Subscribe for updates
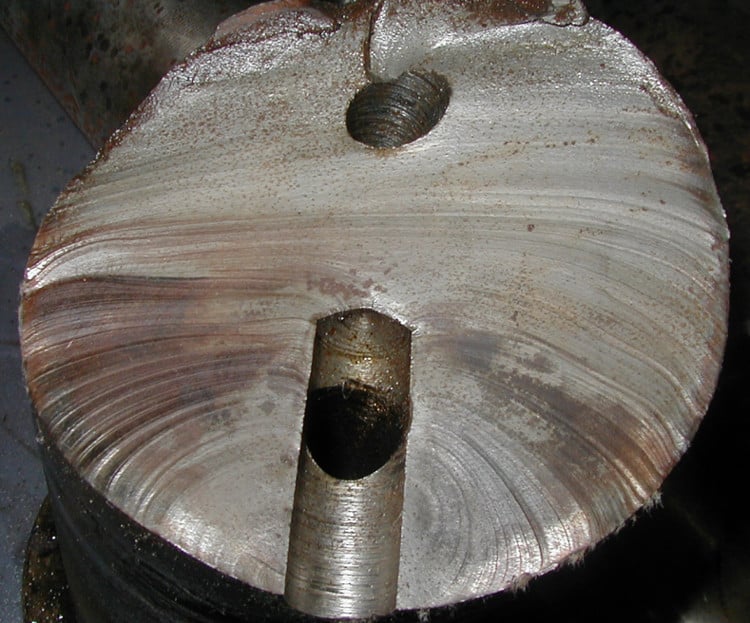
Name That Failure | Part 3
Reading Time: 4 minutes Can you identify and name this fracture pattern? How can you tell it is that fracture pattern? Where are the origin(s) of the failure
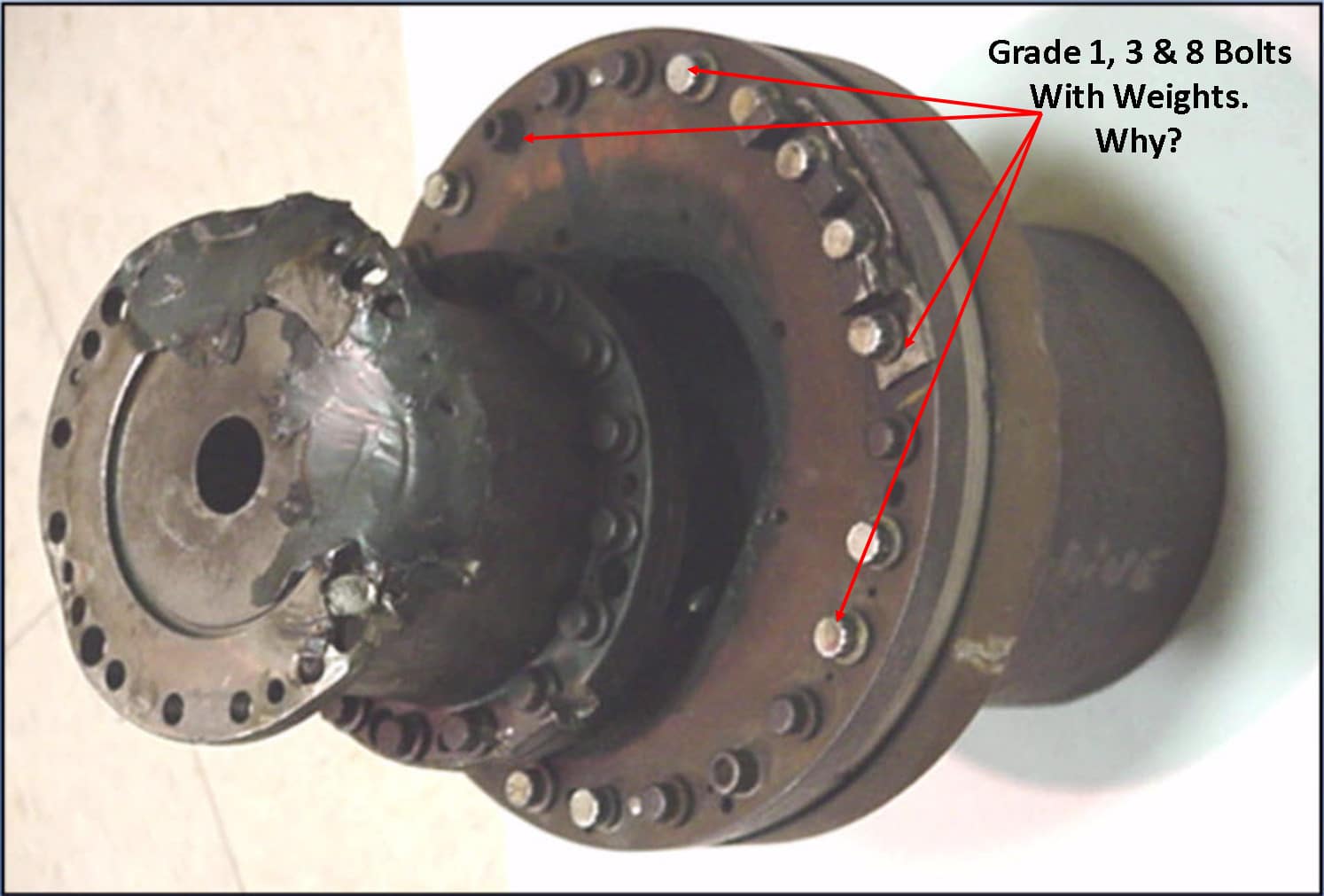
Name That Failure Pattern | 2nd Edition
Reading Time: 3 minutes This failure occurred on a turbine driven boiler feedwater pump (TDBFP) at a fossil fuel power plant. The pump in question is an outboard boiler
