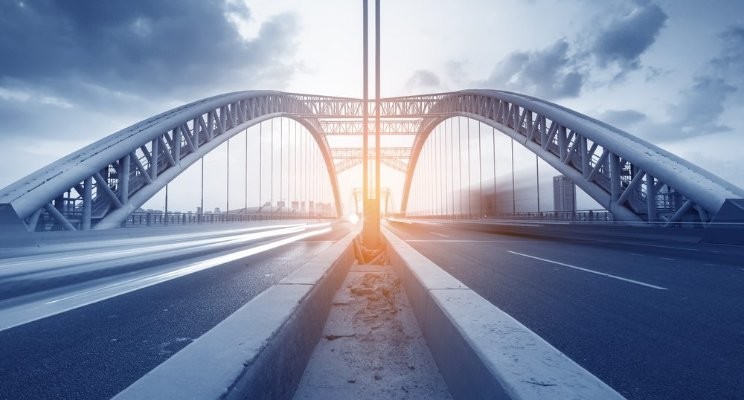
Electronic Field Data Collection: The Bridge to the Connected Plant
The Industrial Internet of Things (IIoT) has created immense excitement and promise for industrial facilities. Having connected assets that continuously monitor their own health and feed that information back in a way that is timely and actionable will drive business outcomes and help organizations achieve loftier goals. The challenge today is that many of our assets are not yet “connected” or “intelligent,” meaning that they are not yet outfitted with the health monitoring instrumentation that provides the live, automated data feed directly to a centralized repository of data.
Yes, critical assets like turbine generators, boiler feed water pumps, highly critical motors and the like are indeed outfitted with modern instrumentation and fail-safe solutions. However, in most industrial facilities throughout the world, this is a very small population of assets.
A typical industrial facility has thousands of electric motors, gearboxes, pumps, and fans, among others, that have ZERO diagnostic instrumentation. While individually these assets may not be as important as some of the more critical assets mentioned above, collectively they are much more important to the productivity of the site. This leaves us with two choices: either outfit these assets with the required diagnostic instrumentation at incredible expense or – more realistically – collect this important data in another way.
The latter is the method that most industrial facilities are employing today.
This is where electronic field data collection comes in. Today, we depend on the eyes and ears of operators, maintenance journeymen and engineers to identify equipment issues and to report those in a way that is timely and actionable. In many cases, this is done with defined rounds or inspection routes that are performed using paper checklists or forms. While this is better than not having any information, it does not always deliver the required results. Paper forms are often lost or discarded, they require someone to review the information in its entirety to determine the next action and they require manual entry of those actions into the enterprise asset management (EAM)/ computerized maintenance management system (CMMS) or other plant execution systems. How often has an operator said, “I told my supervisor and he never did anything about it.”
Electronic field data collection can be the bridge to collecting critical asset health data until the economics of outfitting ALL of our assets with diagnostic technologies becomes a reality. The technology to digitize our existing paper-based routes and checklists is readily available today. In the past, we were limited by sizable and difficult-to-use devices that provided very limited connectivity and lacked the usability needed for everyday use. That has all changed with the advent of mobile computing. Now we have the power of a “real” computer (e.g. tablet or iPad) that can connect wirelessly to our networks to transmit asset health information in the same way that a connected device can. The additional benefits are having both the ability to collect both quantitative data like temperature readings and qualitative information, such as the insight of trained human beings who can provide accurate context to the information that is being generated.
The technology for performing electronic rounds are abundant. Aside from technology though, we must also look at the cultural aspects of this type of effort. As Peter Drucker once said, “Culture eats strategy for breakfast.” To ensure success, this type of effort must be viewed as a replacement for inefficient work, including paper based routes, with more effective methods. If this is viewed as piling on more work, rather than making work easier, it will be fought with resistance. Before deploying any technology, ensure that you have a defined work process for how the data will be collected and how the data will be used. If workers see that they are out collecting data and it is not reviewed or acted upon, the effort will generate no positive outcomes. However, if employees see that their findings are addressed and viewed as valuable, they will continue to support the effort.
8 Essential Features of Electronic Field Data Technology
- Integrates with current maintenance and asset management systems
- Creates templates for data entry
- Integrates with existing asset strategy efforts
- Allows for both numeric and character based responses
- Has the ability to drive field data collection in both online and offline modes
- Can create recommendations in the field on mobile devices
- Should be device-agnostic and capable of working on tablets, phones and a variety of operating systems
- Data should integrate seamlessly with existing IIoT technologies
Conclusion
The vision of a totally digital plant is rapidly becoming a reality. Devices are more economical and practical to deploy. However, we still cannot overlook the fact that many of our plants are older and will not have this connected technology in the near-term. This is where a mobile electronic field data collection effort can provide the bridge to the digital industrial facility, capturing the benefits of digital asset health today while the economics and practicality of a fully connected facility catches up.
Originally Published on Inspectioneer.com
About the Author
Ken Latino is the Managing Director of Prelical Solutions, a Practical Reliability Group offering Maintenance and Reliability consulting services in both continuous process and batch manufacturing plants.
Ken’s services help large asset intensive companies to get increased production rates and reduced maintenance costs while improving safety and environmental performance.
He has extensive Maintenance and Reliability experience in both continuous process and batch manufacturing plants, and has helped large asset-intensive companies to increase production rates and reduce maintenance costs while improving safety and environmental performance.
Recent Posts
AI and Site Reliability Engineers: Lessons from the Field.
Smarter, Faster, Deeper: How AI Is Transforming Root Cause Analysis in Software and Beyond
North America’s Looming Power Shortfall: A Root Cause Analysis for the Grid—and Beyond
Preventing EV Charger Downtime: How Smart Test Strategies Act as Root Cause Analysis in Action
Root Cause Analysis Software
Our RCA software mobilizes your team to complete standardized RCA’s while giving you the enterprise-wide data you need to increase asset performance and keep your team safe.
Root Cause Analysis Training