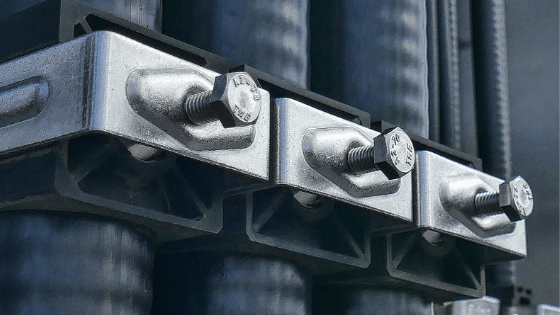
Questions About Coefficient of Friction in Fasteners
Questions About Coefficient of Friction in Fasteners
I recently received an interesting LI inquiry that I felt others could learn from the answers that I was able to get. This is not my expertise so I sought out answers from some colleagues who were more familiar with fasteners.
Here is the original inquiry (translated from Portuguese so I hope Google Translator did a good job):
“I would like to know if you can help me clarify my doubts about:
- The purpose of conducting a study of the coefficients of friction in screws, threads and nuts?
- Is there an accurate standard for such testing?
- What methods can be perfected in projects that target this type of trial and application?
- Can surface treatments influence changes in results?
- Who is responsible for such testing (the manufacturers and suppliers of raw materials, the assembler and/or its various final assembly applications)?
I first checked with our Ron Hughes (Sr. Reliability Consultant at Reliability Center, Inc):
“This is an excellent question as these highly engineered mechanical assemblies are often put in by “rule-of-thumb” rather than the slide rule mentality for which they are designed.
Mechanical fastener assemblies have been studied by the nuclear power industry for years and the derived coefficient of friction for the threads of these assemblies has indeed provided much needed quality assurance on safety related items. Testing in accordance with recommended ASTM and SAE standards is the quality control portion of the quality assurance program and is dome by the manufacturer of the fasteners. The ASME has worked closely with ASTM and SAE for decades on this program and many documents have been written on the subject.
The purpose is quite simple, what you are actually measuring is the slip resistance of the faying (contact) surfaces of the components being assembled. Torque ensures that the assembly is tensioned enough to maintain an adequate slip resistance. For steel bolts the general rule is that for every 0.001″ of stretch (tension) you put on a bolt you increase the clamping force (and thus the slip resistance) by approximately 3,000 psi of internal tension in the bolt.
Always remember that the coefficients are for new bolt threads that are non-lubricated and have never been previously tensioned (this changes the coefficients significantly). Field verification is done by proper torquing operations and by measuring break-away- torque when necessary.
It is good to remember that the torque values change after assembly. The initial assembly is the pre-load and the working load (or actual load) is only seen during operations. Some mechanical fastener assemblies will loosen and some tighten during working load.
The installer is responsible for making sure that the assembly has been made properly and the proper slip resistance has been achieved. Things to consider are as follows:
- Coatings such as zinc, cadmium plating, never-seize, etc. on the bolts change the slip resistance and must be accounted for.
- National coarse, fine and standard have different coefficients as the actual amount contact between the surfaces of the male and female differ.
- Type of thread (cut, rolled, ACME, etc.) is an important consideration due to the amount of contact.
- Die-electric properties of the materials to prevent fretting or Crevice Corrosion.
- Dynamic versus static loading conditions.
I then checked with a valued friend and colleague, Allan McNally (turbo-machinery expert currently working as a contractor in KSA):
1.0 The lubricant manufacturer typically provides the coefficient of friction stating a temperature range and various loads applications. I am going to assume the manufacturer does research and testing of the lubrication under various conditions following different controlled tightening procedures since they are willing to provide such information.
2.0 The only standards that I know about in relation to fasteners and torque/clamping force results (using lubricants as inputs in the testing process) include VDI 2230 and ISO 16047. However, both standards have specific definitions as to when they can be used.
3.0 Surface treatments CAN influence the results as the asperities for different materials create different lubrication boundaries.
4.0 I am not sure who is responsible for such testing, but in my experience equipment manufacturers typically provide a list of preferred lubricants to be used on equipment that must have bolted joints based on given conditions; therefore, I am assuming testing is done in the design and prototype faces to determine what lubricant provides the best results. The lubricant has various roles besides power transmission therefore the test may vary in each individual case.
5.0 The book (https://www.amazon.com/Introduction-Design-Behavior-Mechanical-Engineering/dp/0824792971) is an excellent source that helps understand joint design and the various factors that affect the design. I would refer those interested to this book as I haven’t found nothing better in the market. I once used the book to solve a failure and sure enough it helped a lot (solved the problem and the OEM paid for the damage).
For the other experts that are reading these responses, please chime in with your expertise so we can provide interested readers as much accurate info as possible.
I hate to let this great information go to waste by not letting as many people as possible learn from it!!!
About the Author
Robert (Bob) J. Latino is former CEO of Reliability Center, Inc. a company that helps teams and companies do RCAs with excellence. Bob has been facilitating RCA and FMEA analyses with his clientele around the world for over 35 years and has taught over 10,000 students in the PROACT® methodology.
Bob is co-author of numerous articles and has led seminars and workshops on FMEA, Opportunity Analysis and RCA, as well as co-designer of the award winning PROACT® Investigation Management Software solution. He has authored or co-authored six (6) books related to RCA and Reliability in both manufacturing and in healthcare and is a frequent speaker on the topic at domestic and international trade conferences.
Bob has applied the PROACT® methodology to a diverse set of problems and industries, including a published paper in the field of Counter Terrorism entitled, “The Application of PROACT® RCA to Terrorism/Counter Terrorism Related Events.”
Recent Posts
UK Retail Cyberattacks: What M&S, Harrods & Co-op Reveal About Cybersecurity and Root Cause Analysis
Richmond Water Crisis Exposes Infrastructure Vulnerabilities: Why RCA Is Key to Long-Term Solutions
Introducing RCA Turbo: Instant Root Cause Analysis with a Snap or a Sentence
Unpacking the Iberian Peninsula Blackout: How Root Cause Analysis Can Illuminate Grid Vulnerabilities
Root Cause Analysis Software
Our RCA software mobilizes your team to complete standardized RCA’s while giving you the enterprise-wide data you need to increase asset performance and keep your team safe.
Root Cause Analysis Training