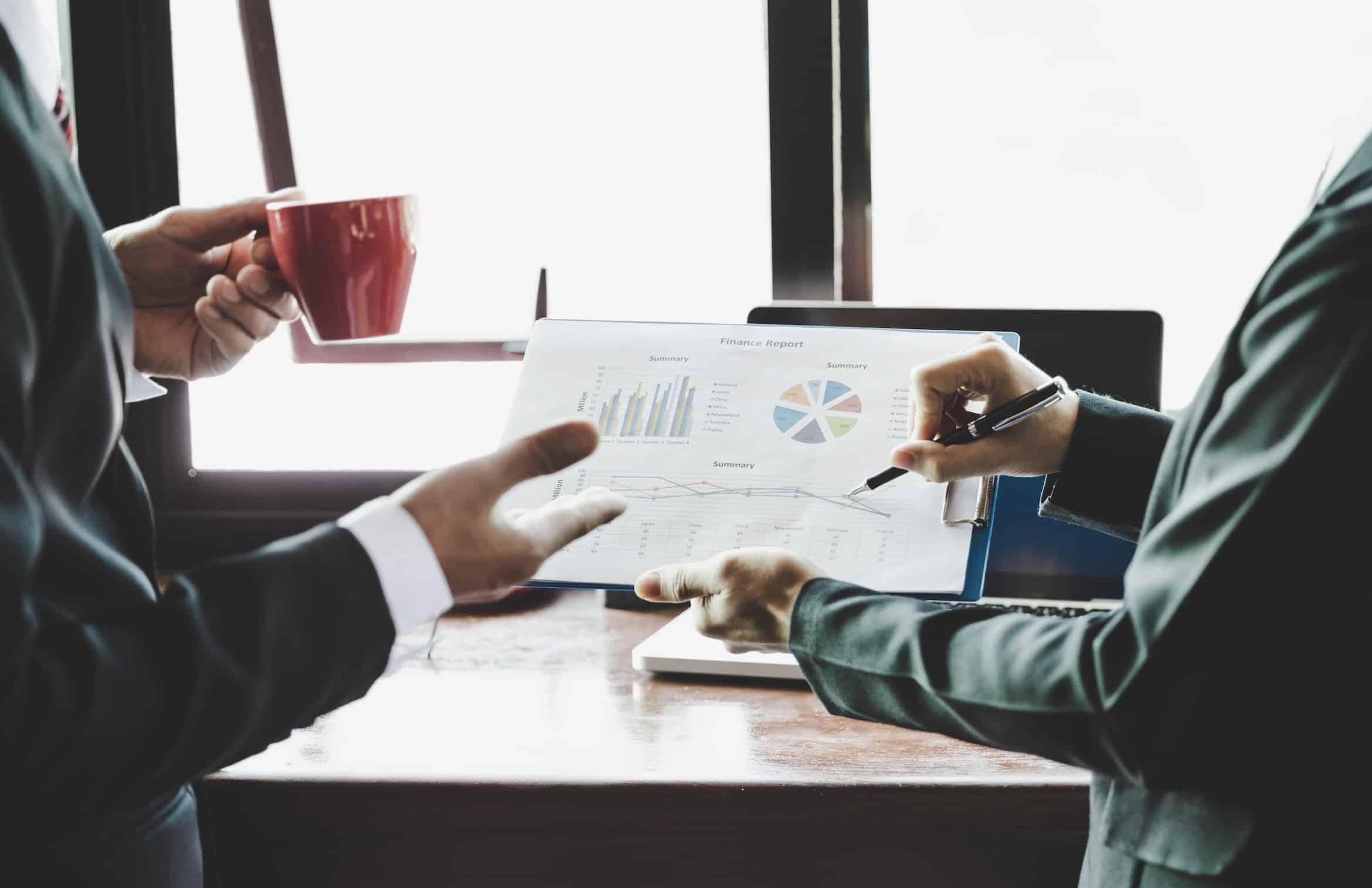
Do We Get Our Money’s Worth Out of Training?
