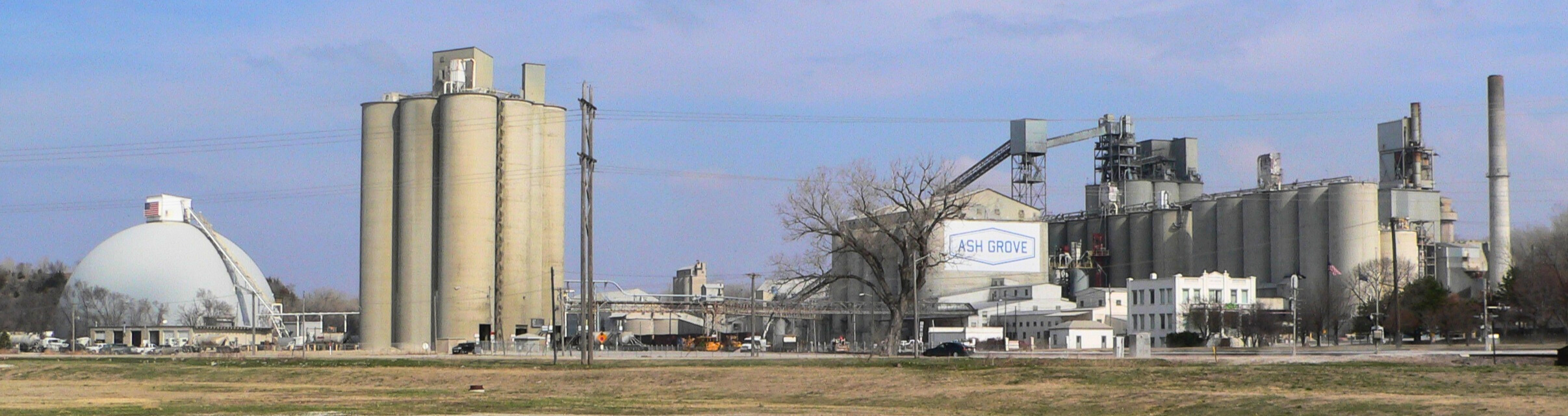
Case Study: Ash Grove Cement’s Enhanced Reliability with EasyRCA
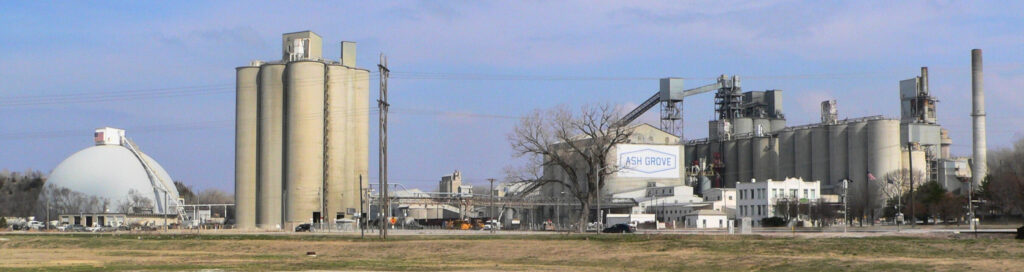
Company Overview
Ash Grove Cement, a leading North American producer of cement with 12 manufacturing plants and 41 distribution terminals across the U.S. and Canada, is committed to enhancing its operational efficiency, reliability, and safety across its facilities. As part of their continuous improvement efforts, Ash Grove Cement implemented EasyRCA, a web-based root cause analysis (RCA) software, to address challenges with tracking and resolving recurring equipment issues.
Challenges with Previous RCA System
Prior to adopting EasyRCA, Ash Grove Cement relied on a traditional CMMS with a basic RCA module, which didn’t meet their needs for effectively tracking and completing root cause investigations. Edwin Gutierrez, Corporate Reliability Engineer, noticed that employees were using troubleshooting techniques instead of engaging in full RCA investigations, leaving root causes unaddressed. “I found out that nobody was able to complete a root cause analysis because the software was designed for different concepts,” Gutierrez stated. The result was an inability to systematically prevent recurring equipment failures and minimize downtime.
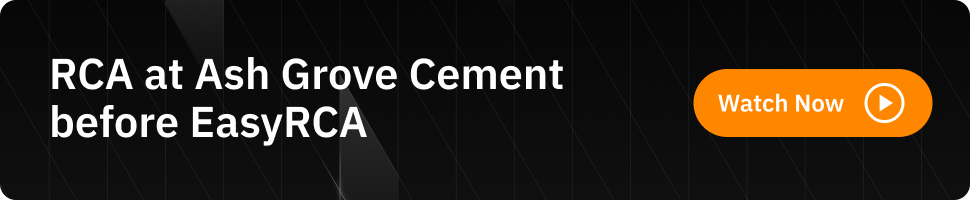
Choosing EasyRCA
In search of a more structured solution, Ash Grove Cement turned to EasyRCA. Gutierrez explained, “What we were looking for was an RCA tool that was easy to use, intuitive, and could track corrective actions—something that wasn’t part of our previous system.” The software’s simple interface and ability to integrate corrective actions into the RCA process were key selling points. “We can now track action items for each RCA investigation, ensuring accountability across our teams.”
Implementation and Training
Gutierrez played a pivotal role in implementing EasyRCA across Ash Grove Cement’s plants. “I traveled to the plants to teach the teams how to conduct a thorough root cause analysis using the software,” he said. His training emphasized moving beyond troubleshooting to a more thorough and systematic approach to identifying root causes.
