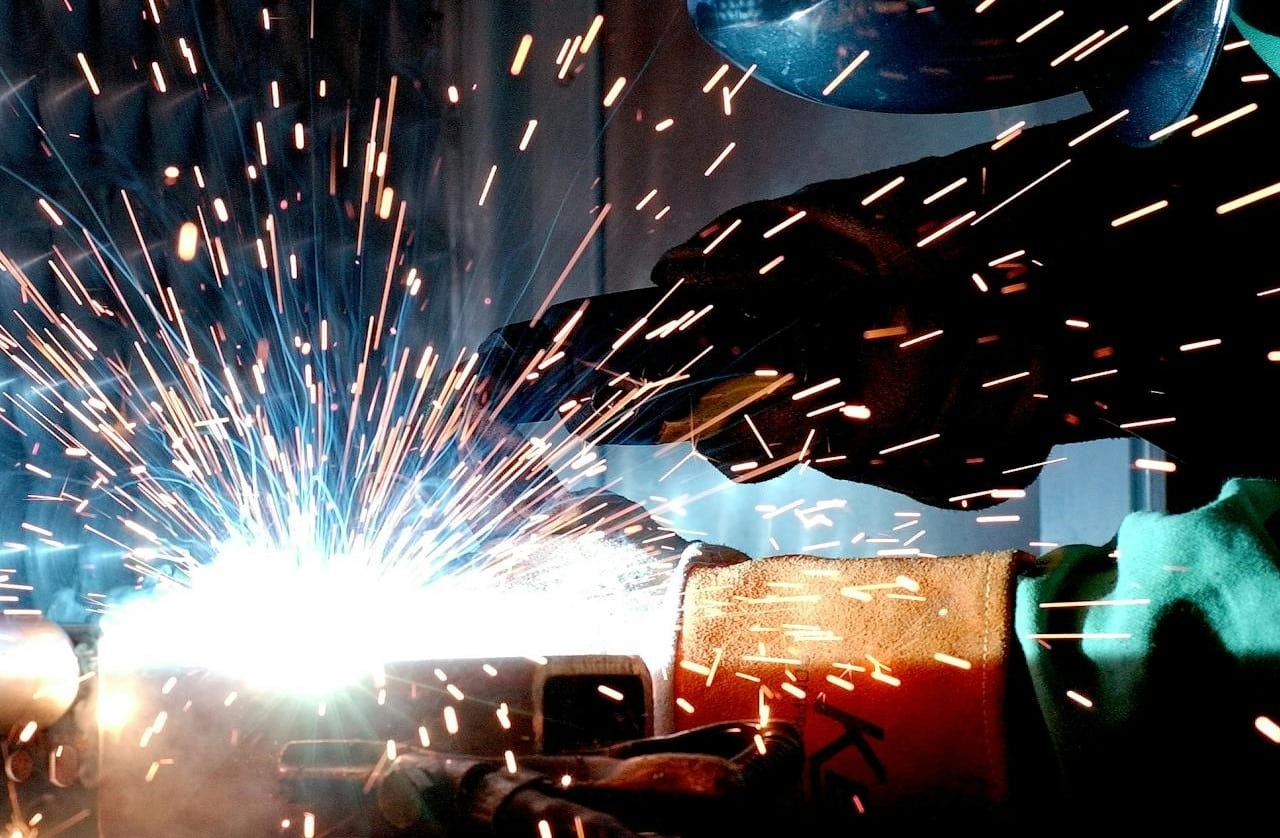
Post-Incident Analysis for Enhanced Reliability
With over two decades in business – spanning strategy consulting, tech startups and executive leadership – I am committed to helping your organization thrive.
At Reliability, we’re on a mission to help enhance strategic decision-making and operational excellence through the power of Root Cause Analysis, and I hope this article will be helpful!
Our goal is to help you better understand post-incident analysis by offering insights and practical tips based on years of experience. Whether you’re new to doing root cause analyses or a seasoned pro, we trust this will be useful in your journey towards working hard and working smart.
———————
When incidents occur in manufacturing plants, they often disrupt operations, jeopardize safety, and incur significant costs. To mitigate these impacts and prevent recurrence, performing a thorough post-incident analysis (PIA) is essential. This analysis mirrors the approach taken by fire departments and other emergency services, where examining the details of an incident can uncover critical lessons and improve future responses. For other industries, Root Cause Analysis (RCA) serves as an invaluable tool in this process, enabling organizations to systematically investigate failures and develop effective solutions.
Understanding Post-Incident Analysis
A Post-Incident Analysis (PIA) involves a detailed examination of incidents that result in significant operational disruption, safety hazards, or financial losses. Let’s take manufacturing as an example. Similar to the fire department’s PIA, manufacturing PIA focuses on identifying the root causes of failures, evaluating the effectiveness of response strategies, and learning from both successes and shortcomings. By doing so, manufacturers can enhance their reliability programs and foster a proactive approach to problem-solving.
Steps to Conduct a Post-Incident Analysis in Manufacturing
1. Incident Overview
Begin by providing a comprehensive overview of the incident. This should include details such as the type of incident, location, time of occurrence, equipment involved, and initial conditions. For example, if a critical machine failure caused a production halt, describe the machine, its operational state prior to the failure, and any unusual conditions that may have contributed to the incident.
2. Data Collection
Effective PIA requires accurate and detailed data collection. This includes gathering information on the incident timeline, equipment status, environmental conditions, and personnel actions. Employing techniques such as the 5-Why Analysis can help uncover the underlying causes of the incident by repeatedly asking “Why?” until the root cause is identified. Utilizing tools like EasyRCA software can streamline this process and ensure a fact-based investigation.
3. Root Cause Identification
The core of the PIA lies in identifying the root causes of the incident. This involves analyzing the collected data to pinpoint the fundamental issues that led to the failure. The PROACT® RCA methodology is particularly effective here, as it helps categorize root causes into physical, human, and latent categories. This comprehensive approach ensures that all contributing factors are considered, from mechanical breakdowns to human errors and organizational deficiencies.
4. Evaluation of Response
Assess the effectiveness of the immediate response to the incident. Were the right procedures followed? Did the response teams have adequate resources and training? Evaluate whether the actions taken mitigated the impact of the incident or if there were areas where improvements are needed. This step helps refine emergency response plans and ensures better preparedness for future incidents.
5. Documentation and Communication
Thoroughly document the findings of the PIA, including the identified root causes, response evaluation, and recommended corrective actions. Clear and detailed documentation serves as an educational tool for all personnel and a reference for future incidents. Communicate the findings to relevant stakeholders, ensuring everyone understands the lessons learned and the steps required to prevent recurrence.
6. Implementing Corrective Actions
Develop and implement corrective actions based on the PIA findings. This may involve technical modifications to equipment, changes in operational procedures, enhanced training programs, or improvements in safety protocols. The goal is to address the root causes effectively and create a safer, more reliable manufacturing environment.
7. Continuous Improvement
Post-incident analysis should be an ongoing process, with each incident providing opportunities for continuous improvement. Regularly review and update PIA procedures, incorporate new insights, and adapt to evolving operational challenges. Cultivating a culture of continuous improvement ensures that the organization remains proactive in identifying and addressing potential issues before they escalate into major incidents.
Example of Applying PIA in a Manufacturing Environment
Consider a scenario where a manufacturing plant experiences a significant equipment failure that halts production for several hours. The PIA process would unfold as follows:
- Incident Overview
A high-speed packaging machine malfunctioned, causing a production stoppage. The incident occurred during a high-demand period, exacerbating its impact on operations. Initial inspection revealed damage to critical machine components.
- Data Collection
Data is collected from various sources, including machine logs, maintenance records, operator testimonies, and environmental conditions at the time of the failure. Using the 5-Why Analysis, investigators repeatedly ask “Why?” to trace the failure back to its root causes.
- Root Cause Identification
Analysis reveals that the failure was caused by inadequate lubrication of a critical component, which led to excessive wear and eventual breakdown. Further investigation uncovers that the lubrication schedule was not properly followed due to a lack of training and oversight.
- Evaluation of Response
The immediate response involved shutting down the machine and initiating repairs. However, the response team faced delays due to a lack of readily available spare parts and unclear communication protocols. This highlights the need for improved inventory management and streamlined communication channels.
- Documentation and Communication
The findings are documented in a detailed PIA report, which is shared with maintenance teams, operators, and management. The report includes a root cause analysis, response evaluation, and recommended actions to prevent similar incidents. This is where tools like EasyRCA are invaluable.
- Implementing Corrective Actions
Corrective actions include revising the lubrication schedule, providing additional training to maintenance personnel, and improving spare parts inventory management. Additionally, communication protocols are updated to ensure quicker and more efficient responses to future incidents.
- Continuous Improvement
The plant schedules regular reviews of the lubrication schedule and maintenance practices. Feedback from these reviews is used to make further adjustments, fostering a culture of continuous improvement and proactive problem-solving.
Benefits of Post-Incident Analysis and Root Cause Analysis
- Enhanced Reliability
By systematically identifying and addressing the root causes of failures, manufacturers can significantly enhance the reliability of their equipment and processes. This leads to fewer unexpected breakdowns, reduced downtime, and improved overall operational efficiency.
- Improved Safety
Effective PIA helps identify and mitigate safety risks associated with manufacturing operations. By understanding the root causes of incidents, organizations can implement measures to prevent accidents and protect the well-being of their employees.
- Cost Savings
Preventing recurring issues through thorough RCA can result in substantial cost savings. Reduced downtime, fewer repairs, and minimized waste all contribute to a more cost-effective manufacturing process.
- Knowledge Sharing
PIA provides valuable lessons that can be shared across the organization. By documenting and communicating findings, manufacturers can foster a learning culture where best practices are disseminated, and continuous improvement is prioritized.
- Proactive Problem-Solving
Transitioning from a reactive to a proactive approach is a key benefit of PIA and RCA. By focusing on preventing incidents rather than merely responding to them, manufacturers can create a more resilient and efficient operation.
Conclusion
By systematically investigating incidents, identifying root causes, and implementing corrective actions, manufacturers can enhance safety, reduce costs, and foster a culture of continuous improvement. As with the Swiss Cheese Model used in risk management, layering multiple defenses and addressing vulnerabilities ensures a robust and resilient manufacturing process. Embracing these practices not only mitigates risks but also drives operational excellence and long-term success.
For more insights and resources on Root Cause Analysis and manufacturing reliability, visit our Reliability Resources and explore the various training programs and tools available to support your continuous improvement journey.
___________
I hope you found this post-incident analysis article insightful and actionable! Stay tuned for more thought-provoking articles as we continue to share our knowledge. Success is rooted in a thorough understanding and consistent application, and we hope this article was a step in unlocking the full potential of Root Cause Analysis for your organization.
Reliability runs initiatives such as an online learning center focused on the proprietary PROACT® RCA methodology and EasyRCA.com software.
Recent Posts
AI and Site Reliability Engineers: Lessons from the Field.
Smarter, Faster, Deeper: How AI Is Transforming Root Cause Analysis in Software and Beyond
North America’s Looming Power Shortfall: A Root Cause Analysis for the Grid—and Beyond
Preventing EV Charger Downtime: How Smart Test Strategies Act as Root Cause Analysis in Action
Root Cause Analysis Software
Our RCA software mobilizes your team to complete standardized RCA’s while giving you the enterprise-wide data you need to increase asset performance and keep your team safe.
Root Cause Analysis Training