A turbine in a refinery fails catastrophically. The adrenaline is flowing as efforts to recover and get back on-line are taking place. Even though turmoil appears rampant there is an air of organization. The magnitude of the failure prompts a Root Cause Failure Analysis (RCFA), primarily because the loss is high and the insurance companies and the lawyers are involved. Everyone wants a name, a culprit! They want someone to blame for the incident, so that it will appear as though the failure has been solved. The failure analysis concludes that John Doe closed a valve that subsequently wrecked the turbine. John is severely disciplined and is lucky to still be employed.
The Importance of Root Cause Failure Analysis (RCFA)
Though the above scenario is fictional, it could very well be reality. We can all think of instances that parallel this scenario. Now John is alienated, because he feels he is the “fall guy” for the failure. Management, the lawyers, and the insurance company are satisfied because they believe the root cause of the failure has been determined. But has it?
When performing RCFA it is important to determine why people do what they do. After all, neither John nor any other employee willingly chooses to cause a failure by being unreliable. We need to go beyond just the person, and explore what about the way in which we operate allows situations like the one outlined above to occur.
Enhancing Training Investment for Operational Improvement
Often, the results of a thorough RCFA demonstrate that the root cause of a failure is that individuals do not possess the skill and/or knowledge to perform their jobs safely or properly. How can this be when industry annually spends billions of dollars on training?
One explanation lays with why we invest in training. Too often, employees are trained to meet governmental regulations or just for the sake of saying “our employees are trained.” To optimize our training investment, the central purpose for training should be to improve operations.
Another reason for training’s poor return-on-investment is management’s lack of commitment to periodically evaluate and review people, procedures, and training to ensure that they are meeting the needs of the organization. When deficiencies are determined, management must develop strategies that will overcome the void.
When you are considering Root Cause Analysis training, we recommend the following 5-step process for training:
- Have a reason to train. Determine what change in behavior will result from the training.
- Train in knowledge.
- Train in the skill through careful development and execution of exercises to assure proficiency.
- Provide the trainees with the opportunity to practice the new knowledge and skill in the field.
- Lastly, and most importantly, determine if the desired behavior change in Step 1 was accomplished.
Properly trained employees will increase Plant Reliability. Improperly trained employees, or employees trained for the wrong reasons, should be considered a lost profit opportunity. We must begin to audit our training efforts and determine if we are indeed getting our money’s worth out of our training investments.
About the Author
Robert (Bob) J. Latino is former CEO of Reliability Center, Inc. a company that helps teams and companies do RCAs with excellence. Bob has been facilitating RCA and FMEA analyses with his clientele around the world for over 35 years and has taught over 10,000 students in the PROACT® methodology.
Bob is co-author of numerous articles and has led seminars and workshops on FMEA, Opportunity Analysis and RCA, as well as co-designer of the award winning PROACT® Investigation Management Software solution. He has authored or co-authored six (6) books related to RCA and Reliability in both manufacturing and in healthcare and is a frequent speaker on the topic at domestic and international trade conferences.
Bob has applied the PROACT® methodology to a diverse set of problems and industries, including a published paper in the field of Counter Terrorism entitled, “The Application of PROACT® RCA to Terrorism/Counter Terrorism Related Events.”
Recent Posts
AI and Site Reliability Engineers: Lessons from the Field.
Smarter, Faster, Deeper: How AI Is Transforming Root Cause Analysis in Software and Beyond
North America’s Looming Power Shortfall: A Root Cause Analysis for the Grid—and Beyond
Preventing EV Charger Downtime: How Smart Test Strategies Act as Root Cause Analysis in Action
Tags
reliability inititatives
reliability training
root cause analysis training
root cause failure analysis
Root Cause Analysis Software
Our RCA software mobilizes your team to complete standardized RCA’s while giving you the enterprise-wide data you need to increase asset performance and keep your team safe.
Root Cause Analysis Training