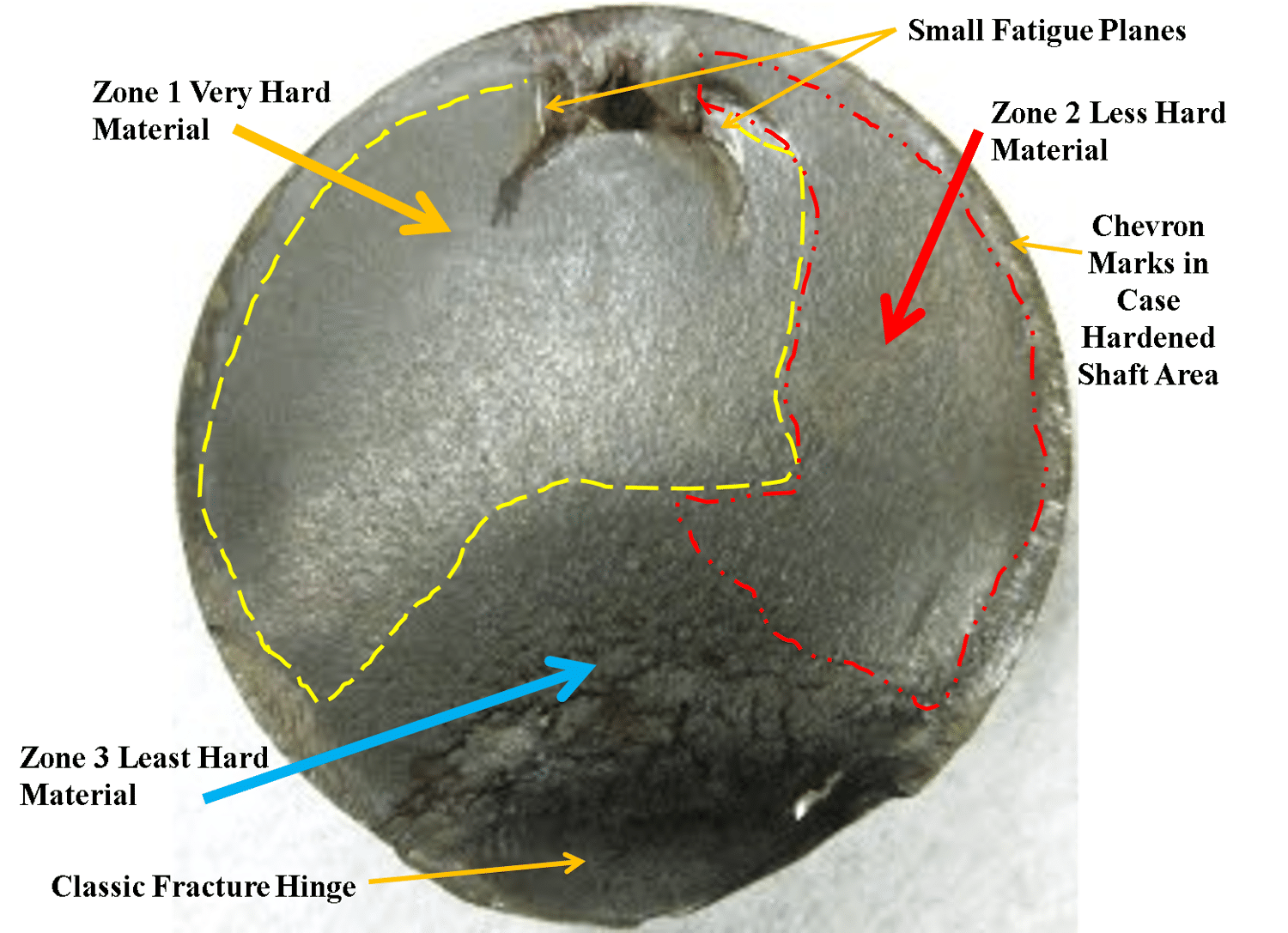
Name That Failure Pattern – Part 1
Reading Time: 8 minutes This is a failed shaft that came out of a pump in a paper mill. The pump was only in service for about a month
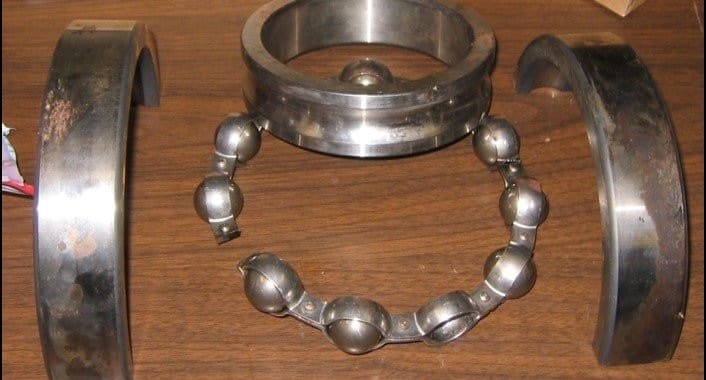
Examining Rolling Element Bearings
Reading Time: 7 minutes In our last series highlighting the 4 primary Failure Modes (FM) of component failures (erosion, corrosion, fatigue and overload), we discussed how to read fractured surfaces.
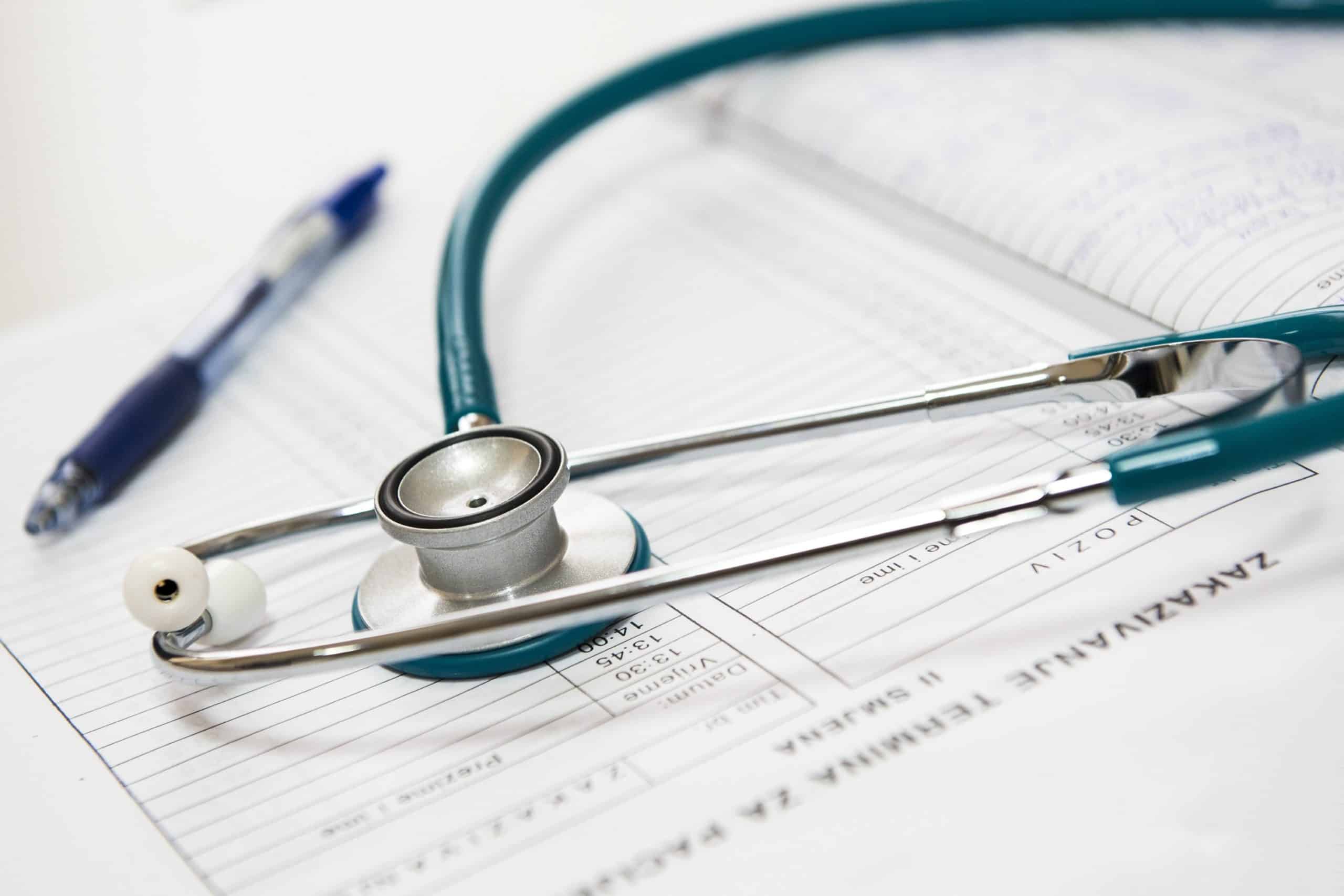
Optimizing RCA and FMEA in Health Care
Reading Time: 12 minutes “Failure Mode and Effect Analysis” (FMEA) and “Root Cause Analysis” (RCA) are becoming commonplace terms in work environments and in the literature. This article will
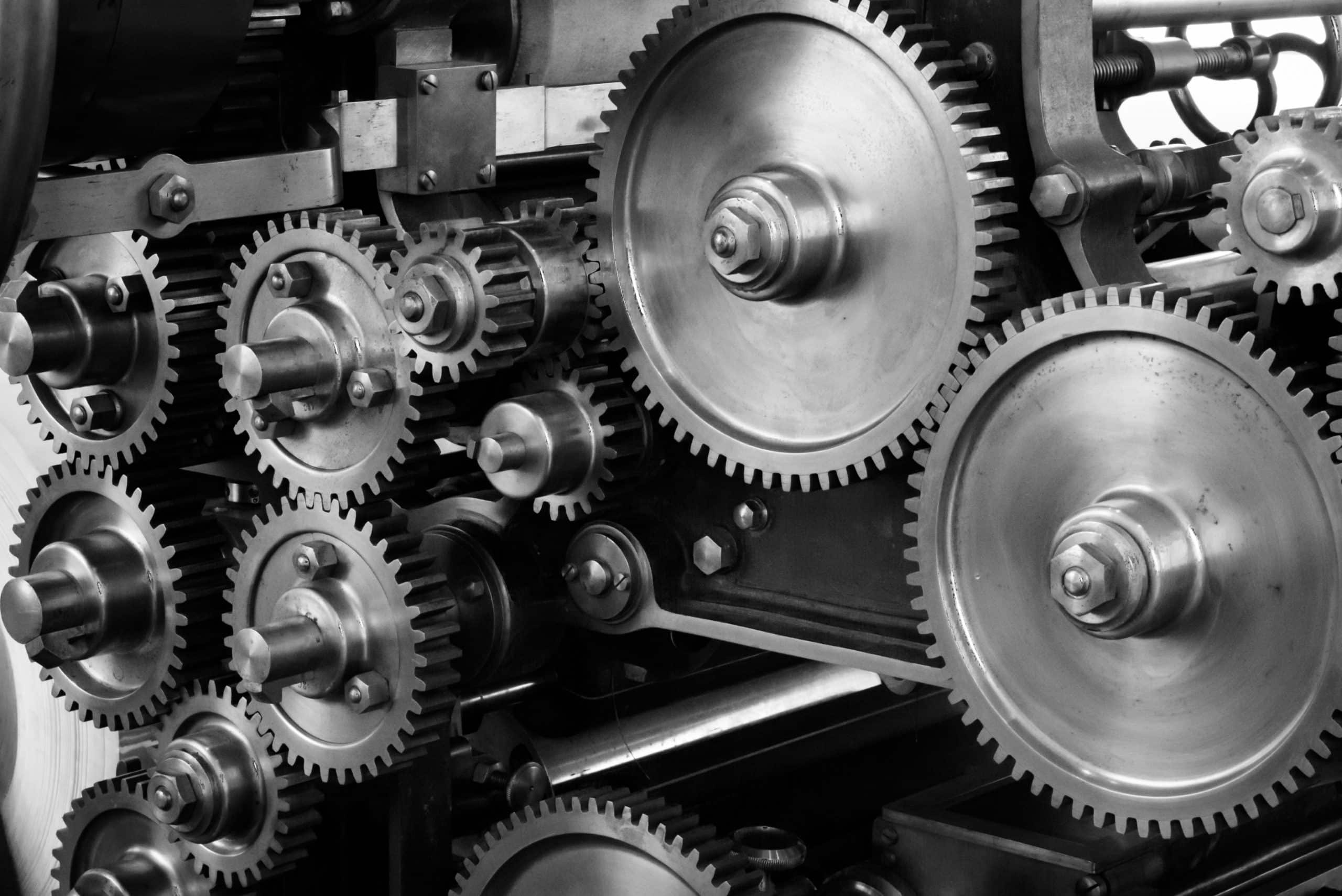
Defining Root Cause Analysis (RCA)
Reading Time: 7 minutes In this blog, I discuss the RCA definition I used as a career analyst/investigator and explain why it makes sense to me. You decide if
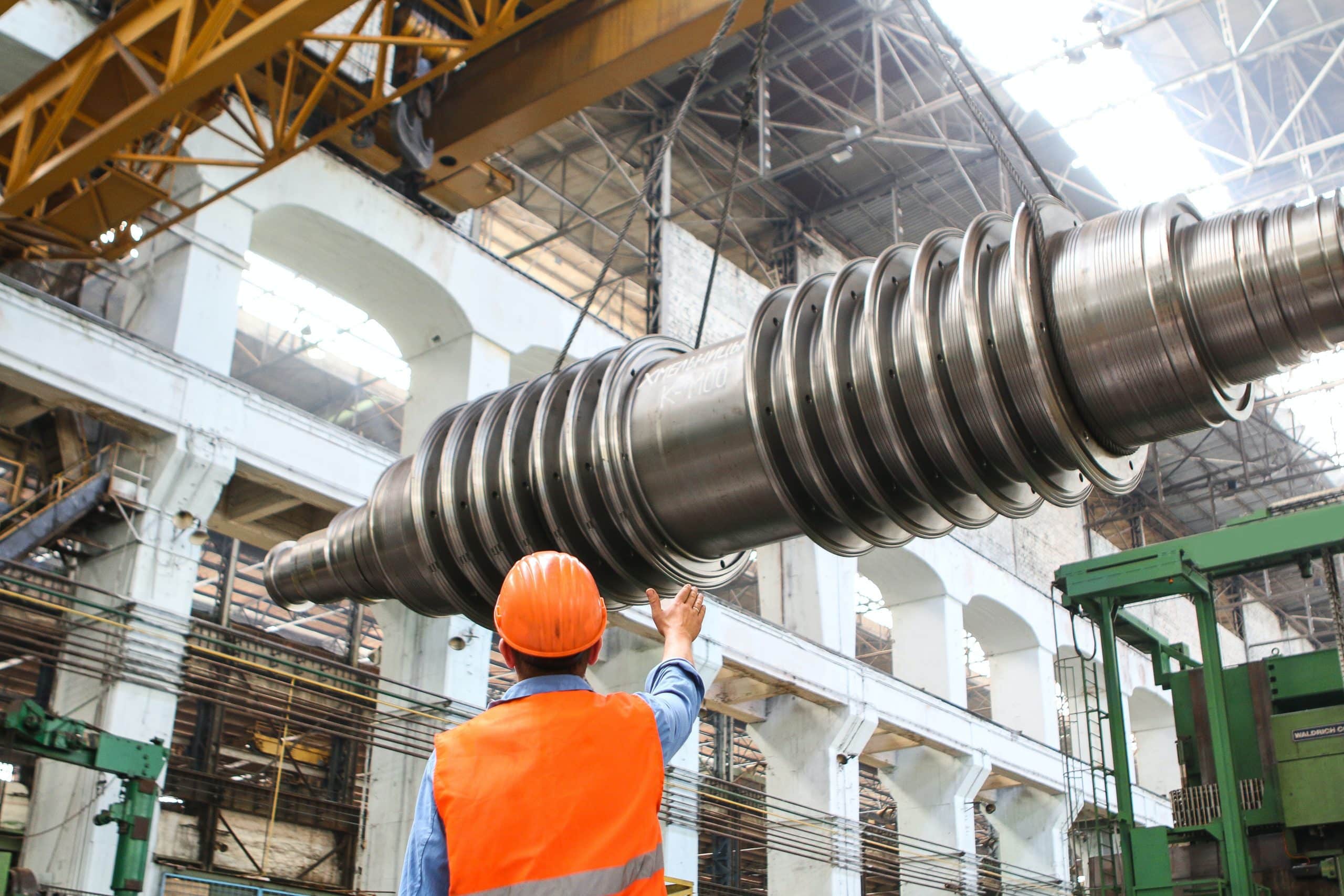
3 Steps to Improve Your Root Cause Analysis
Reading Time: 5 minutes There are various ways for us to improve our root cause analysis and take our reliability to the next level. Reliability professionals could do RCAs
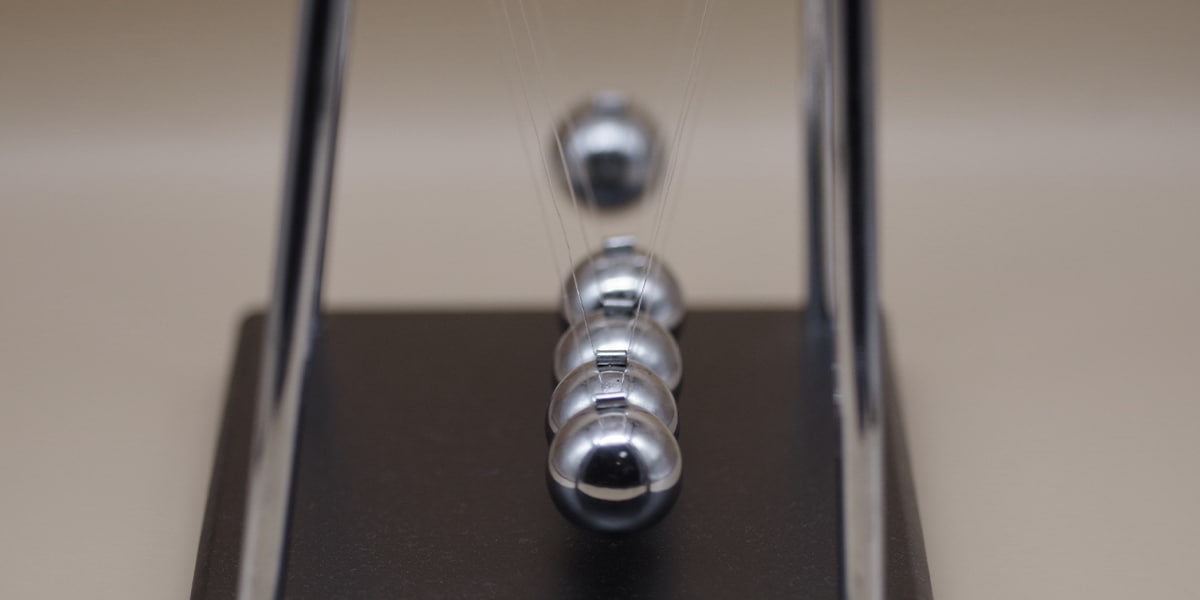
The 5 Reasons Why Most RCA Efforts Fail to Have a Lasting Impact
Reading Time: 5 minutes Most of us have all worked at places with some degree of an ‘RCA’ effort. They likely all defined and practiced ‘RCA’ differently, but nonetheless
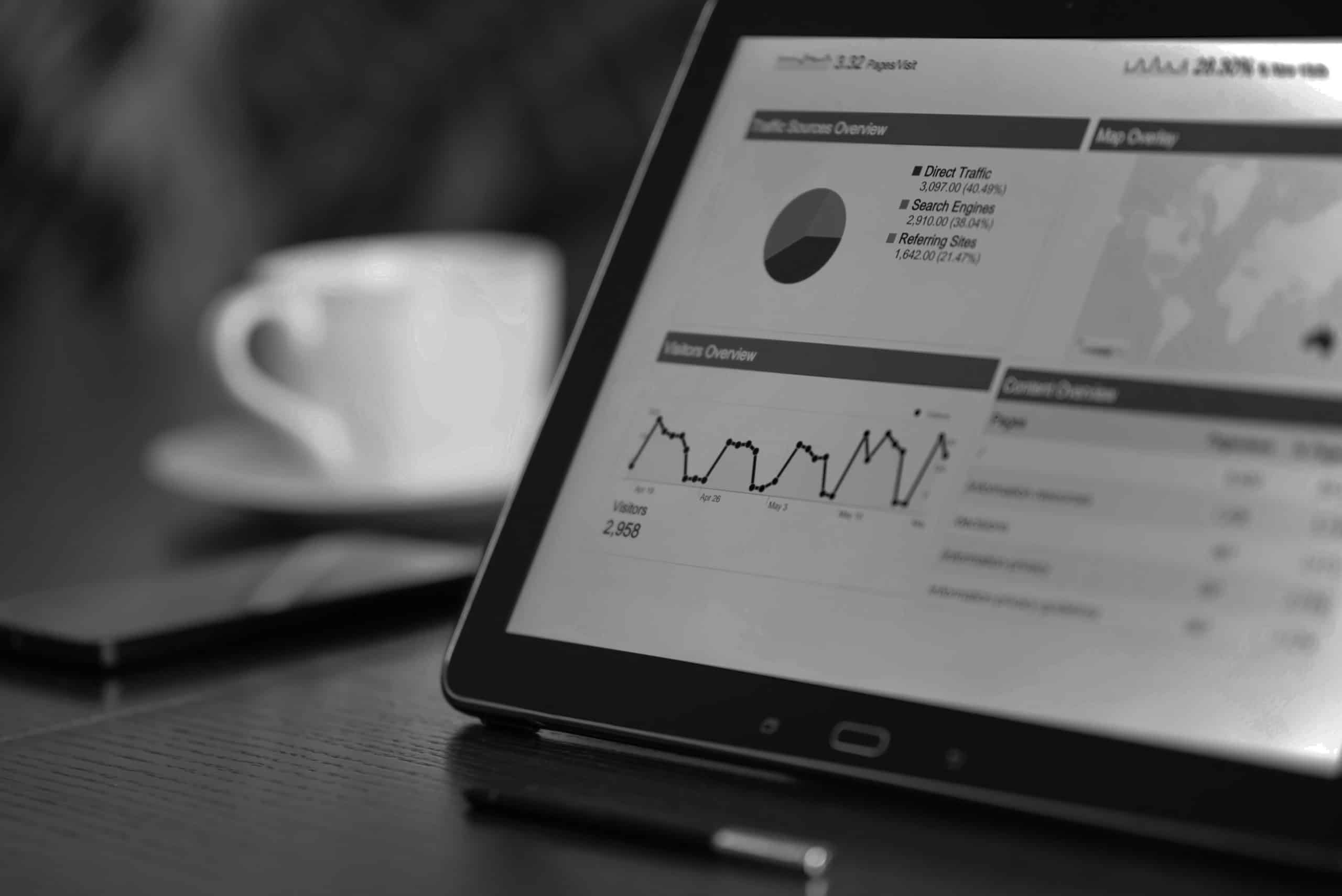
The PROACT® Approach to RCA
Reading Time: 9 minutes Chapter 1: Is All RCA the Same? An RCA myth shared by many managers is that RCA methods are all the same, when in fact
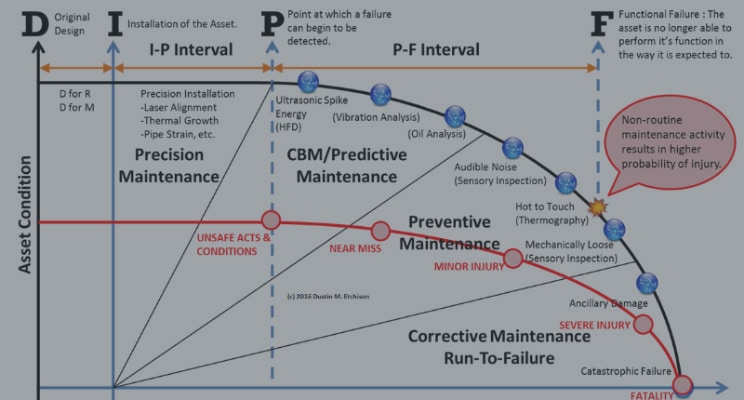
