining safety and regulatory compliance.
Conclusion
The role of a Reliability Engineer extends beyond just fixing equipment—it is about fostering a culture of continuous improvement, proactive maintenance, and strategic asset management. By integrating reliability engineering practices, organizations can enhance operational efficiency, extend the lifespan of critical assets, and ensure long-term business success.
Recent Posts
AI and Site Reliability Engineers: Lessons from the Field.
Smarter, Faster, Deeper: How AI Is Transforming Root Cause Analysis in Software and Beyond
North America’s Looming Power Shortfall: A Root Cause Analysis for the Grid—and Beyond
Preventing EV Charger Downtime: How Smart Test Strategies Act as Root Cause Analysis in Action
Root Cause Analysis Software
Our RCA software mobilizes your team to complete standardized RCA’s while giving you the enterprise-wide data you need to increase asset performance and keep your team safe.
Root Cause Analysis Training