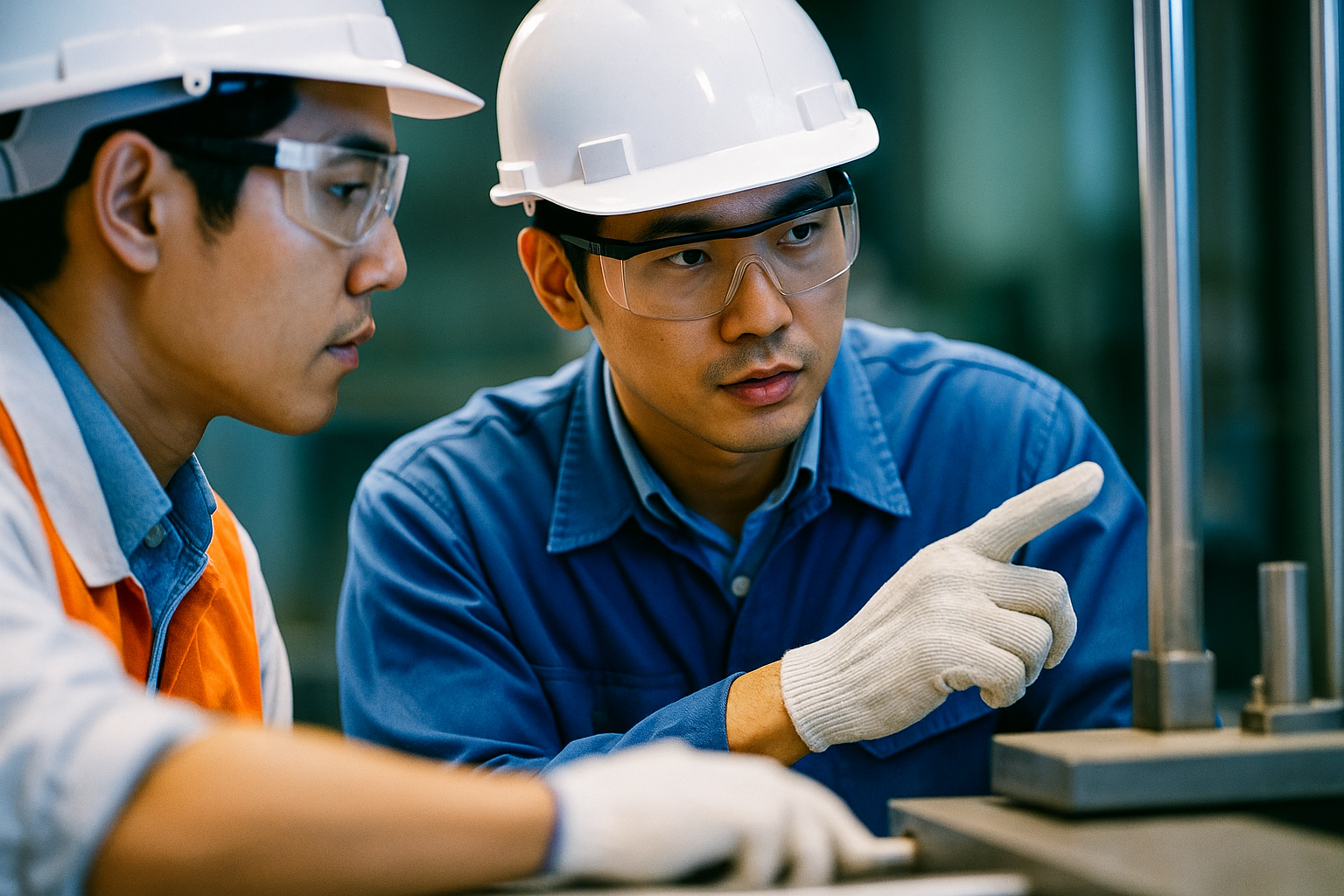
A Step-by-Step Guide to Using Root Cause Analysis Tools for Improved Reliability
Reliability has become a cornerstone of operational excellence in today’s fiercely competitive industrial landscape. Unexpected failures can lead to significant downtime, increased costs, and potential safety hazards. To effectively address these recurring challenges, organizations turn to Root Cause Analysis (RCA) tools, which help uncover the underlying causes of problems and prevent their recurrence. This comprehensive guide will take you step-by-step through the process of utilizing RCA tools, empowering you to enhance reliability and secure long-term success for your operations.
