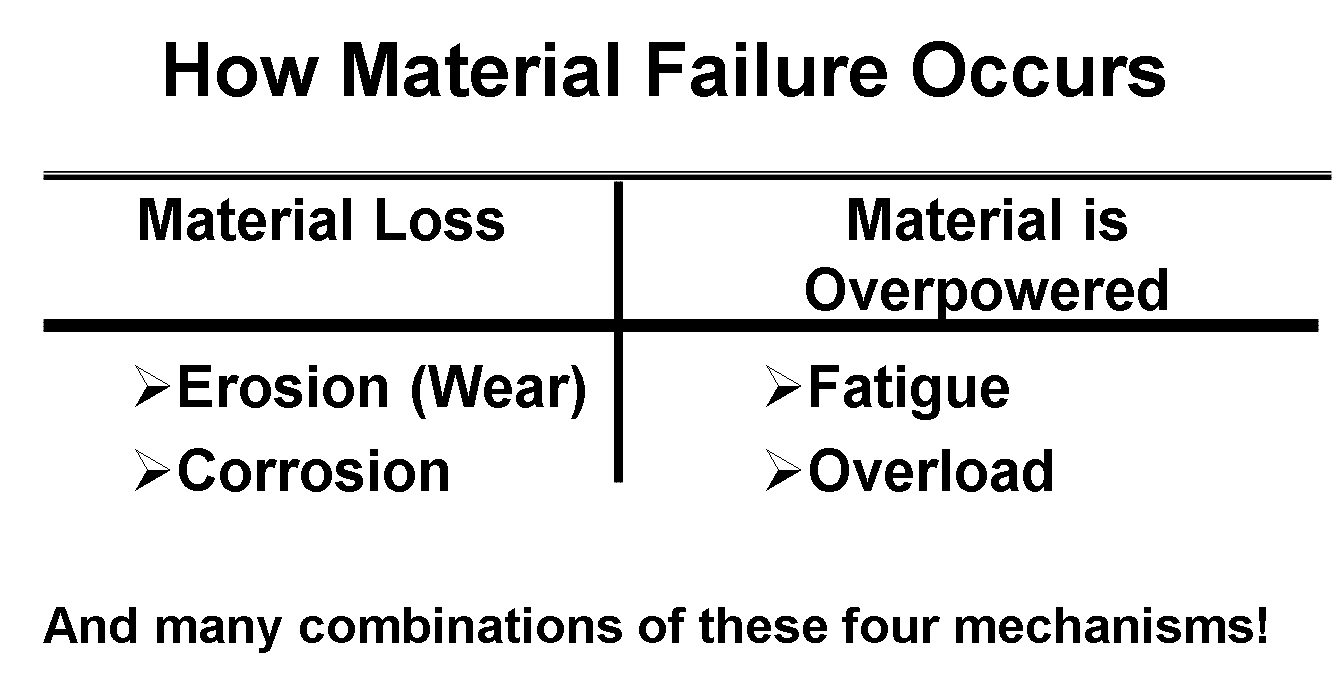
Fatigue & Overload: Part II, 4 Mechanisms of Component Failure
Author’s Note: I want to reiterate that this Series about reading the basic fracture surfaces, is for novices who often come into contact with such failed components. This Series is about the basics (101), and is intended to give readers an appreciation for the value of such ‘broken’ parts to an effective investigation/RCA. While this information will be rudimentary to seasoned materials engineers, I know they will all appreciate heightening awareness to the need to retain such failed parts for analysis, versus throwing them away and just replacing the part. Throwing away failed parts is a recipe for a repeat failure, when one does not understand why the part failed in the first place.
In Part I of this series we focused on Erosion and Corrosion as the the first two (2) basic failure mechanisms of component failure. When Erosion and Corrosion are apparent, there is generally a loss of metal in some form or fashion.
How Material Failure Occurs
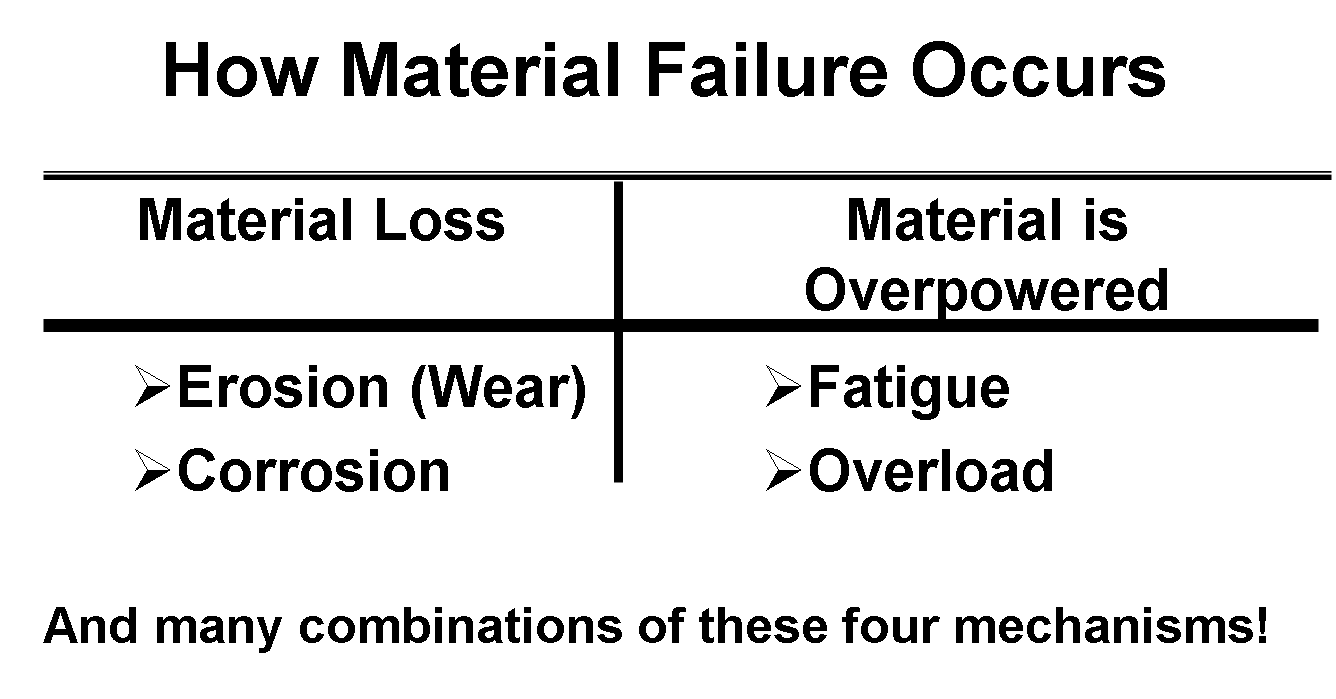
In this follow-up, we will focus on Fatigue and Overload, where generally the material is overpowered. Because these are such important topics by themselves, in my continuing interest to provide such information in digestible chunks, I will break Fatigue and Overload up into two separate blogs (Part III will focus on Overload by itself).
Let’s focus on Fatigue, since fatigue is the most common fracture pattern in about 90% of the cases.
Component Fatigue
- Fatigue occurs when a material is subjected to repeated loading and unloading.
- When the loads are above a certain threshold, microscopic cracks will begin to form at a material’s surface.
- Cracks always begin in high stressed areas of a material.
- Eventually a crack will reach a critical size, and the structure will suddenly fracture.
This graphic (Figure 1) demonstrates a classic case of fatigue.
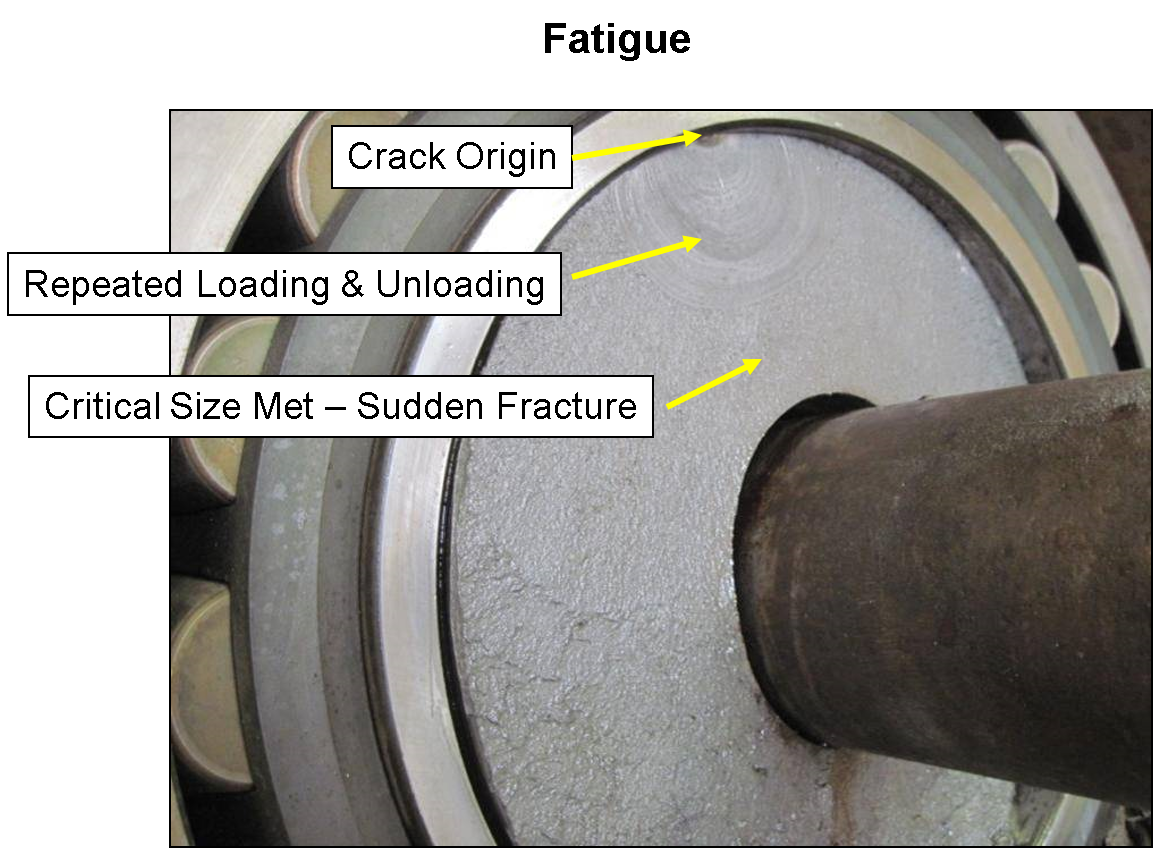
Figure 1- Classic Fatigue Pattern
Repeated cyclical loading will surface in a variety of forms. Here are a few such applications in Figure 2:
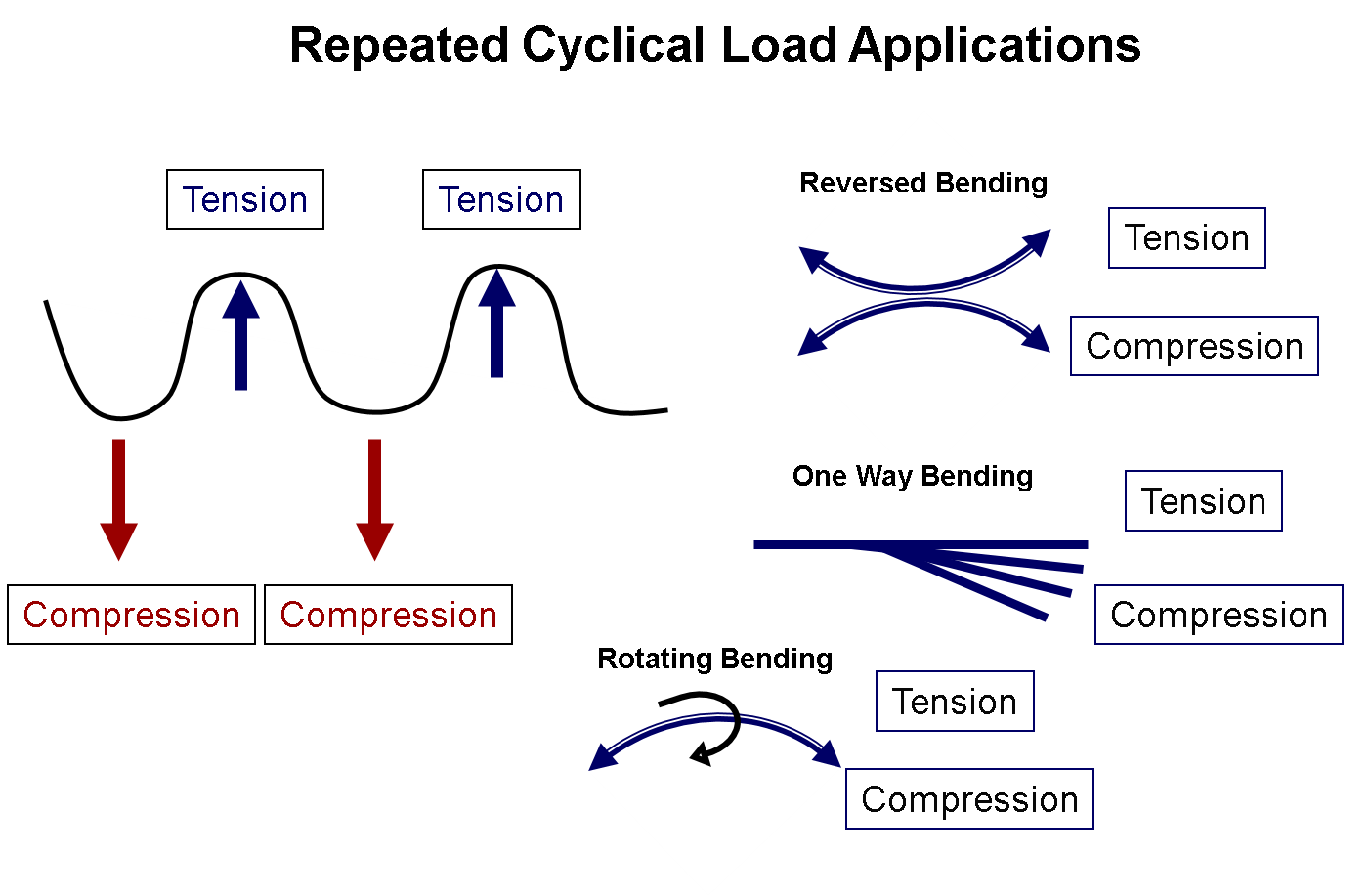
Figure 2 – Cyclical Loading Applications Resulting in Fatigue
Characteristics of Fatigue
