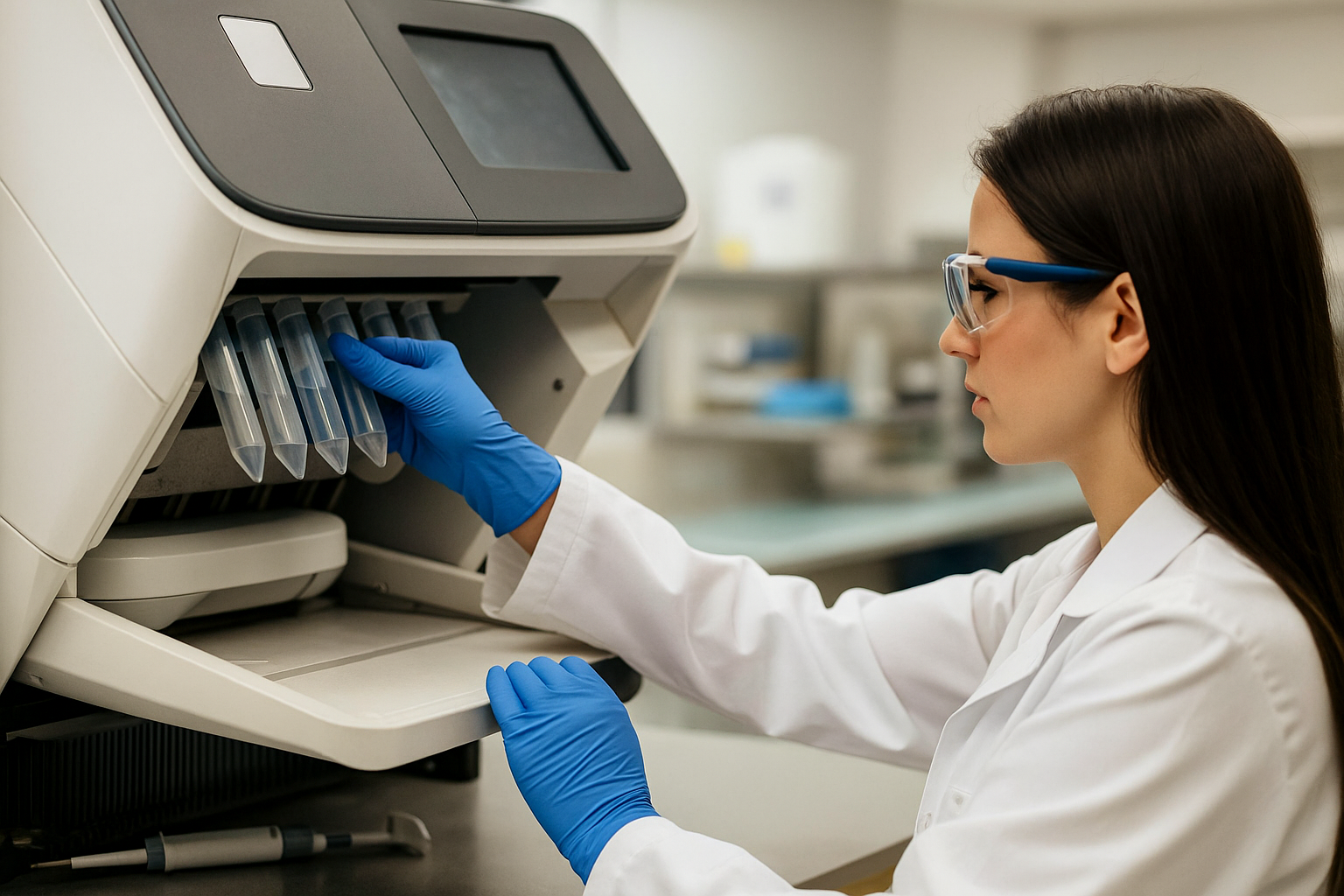
How Root Cause Analysis Tools Can Prevent Equipment Failures in Healthcare
In the fast-paced world of healthcare, where it’s a matter of life and death, equipment failures can have serious consequences. When an important machine stops working, it can jeopardize patient safety, disrupt care, and even put life on the line. Fortunately, Root Cause Analysis (RCA) tools can help healthcare professionals identify and prevent these failures before they occur. Let’s explore how these tools work and why they are essential for running healthcare facilities smoothly.

Understanding Root Cause Analysis
Root Cause Analysis is a method used to uncover the underlying reasons for problems, such as equipment failures. Instead of just fixing the issue at hand, RCA helps healthcare teams understand what caused it in the first place. By addressing the source of the problem, they can implement solutions that prevent similar issues from arising in the future.
Key RCA Tools for Preventing Equipment Failures
1. Fishbone Diagram

The Fishbone Diagram, or the Ishikawa Diagram, is a visual tool that helps teams categorize potential causes of equipment failures. By mapping out different factors—like people, processes, equipment, and environment—healthcare professionals can pinpoint where issues might arise.
Why It Works: This visual representation helps us see connections and identify the most significant factors contributing to equipment problems.
2. 5 Whys Technique

The 5 Whys technique is a simple yet powerful tool that asks “why” repeatedly (typically five times) to dig deeper into the cause of a failure. For example, if a defibrillator fails, you might ask why it wasn’t functioning, why it wasn’t checked, and so on.
Why It Works: This method encourages critical thinking and helps uncover the root cause rather than just addressing the symptoms.
3. Failure Mode and Effects Analysis (FMEA)

FMEA is a proactive approach that identifies potential failure points in equipment before they lead to problems. Healthcare teams can prioritize risks and implement preventive measures by evaluating each process step.
Why It Works: FMEA helps healthcare facilities stay one step ahead, reducing the likelihood of equipment failures that could disrupt patient care.
4. Process Mapping

Process mapping involves creating a visual flowchart of how equipment is used and maintained. By detailing each step, healthcare teams can spot inefficiencies and areas where failures might occur.
Why It Works: A clear visual map helps identify bottlenecks and improve workflows, leading to more reliable equipment operation.
5. RCA Software Solutions
Specialized software designed for RCA can streamline the process of collecting data, analyzing incidents, and tracking improvements. These tools help healthcare teams collaborate and maintain accurate records of equipment performance and maintenance.
Why It Works: Centralizing data allows for easier identification of patterns and trends, leading to more effective prevention strategies.
Conclusion
Root Cause Analysis tools are essential for preventing equipment failures in healthcare settings. By utilizing tools like fishbone diagrams, the 5 Whys technique, FMEA, process mapping, and specialized software, healthcare professionals can identify root causes and implement effective solutions.
This proactive approach enhances patient safety and ensures that healthcare facilities can provide consistent, high-quality care. By investing in RCA, healthcare teams demonstrate their commitment to protecting patients and improving outcomes, ultimately fostering a culture of safety and reliability.
Recent Posts
AI and Site Reliability Engineers: Lessons from the Field.
Smarter, Faster, Deeper: How AI Is Transforming Root Cause Analysis in Software and Beyond
North America’s Looming Power Shortfall: A Root Cause Analysis for the Grid—and Beyond
Preventing EV Charger Downtime: How Smart Test Strategies Act as Root Cause Analysis in Action
Root Cause Analysis Software
Our RCA software mobilizes your team to complete standardized RCA’s while giving you the enterprise-wide data you need to increase asset performance and keep your team safe.
Root Cause Analysis Training