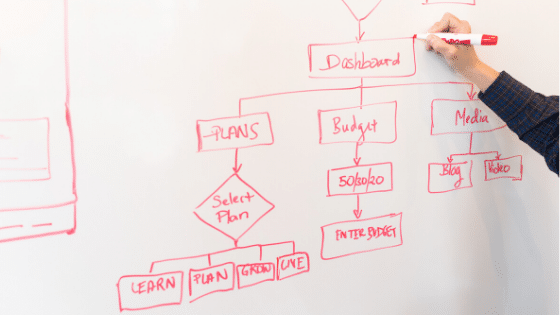
Should a Procedure = Practice?
Should a Procedure = Practice?
Recent Posts
AI and Site Reliability Engineers: Lessons from the Field.
Smarter, Faster, Deeper: How AI Is Transforming Root Cause Analysis in Software and Beyond
North America’s Looming Power Shortfall: A Root Cause Analysis for the Grid—and Beyond
Preventing EV Charger Downtime: How Smart Test Strategies Act as Root Cause Analysis in Action
Root Cause Analysis Software
Our RCA software mobilizes your team to complete standardized RCA’s while giving you the enterprise-wide data you need to increase asset performance and keep your team safe.
Request Team Trial
Root Cause Analysis Training
Your team needs a common methodology and plan to execute effective RCA's. With both in-person and on-demand options, our expert trainers will align and equip your team to complete RCA's better and faster.
View RCA Courses
Reliability's root cause analysis training and RCA software can quickly help your team capture ROI, increase asset uptime, and ensure safety.
Contact us for more information: