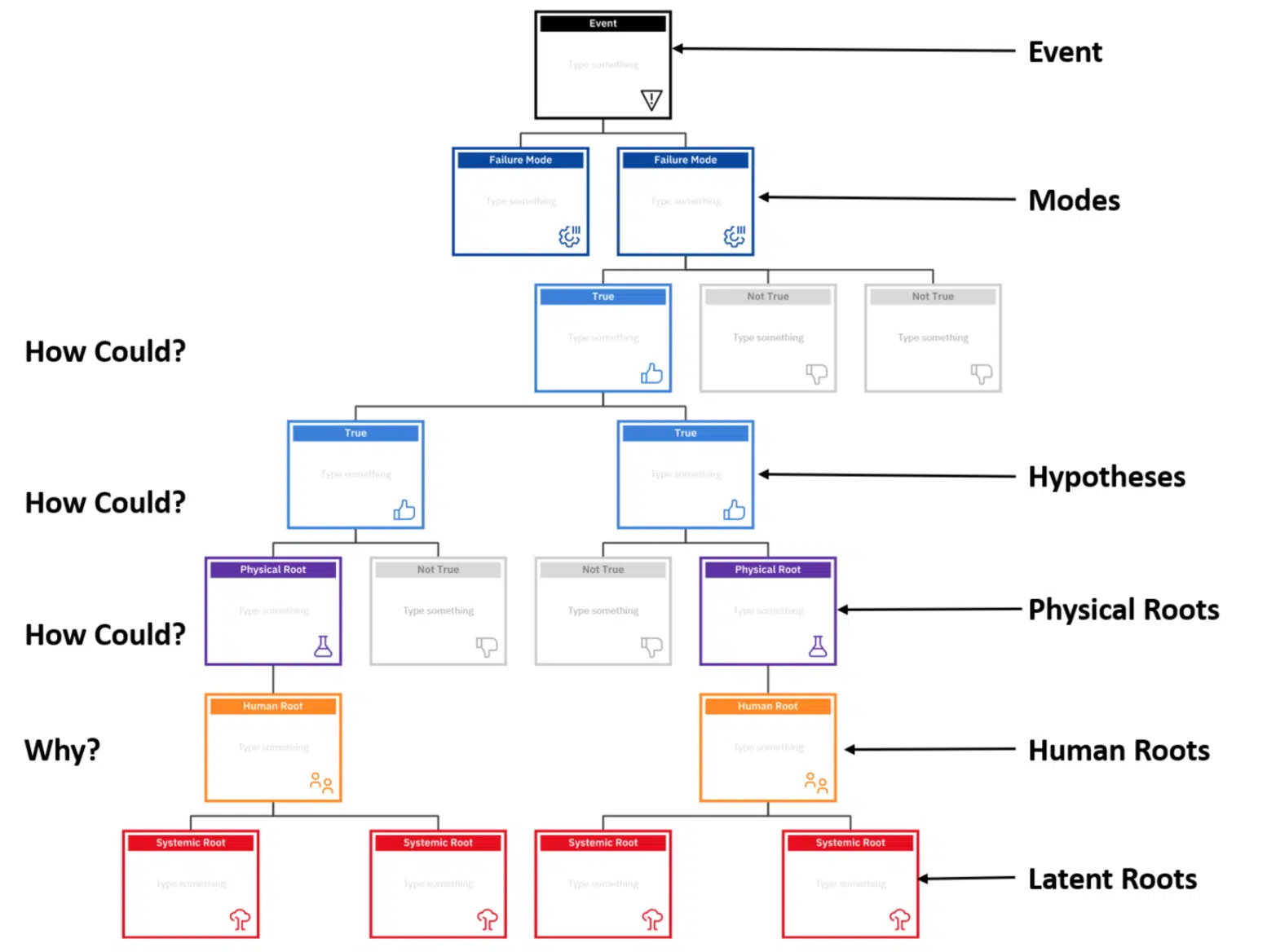
Supercharge Lean Six Sigma with Root Cause Analysis
Has your organization adopted Six Sigma? Lean manufacturing? What about Lean Six Sigma? If you already have any of these business process improvements in place, where will you go next? In this article we will focus on transforming your organization beyond Lean Six Sigma to the next level of performance.
In the future, companies can take another quantum step forward by combining Lean Six Sigma with Advanced Root Cause Analysis (RCA). The value of taking this natural progression on the way to achieving new levels of organizational excellence is presented.
Background
Over the past quarter century or so several transformational strategies have been employed to help manufacturers become more competitive. Indeed, as the markets have become more globalized, there is an ever-increasing imperative for such transformations to be in place just for today’s suppliers to remain in business. We will now consider just a few of these tools and how to utilize them in combination to achieve unprecedented reliability and enhance competitive advantage.
Two of the major tools that have been more successful than others are Six Sigma and Lean manufacturing. The first of these tools, Six Sigma, is a precision technology. In other words, here is a change process that emphasizes the value of adding precision to relentlessly drive out variation. Six Sigma relies heavily on the application of extensive, specialized technical training provided to a network of core practitioners, the most common of which are “Black Belts” and “Green Belts.”
Lean manufacturing, in contrast, is most commonly associated with a relentless drive to eliminate various wastes associated with the manufacturing process. Specifically, the consumption of any company resource for any purpose that does not create value for a customer. The tools used in lean manufacturing such as Kaisen, the 5 S’s method, value stream mapping or flow charting to assist in set-up reduction or process step elimination, mistake proofing and others, are generally rolled out to the bulk of the workforce. These tools are often less complicated than many of the statistical techniques used in Six Sigma and are therefore easier for the ordinary person on the shop floor to not only understand, but to embrace and even vigorously support this change process.
Since around the turn of the century, companies have started combining Six Sigma and Lean manufacturing to achieve greater benefits than either technology can offer alone. This combination of tools has become known as Lean Six Sigma. Consider the following observations:
- Lean manufacturing does not bring a process under statistical quality control
- Six Sigma alone cannot dramatically improve the speed of business processes
- Both business improvement technologies enable substantial cost reductions and reduce complexity
- Adding Lean to Six Sigma emphasizes excellence achieved through speed
Lean Six Sigma is a business improvement methodology that maximizes value by achieving fast rates of improvement in customer satisfaction, cost, quality, process speed, and invested capital. Successful implementation can be measured through delighting the customer by delivering higher levels of product quality or quality service while also delivering results in shorter time frames. Internally, process users must emphasize teamwork and openness in sharing ideas across the organization to ensure the problem-solving efficiency is maximized. At the same time, there has to be an insistence that all decisions will be based on data and hard facts, not assumptions, perceptions or other types of hypotheses. The results of this synergistic approach has helped companies to reduce manufacturing overhead and quality costs by 20% and inventory by 50% in less than two years.2
Using Lean Six Sigma
At the heart of the Lean Six Sigma process is the DMAIC (Define, Measure, Analyze, Improve and Control) problem-solving method from Six Sigma combined with a selection of Lean manufacturing tools. The specific Lean methodologies will vary depending on the application and can be a result of the specific training received early in the implementation process.
In the Define phase, a team charter should be discussed and agreed for the project. This exercise typically involves process mapping, reviewing existing data about the process or problem and obtaining any customer data or input related to the project. Finally, a preliminary project plan and critical success factors or guidelines for the project to be successful are developed. Typical quality tools employed may include a SIPOC (Suppliers, Inputs, Process, Output and Customers) process map, voice of the customer, Kano model, stakeholder analysis, affinity diagrams and Critical-to-Quality (CTQ) tree.
The second step is to Measure the process. It is very important to ensure existing measurement systems are up to the task. A good check could be to generate a list of potential measurements to be utilized for the project and generate a prioritization matrix to achieve consensus as to what measurements must be in place to succeed. Significant data gaps can arise when measurement systems turn out to be inadequate, followed by delays while developing and implementing the necessary monitoring capabilities. Once the company is sure they are ready to proceed, it is necessary to observe the process in action while gathering essential data over pre-determined time periods. While performing these tasks, a more detailed process map should be generated. Process Cycle Efficiency (PCE) is often employed to determine what work is value-added (to the customer), not value-added or non-value-added but required to produce the final product or service. A variety of continuous improvement tools of varying complexity are brought to bear to correctly interpret the data gathered during the measurement phase such as Time Value Analysis, Pareto Analysis, Failure Modes and Effects Analysis (FMEA) and statistical process control charts.
Analyze or analysis of the data is the third step in the cycle. Here we confirm sources of delay, identify wastes (both wasted process steps and wastes that are generated from the process), list causes of poor quality and begin to determine root causes of these inefficiencies in the work processes. This is the point where we begin to see some rudimentary tools for Root Cause Analysis (RCA) appear including 5Why’s analysis, brainstorming, and Cause-and-Effect Diagrams. There is no doubt that each of these quality management tools is effective when applied correctly but it is also certain that these techniques are more suited for quick action than for the more rigorous analysis provided by more advanced Root Cause Analysis techniques.
Figure 1 provides a relative comparison of these tools as follows:
Figure 1: Comparison of Analytical Processes to RCA Essential Elements
The limitations imposed by more simple quality tools primarily manifest themselves in the form of physical solutions often unfortunately combined with a tendency to assign blame for human error to the employer’s greatest asset, the people who made those decisions. In this manner, the symptoms of the disease are constantly addressed, not the disease itself, with the results that after a couple of years of program implementation little overall progress has been made. By integrating advanced RCA into your Lean Six Sigma process, you will not only address physical and human root causes, you will resolve latent systemic or organizational issues that are the real, underlying root causes that must be addressed to achieve quantum improvements in operational performance.
In the Improve step of the process, the focus is on reducing different types of wastes such as defects, unnecessary or inefficient process steps and physical wastes generated by the process, including both expected and unexpected waste streams. Here is where the benefits of Lean really kick in. Tools such as set-up reduction, improved queuing methods, 5S and kaizen events are invaluable in achieving the process speed increases that are required for a successful Lean Six Sigma implementation. Here again, by adding advanced RCA to your arsenal, more intensive investigation will result in higher quality recommendations for corrective action, increasing the effectiveness of your Lean Six Sigma project.
Finally, in the Control phase, it is necessary to implement corrective actions, develop key performance metrics to measure the resulting improvement and track performance. A variety of quality tools are readily available for this purpose such as statistical control charts, process flow charts or diagrams, Pareto charts, quality control process charts and standardization of work documentation.
Advanced Root Cause Analysis
RCA is often considered to be a soft tool, specifically, a very strong learning tool. RCA simply put is a structured process designed to uncover the causes of any undesirable event occurring within a given system. Although RCA is designed to be a proactive tool, the initial use at a company is typically reactive. Trigger events initiating investigations often include fires, explosions, personnel injury, and the generation of off-specification product, environmental releases and major equipment failures.
Like Lean Six Sigma, when measuring the impact of chronic issues or chronic processing variations, a hard tool is utilized such as Failure Modes and Effects Analysis (FMEA) or Pareto analysis to evaluate the order in which problems or issues should be addressed. With both methodologies the focus is on driving out chronic losses.
When performing a Root Cause Analysis, it is often useful to employ depictive devices specifically designed for use with RCA. A logic tree is a common and particularly useful method of describing the output from a completed RCA.
The logic tree provides a straightforward structure for showing how a set of cause-and-effect relationships that queued up in a particular sequence at a particular time resulted in an undesirable outcome such as the generation of waste to occur. These cause-and-effect relationships should always be validated with hard evidence to ensure the accuracy of the analysis and increase confidence that solutions identified by a Lean Six Sigma project will be effective in ensuring rapid results from corrective actions.
A simple logic tree has the following form:
Figure 2: A PROACT® Logic Tree
In essence, a logic tree tells a story. The story can be told from the top down or from the bottom up. In either case, we have a simple way to show the cause-and-effect relationships to such a degree that we have an opportunity to eliminate the event and failure modes completely. This is, of course, the bar we are required to set if we intend to fully realize Six Sigma capability.
References:
George, Michael L., Rowlands, Dave, and Kastle, Bill, 2004, What is Lean Six Sigma?, George Group, pp 9-10.
George, Michael L., 2002, Lean Six Sigma: Combining Six Sigma Quality with Lean Speed, McGraw-Hill Companies, Inc., p.4.
Latino, Robert J., April 2007, “Root Cause Analysis vs. Shallow Cause Analysis,” Industrial Maintenance and Plant Operation.
About the Author
Victor E. May has more than 35 years of progressive managerial experience in reliability, engineering, operations and business process improvement at global Fortune 500 corporations. His expertise includes the training, facilitation, and mentoring of individuals and teams leading efforts involving root cause analysis, human error reduction and failure investigation. Mr. May received his B.S. in Materials Engineering from North Carolina State University.
Recent Posts
AI and Site Reliability Engineers: Lessons from the Field.
Smarter, Faster, Deeper: How AI Is Transforming Root Cause Analysis in Software and Beyond
North America’s Looming Power Shortfall: A Root Cause Analysis for the Grid—and Beyond
Preventing EV Charger Downtime: How Smart Test Strategies Act as Root Cause Analysis in Action
Root Cause Analysis Software
Our RCA software mobilizes your team to complete standardized RCA’s while giving you the enterprise-wide data you need to increase asset performance and keep your team safe.
Root Cause Analysis Training