Fatigue failures will contain one or more of the following characteristics:
- Always have an origin(s)
- Progression marks may be visually present (depends on load variations)
- Will have a Final Fracture Zone or FFZ (the larger the FFZ the higher the load)
- Ratchet marks may be present (representing high stress concentrations [SC])
- Spalls (Hertzian Fatigue) may be present (mainly in bearings)
Characteristics of Fatigue
Now let’s look at some examples from various environments:
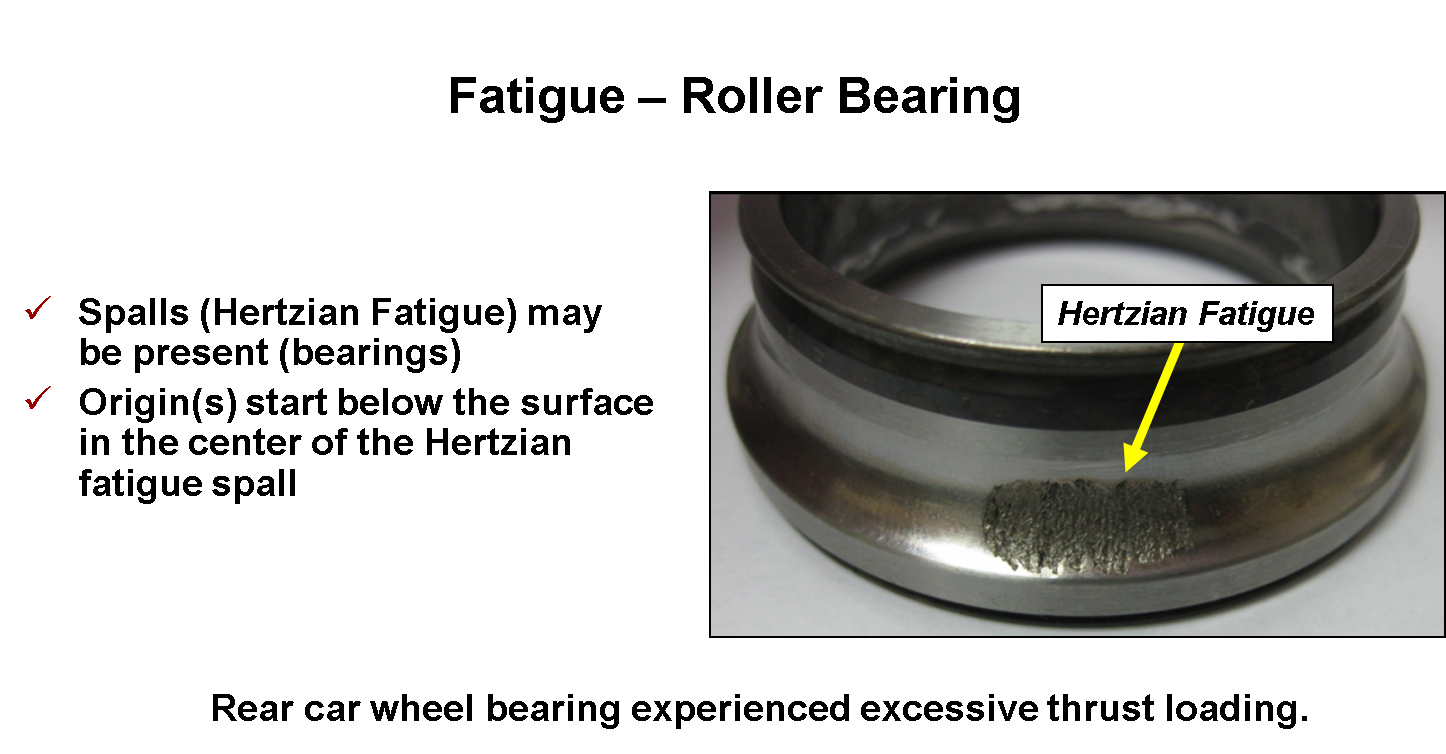
Figure 3 – Hertzian Fatigue on a Roller Bearing
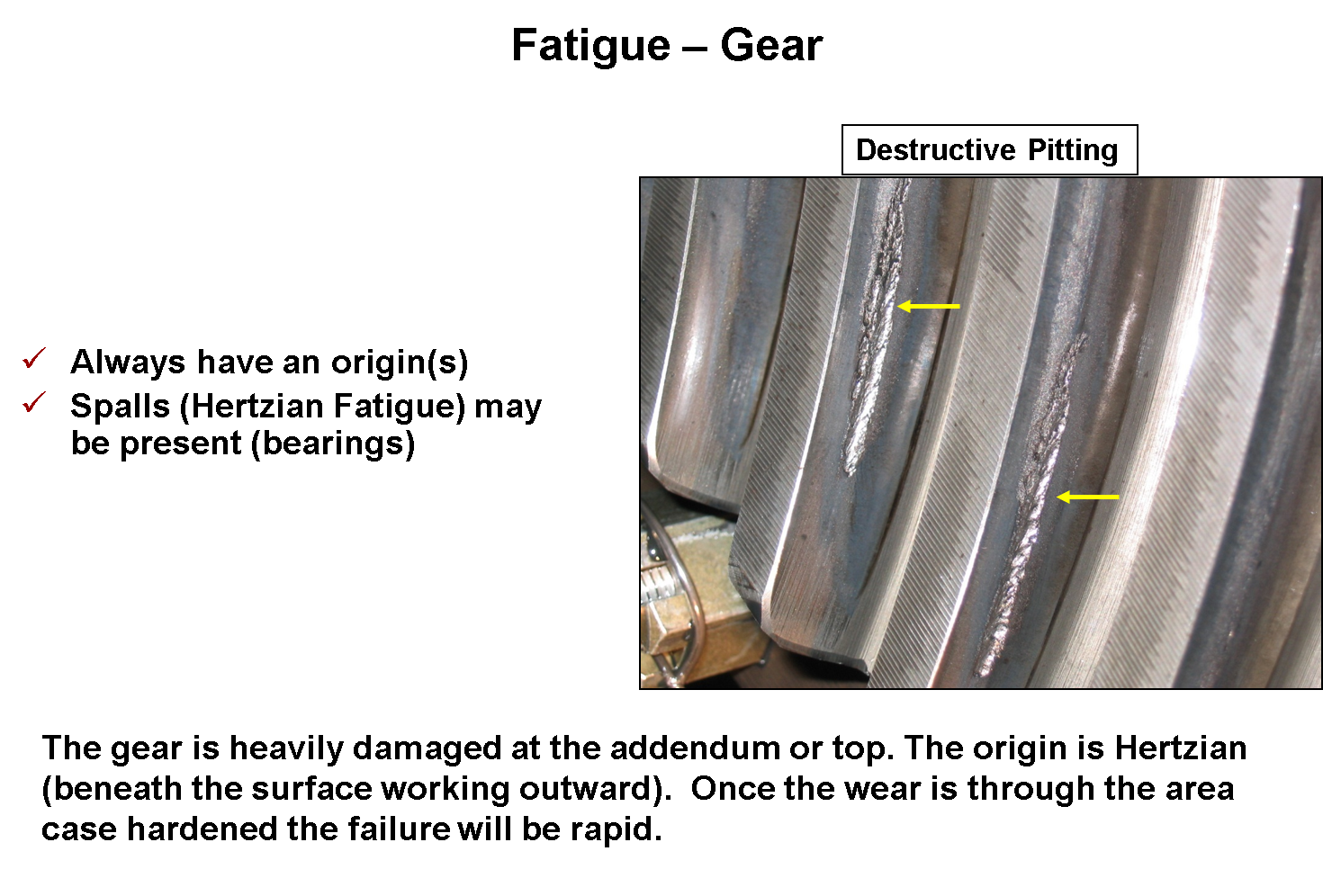
Figure 4 – Spalling on Gear Teeth
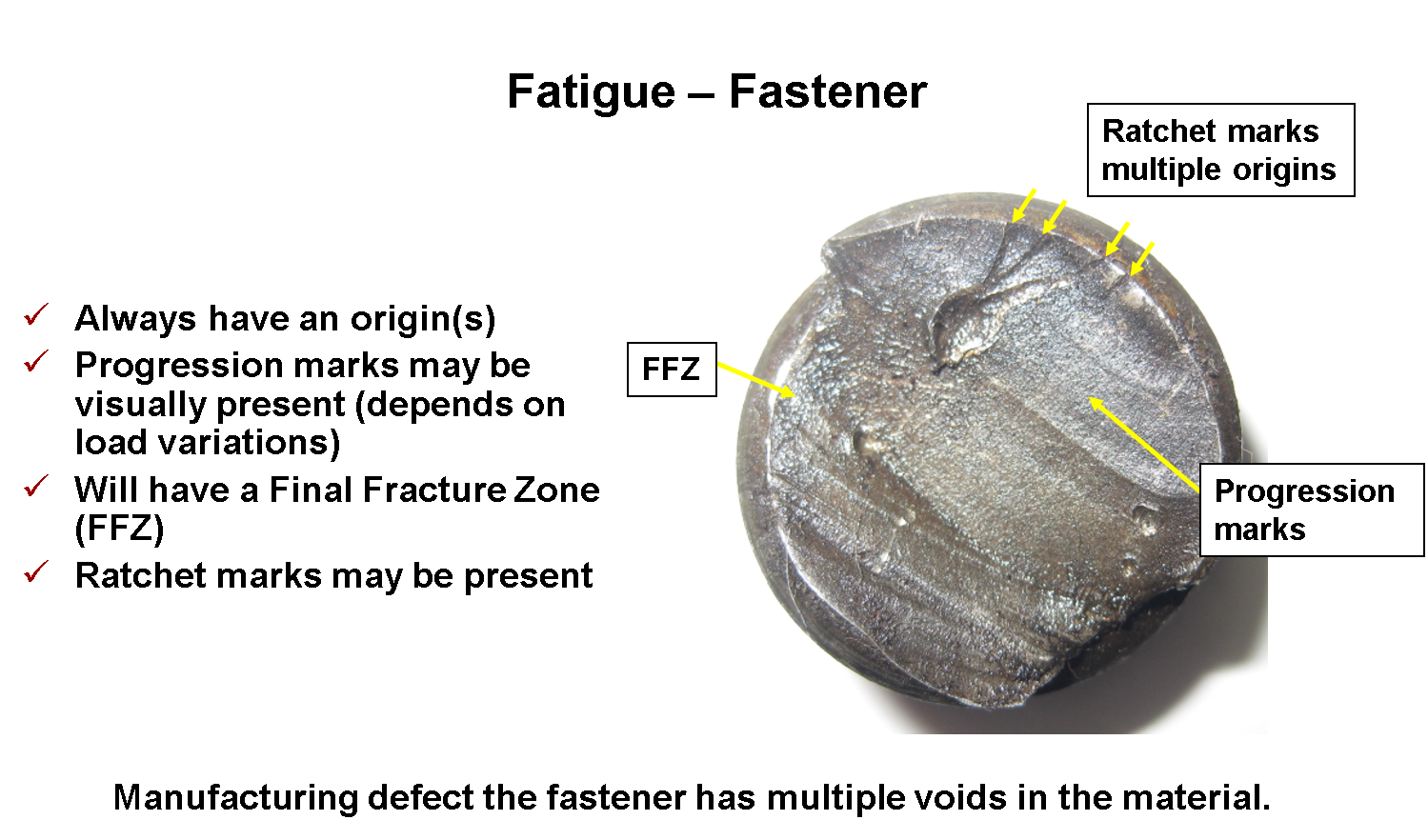
Figure 5 – Fastener Fatigue Example
Let’s take a quick look at where stress concentrations are most prominent on various components.