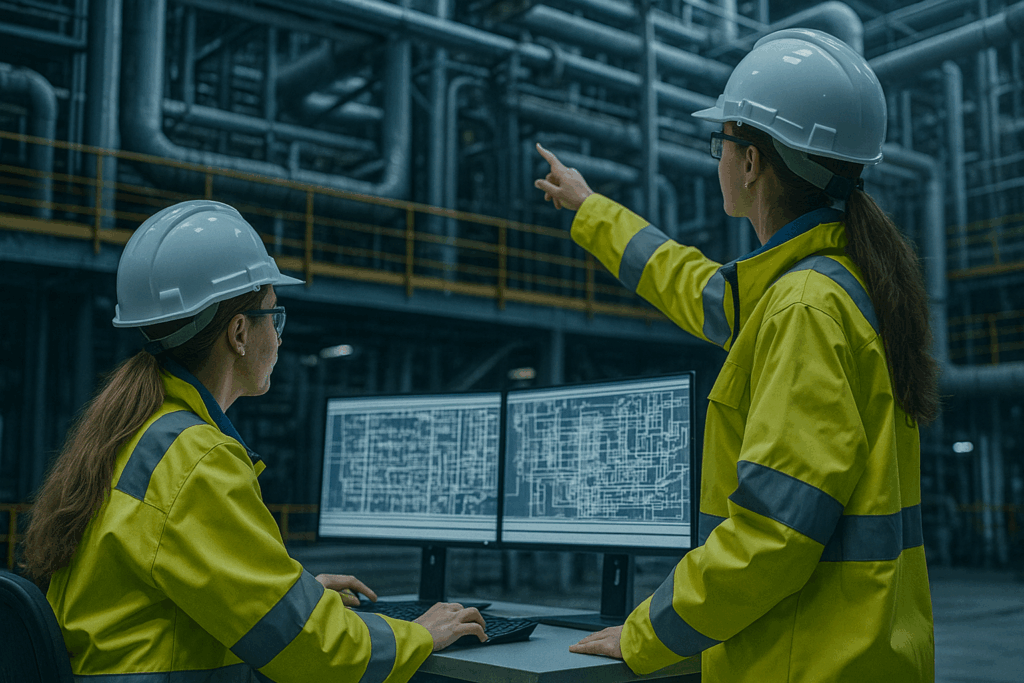
Why Use RCA Tools for Reliability?
RCA tools provide a structured way to investigate failures within your system and help you address the root cause of a problem and eliminate it instead of applying temporary fixes.
By implementing RCA tools, companies can:
- Reduce equipment downtime
- Save costs by avoiding recurring issues
- Improve safety standards
- Boost overall reliability and performance
Step 1: Define the Problem Clearly
The first step in using any RCA tool is to clearly define the problem you’re dealing with. A well-defined problem sets the direction for the entire investigation. Start with basic facts about the issue, including what happened, when it happened, and a detailed accounting of its impact on your operations.
- Tip: Use tools like checklists or predefined templates to gather all relevant information and structure your investigation from the start.
Step 2: Collect Data and Analyze Trends
Once the problem is defined, the next step is to collect relevant data that will help in identifying the root cause. This includes historical maintenance records, logs, and operating conditions at the time of the failure. Your RCA tool will allow you to analyze this data to find patterns and trends.
- Tip: Look for RCA tools that offer built-in data collection features and visualization options, making it easier to spot the relationships between different causes and effects.
Step 3: Use a Root Cause Analysis Tool to Identify Potential Causes
At this stage, your team should work collaboratively using your RCA tool to explore all possible causes of the problem. Techniques like the 5 Whys can help by encouraging you to ask “why” multiple times until the true cause is uncovered.
Most RCA tools come equipped with a range of investigation techniques, including:
- Fishbone Diagrams: Great for mapping out all possible causes visually.
- 5 Whys Analysis: Helps you dig deeper into the problem by repeatedly asking “Why?”
- Change Analysis: Used to assess what changed in the system before the issue occurred.
- Tip: Encourage your team to think broadly, considering all aspects of the system to avoid missing hidden causes.
Step 4: Analyze and Verify the Root Cause
Once you’ve identified potential causes, the next step is to validate them through analysis and testing. Your RCA tool should help you narrow down the list to the most likely root cause(s). In some cases, further testing or simulation may be required to confirm the findings.
- Tip: Use tools like Failure Modes and Effects Analysis (FMEA) or Fault Tree Analysis to further assess the risks associated with each cause.
The goal here is to ensure you’re addressing the real problem, not just the symptoms. Make sure your team agrees on the findings and is confident in the root cause before moving forward.
Step 5: Develop and Implement Solutions
With the root cause identified, it’s time to develop corrective actions. This stage involves brainstorming potential solutions, evaluating them based on feasibility, and selecting the one that best addresses the root cause.
An excellent RCA tool should allow you to document these solutions and track their implementation. Whether it involves process changes, equipment upgrades, or additional training, the solution should be implemented as soon as possible to prevent the issue from recurring.
- Tip: Ensure that any changes made are communicated clearly to all relevant teams to avoid confusion or implementation delays.
Step 6: Monitor the Results
After implementing the solution, it’s important to monitor the results over time. Your RCA tool should allow you to track performance metrics and ensure the solution is effectively preventing the problem from recurring. In some cases, new issues may arise, so ongoing monitoring is key to ensuring long-term success.
- Tip: Look for RCA tools that offer built-in monitoring and reporting features, so you can track performance and share the results with stakeholders.
Achieving Reliability Through Root Cause Analysis Tools
RCA tools are an indispensable part of any reliability program. By following the steps outlined above—defining the problem, collecting data, analyzing potential causes, identifying root causes, implementing solutions, and monitoring results—you can achieve more reliable operations, reduce costs, and improve safety.
At Reliability.com, we provide the latest insights and tools to help you improve your RCA processes and enhance your overall reliability strategy. Whether you’re new to Root Cause Analysis or looking to upgrade your existing system, we’re here to guide you every step of the way.
Recent Posts
AI and Site Reliability Engineers: Lessons from the Field.
Smarter, Faster, Deeper: How AI Is Transforming Root Cause Analysis in Software and Beyond
North America’s Looming Power Shortfall: A Root Cause Analysis for the Grid—and Beyond
Preventing EV Charger Downtime: How Smart Test Strategies Act as Root Cause Analysis in Action
Root Cause Analysis Software
Our RCA software mobilizes your team to complete standardized RCA’s while giving you the enterprise-wide data you need to increase asset performance and keep your team safe.
Root Cause Analysis Training