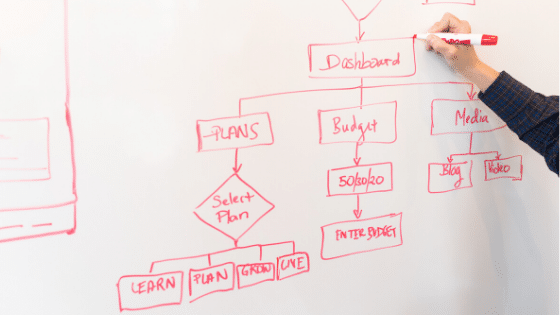
Should a Procedure = Practice?
Should a Procedure = Practice?
Recent Posts
UK Retail Cyberattacks: What M&S, Harrods & Co-op Reveal About Cybersecurity and Root Cause Analysis
Richmond Water Crisis Exposes Infrastructure Vulnerabilities: Why RCA Is Key to Long-Term Solutions
Introducing RCA Turbo: Instant Root Cause Analysis with a Snap or a Sentence
Unpacking the Iberian Peninsula Blackout: How Root Cause Analysis Can Illuminate Grid Vulnerabilities
Root Cause Analysis Software
Our RCA software mobilizes your team to complete standardized RCA’s while giving you the enterprise-wide data you need to increase asset performance and keep your team safe.
Request Team Trial
Root Cause Analysis Training
Your team needs a common methodology and plan to execute effective RCA's. With both in-person and on-demand options, our expert trainers will align and equip your team to complete RCA's better and faster.
View RCA Courses
Reliability's root cause analysis training and RCA software can quickly help your team capture ROI, increase asset uptime, and ensure safety.
Contact us for more information: