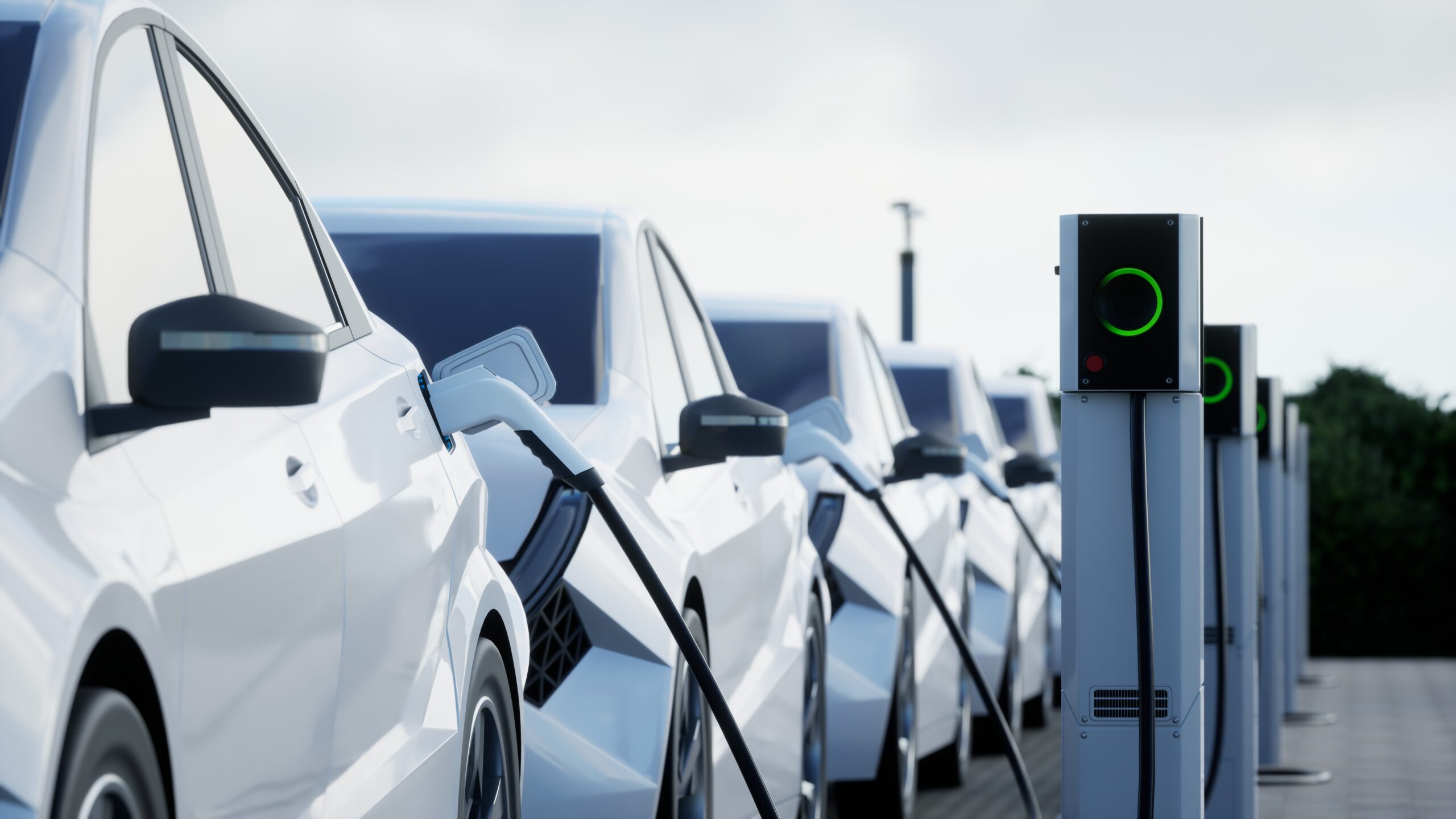
Preventing EV Charger Downtime: How Smart Test Strategies Act as Root Cause Analysis in Action
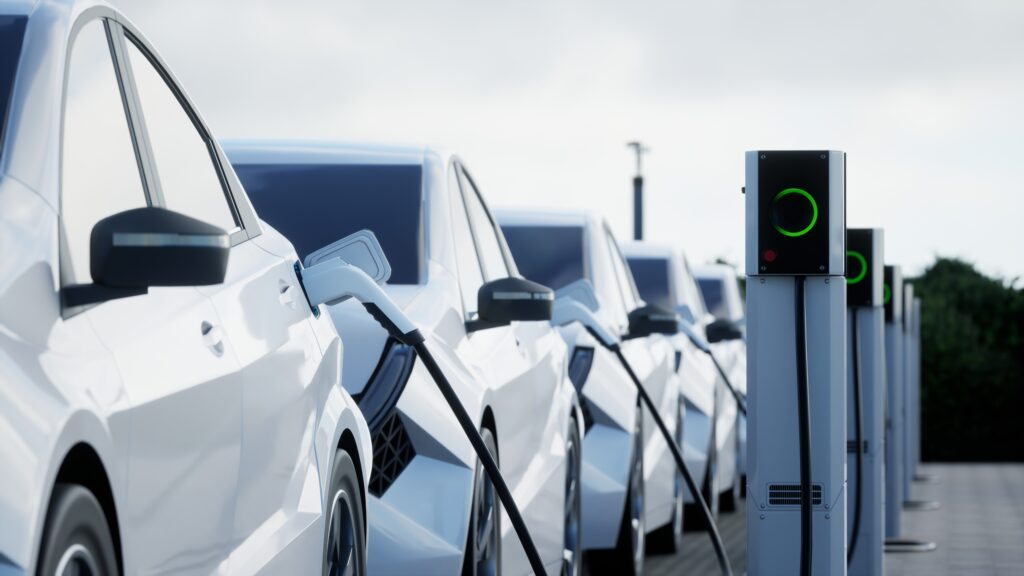
The push for widespread electric vehicle (EV) adoption has put a fresh spotlight on an old reliability challenge: keeping critical equipment running when drivers need it most. For EV charging networks, that means chargers must be ready, safe, and efficient every time a car pulls up. But as the recent Charged EVs report on test strategies points out, the gap between design and real-world uptime often hides a mess of root causes—faulty power modules, thermal breakdowns, software bugs, or even basic installation mistakes that stay buried until chargers fail on site.