Key Benefits
The implementation of EasyRCA has delivered several tangible benefits:
- Measurable Improvements: In just 10 months, Ash Grove Cement has seen a reduction in unplanned downtime. More than 140 RCAs have been completed, indicating widespread adoption of the tool across the company.
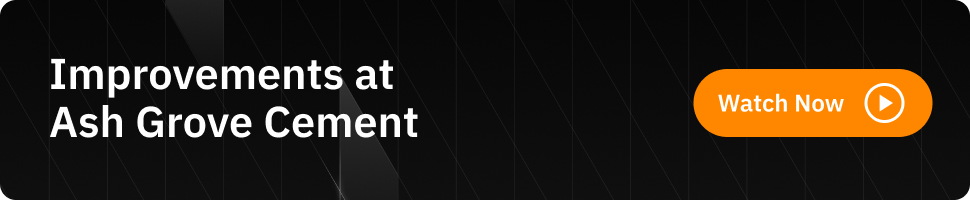
- Improved Action Tracking: Before EasyRCA, there was no formal way to track corrective actions. Now, the team can see which actions are pending, who’s responsible, and how far along they are.
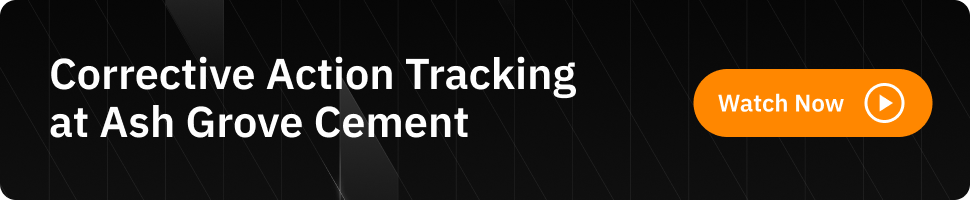
- Increased Accountability: Teams now own their RCA investigations, leading to more reliable outcomes. “It’s much easier to hold people accountable with this system,” Gutierrez said.
Expanding Beyond Reliability
Initially, EasyRCA was used for maintenance-related investigations, but its utility has extended into safety and quality control as well. “We’ve used the software for safety incidents and quality issues,” Gutierrez said. This cross-functional use has contributed to a more integrated approach to problem-solving within Ash Grove Cement.
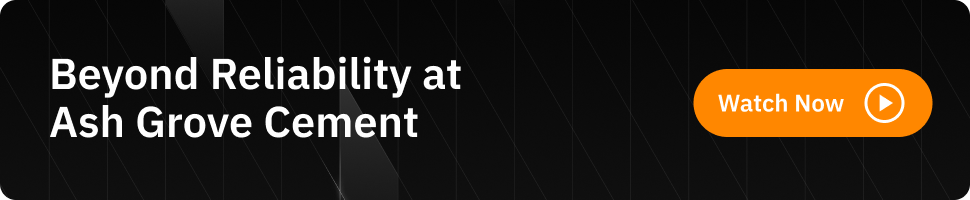
Future Outlook
Looking ahead, Gutierrez is excited about new features like AI-driven root cause suggestions, which have helped the team identify potential causes faster. “Before, I would reference a bibliography to check possible causes. Now, the AI does that for me, saving time,” he said. However, he cautioned that AI suggestions should still be verified by experts to ensure accuracy.
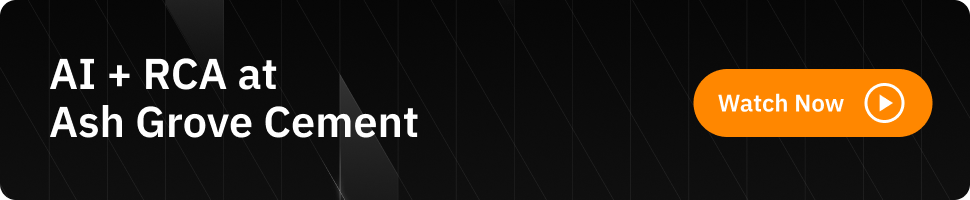
Advice to Other Teams
Gutierrez advises other teams considering EasyRCA to focus on proper implementation and training. “The most challenging part is training people who can facilitate RCA investigations effectively,” he said. “Without strong facilitators, the RCA process won’t be as effective.”
Conclusion
EasyRCA has transformed Ash Grove Cement’s approach to root cause analysis, making it easier to identify and resolve issues while ensuring accountability and continuous improvement. By integrating the tool across reliability, safety, and quality control, Ash Grove Cement has created a more holistic and efficient reliability program, setting a high standard for the cement industry.
Interested in Learning More?
If you’re ready to enhance your root cause analysis process like Ash Grove Cement, we invite you to request a demo of EasyRCA or explore our Root Cause Analysis training opportunities. Our team can show you how EasyRCA can help streamline investigations, improve accountability, and reduce unplanned downtime in your organization. Contact us today to get started!
Watch the full interview with Edwin Gutierrez on our YouTube channel or listen on Spotify to learn more about how EasyRCA has transformed Ash Grove Cement’s approach to reliability. Gain deeper insights into their experience and see how you can apply these strategies in your own organization.
Recent Posts
AI and Site Reliability Engineers: Lessons from the Field.
Smarter, Faster, Deeper: How AI Is Transforming Root Cause Analysis in Software and Beyond
North America’s Looming Power Shortfall: A Root Cause Analysis for the Grid—and Beyond
Preventing EV Charger Downtime: How Smart Test Strategies Act as Root Cause Analysis in Action
Root Cause Analysis Software
Our RCA software mobilizes your team to complete standardized RCA’s while giving you the enterprise-wide data you need to increase asset performance and keep your team safe.
Root Cause Analysis Training