Is There Really a Direct Correlation Between Reliability & Safety?
Reading Time: 6 minutes Safety is often directly correlated with system or component reliability. Is that really the case? Find out what the experts and their data really says.
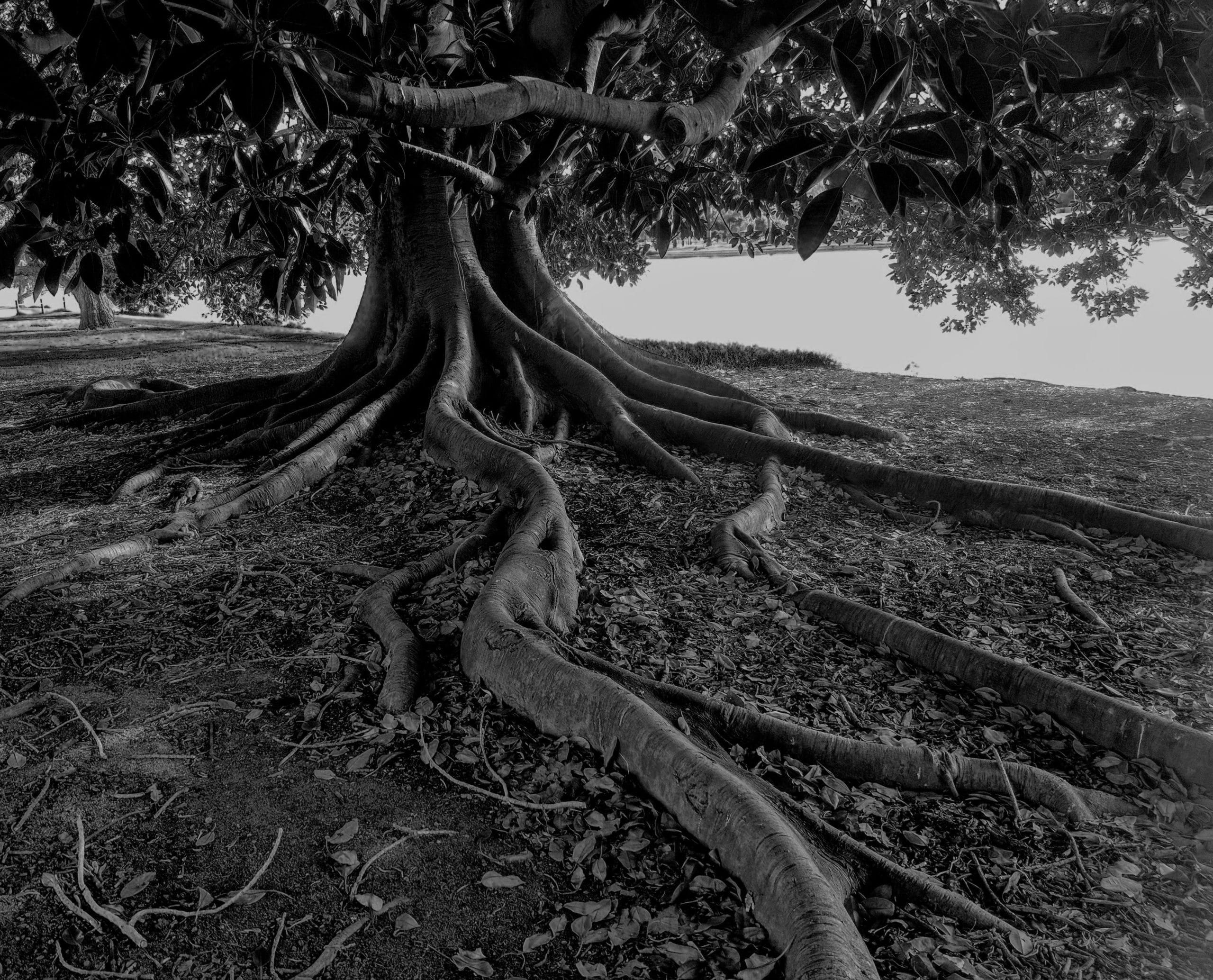
How to Perform Root Cause Analysis (RCA)?
Reading Time: 11 minutes Understanding the reasons behind a company’s struggles isn’t always about not knowing how to fix them. Often, the true origins of these problems are hidden,
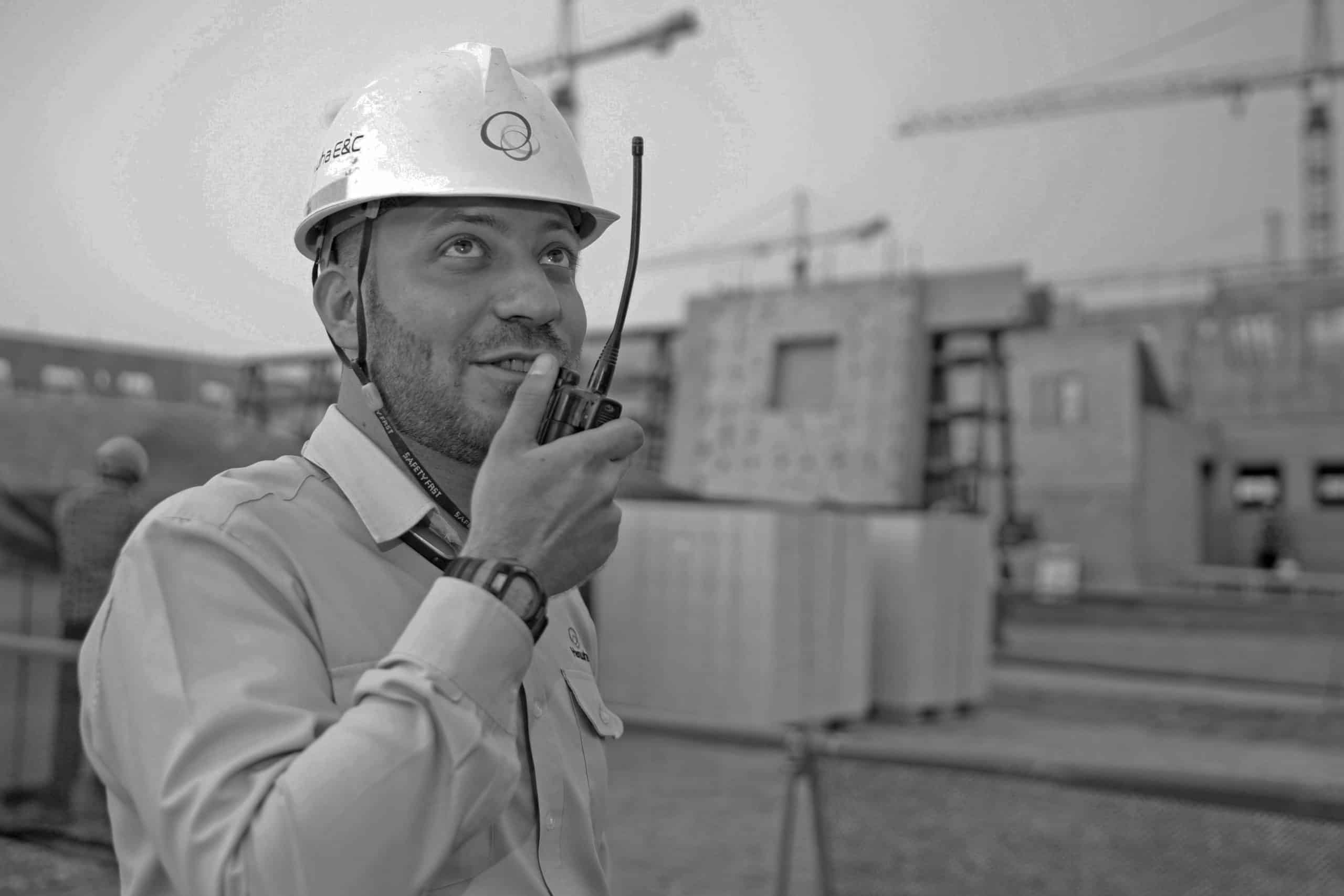
The Secrets of How To Be a Good Reliability Engineer
Reading Time: 8 minutes What does it take to be a good Reliability Engineer? Learn how to better utilize RCA thinking, develop Reliability habits, and how to build a