So how can operators and OEMs prevent these headaches? The answer is to treat every test procedure not just as a quality step, but as a kind of preventive Root Cause Analysis (RCA) that catches hidden problems before they ever hit the road.
The Hidden “Why” Behind Charger Failures
Unplanned charger failures don’t come out of nowhere. Like any complex system, an EV charger can hide weak spots that sneak in during design, assembly, or even on-site installation. When chargers break down, the usual root causes include:
- Overheating caused by poor thermal design
- Defective power modules
- Software bugs in the power flow or payment systems
- Weather or moisture getting inside the cabinet
- Poor installation work or wiring slip-ups
When these flaws slip through, the result is lost revenue, frustrated EV drivers, and a damaged reputation for charger uptime.
Testing as Proactive Reliability
This is where tough testing comes in—not just as a box to tick for QA, but as a core reliability safeguard. Just like a good RCA after a breakdown asks “why” again and again, smart test plans stress equipment under real-world conditions to catch failure modes early.
For instance, high-power DC fast chargers go through thermal cycling tests to check how heat sinks, power electronics, and connectors stand up to repeated heavy loads. EMC (Electromagnetic Compatibility) testing checks that stray interference won’t crash the system when it’s installed in busy urban settings. On top of that, site inspections catch wiring or grounding issues that might otherwise lead to surprise shutdowns.
Together, these tests work like an early RCA loop—catching flaws, flagging fixes, and making sure they’re handled before they show up in the real world.
Connecting to Proven RCA Tools
Reliability professionals will recognize how this approach links to classic reliability tools. Design teams often pair real-world testing with Failure Mode and Effects Analysis (FMEA) to map out possible weak points and prioritize which ones to fix first. Feeding actual test data back into an FMEA keeps assumptions honest and bridges the gap between theory and what happens in the field.
Fault Tree Analysis (FTA) is another tool that goes hand in hand. FTA lets teams map out possible pathways to failure, from a single faulty module to a chain reaction that takes a charger offline. The better your test data, the sharper your fault tree—and the stronger your prevention plan.
When teams log all this in a modern RCA tool like EasyRCA, they can trace problems, map causes, and ensure fixes stick. That’s the difference between “we fixed it” and “it won’t happen again.”
Powering Predictive Maintenance and Digital Twins
Smart operators aren’t stopping at just passing lab tests. Many now use test data to fuel predictive maintenance. By watching trends—like temperature drift or power module wear—teams can spot early warning signs and plan service before breakdowns happen.
Some networks even use digital twins: virtual models of real-world chargers running side by side with live condition monitoring. That means teams don’t just react when a charger goes down—they see which ones are starting to fail and fix them in time.
Testing for Compliance and Building Trust
Solid testing isn’t just good practice—it’s how networks stay on the right side of global standards. From IEC safety requirements to ISO quality rules, testing provides the proof regulators need. But the real payoff is bigger than just ticking a compliance box. When chargers work every time, networks win user trust—a big factor in keeping drivers loyal and confident to go electric.
The Takeaway: Test to Prevent, Not Just Detect
In the EV charging world, waiting to troubleshoot problems in the field just doesn’t cut it. The smartest teams see every test plan as a living RCA tool—one that hunts down hidden issues, explains the “why,” and stops failures before they ever reach the road.
At Reliability.com, we know true reliability is about building resilience in from the start. By combining solid test strategies, time-tested RCA tools like FMEA and FTA, and modern platforms like EasyRCA, charger operators can deliver the uptime that keeps the shift to electric moving forward.Want more practical tips on using RCA to boost reliability in your industry? Check out more resources and real-world examples at Reliability.com/resources.
Recent Posts
Preventing EV Charger Downtime: How Smart Test Strategies Act as Root Cause Analysis in Action
UK Retail Cyberattacks: What M&S, Harrods & Co-op Reveal About Cybersecurity and Root Cause Analysis
Richmond Water Crisis Exposes Infrastructure Vulnerabilities: Why RCA Is Key to Long-Term Solutions
Introducing RCA Turbo: Instant Root Cause Analysis with a Snap or a Sentence
Root Cause Analysis Software
Our RCA software mobilizes your team to complete standardized RCA’s while giving you the enterprise-wide data you need to increase asset performance and keep your team safe.
Root Cause Analysis Training