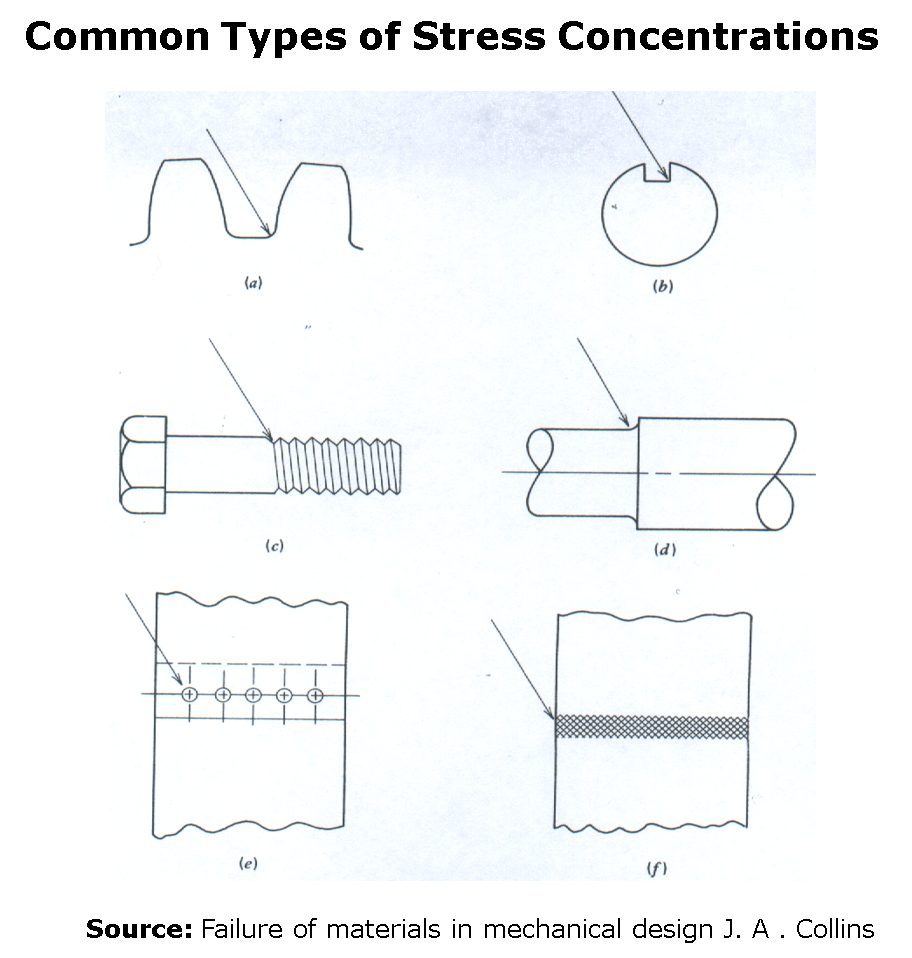
Figure 6 – Stress Concentrations (SC) Types

Figure 7 – Common Means of Reducing Stress Concentrations (via proper welding techniques)
While we showed this fracture surface before, in NAME THAT FAILURE (3), it again becomes relevant here.
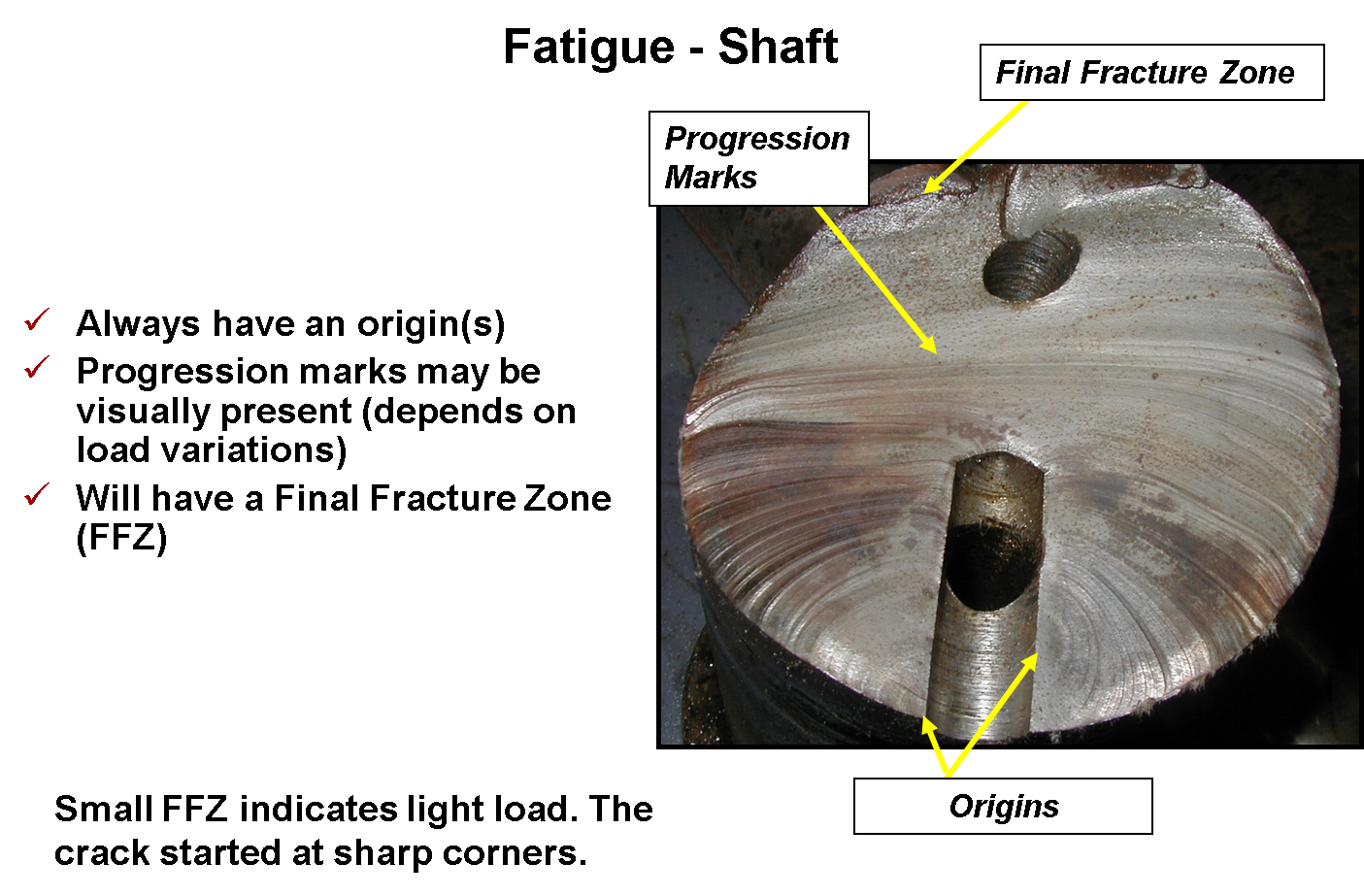
Figure 8 – Classic Fatigue Fracture Pattern on Shaft
This will wrap up our Fatigue 101 discussion and I will leave you with a teaser for Part III-Overload, what type of overload pattern do you think this is?
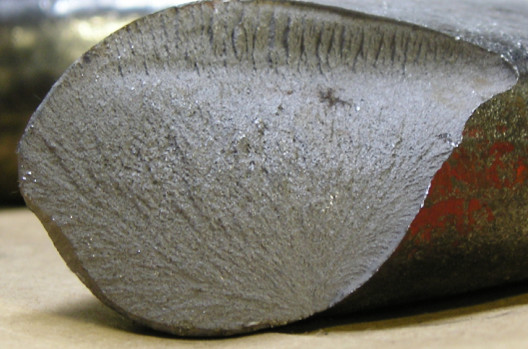
As always, if you interested in learning more about these basics please visit www.reliability.com, or simply click on the graphic below for workshops that specialize in preserving and analyzing such evidence.
Please click the hyperlink if you’re interested in more job aides likes this and/or information on associated training and tools to help with understanding Why Parts Fail.
About the Author
Robert (Bob) J. Latino is former CEO of Reliability Center, Inc. a company that helps teams and companies do RCAs with excellence. Bob has been facilitating RCA and FMEA analyses with his clientele around the world for over 35 years and has taught over 10,000 students in the PROACT® methodology.
Bob is co-author of numerous articles and has led seminars and workshops on FMEA, Opportunity Analysis and RCA, as well as co-designer of the award winning PROACT® Investigation Management Software solution. He has authored or co-authored six (6) books related to RCA and Reliability in both manufacturing and in healthcare and is a frequent speaker on the topic at domestic and international trade conferences.
Bob has applied the PROACT® methodology to a diverse set of problems and industries, including a published paper in the field of Counter Terrorism entitled, “The Application of PROACT® RCA to Terrorism/Counter Terrorism Related Events.”
Recent Posts
AI and Site Reliability Engineers: Lessons from the Field.
Smarter, Faster, Deeper: How AI Is Transforming Root Cause Analysis in Software and Beyond
North America’s Looming Power Shortfall: A Root Cause Analysis for the Grid—and Beyond
Preventing EV Charger Downtime: How Smart Test Strategies Act as Root Cause Analysis in Action
Root Cause Analysis Software
Our RCA software mobilizes your team to complete standardized RCA’s while giving you the enterprise-wide data you need to increase asset performance and keep your team safe.
Root Cause Analysis Training