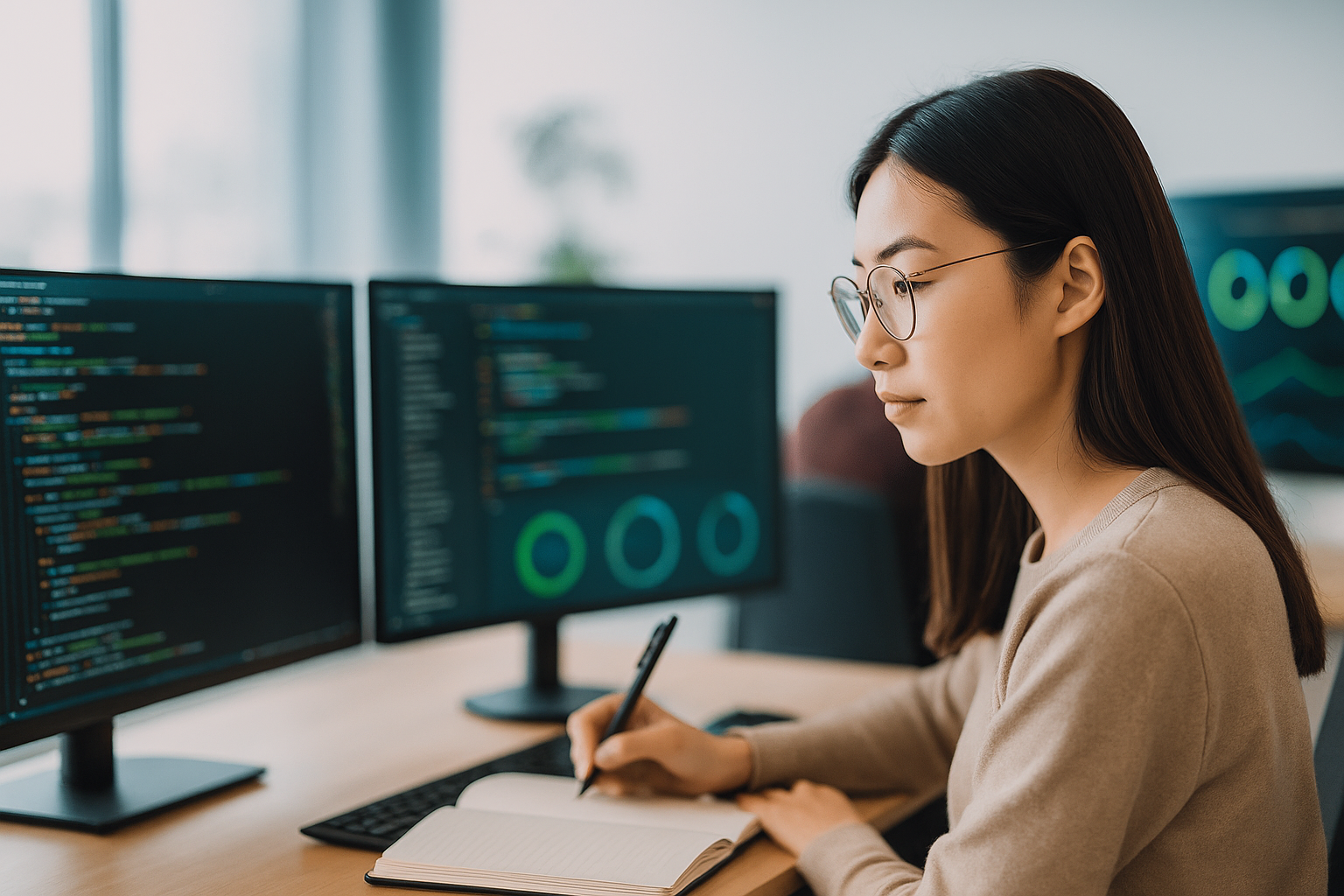
Understanding the Role of a Site Reliability Engineer (SRE)
Reading Time: 3 minutes
In today’s digital-first world, businesses rely on highly available, scalable, and resilient systems to maintain seamless operations. A single instance of downtime can lead to significant financial losses, customer dissatisfaction, and operational inefficiencies. This is where the role of a Site Reliability Engineer (SRE) becomes essential. What is a Site Reliability Engineer (SRE)? A Site Reliability Engineer (SRE) is a
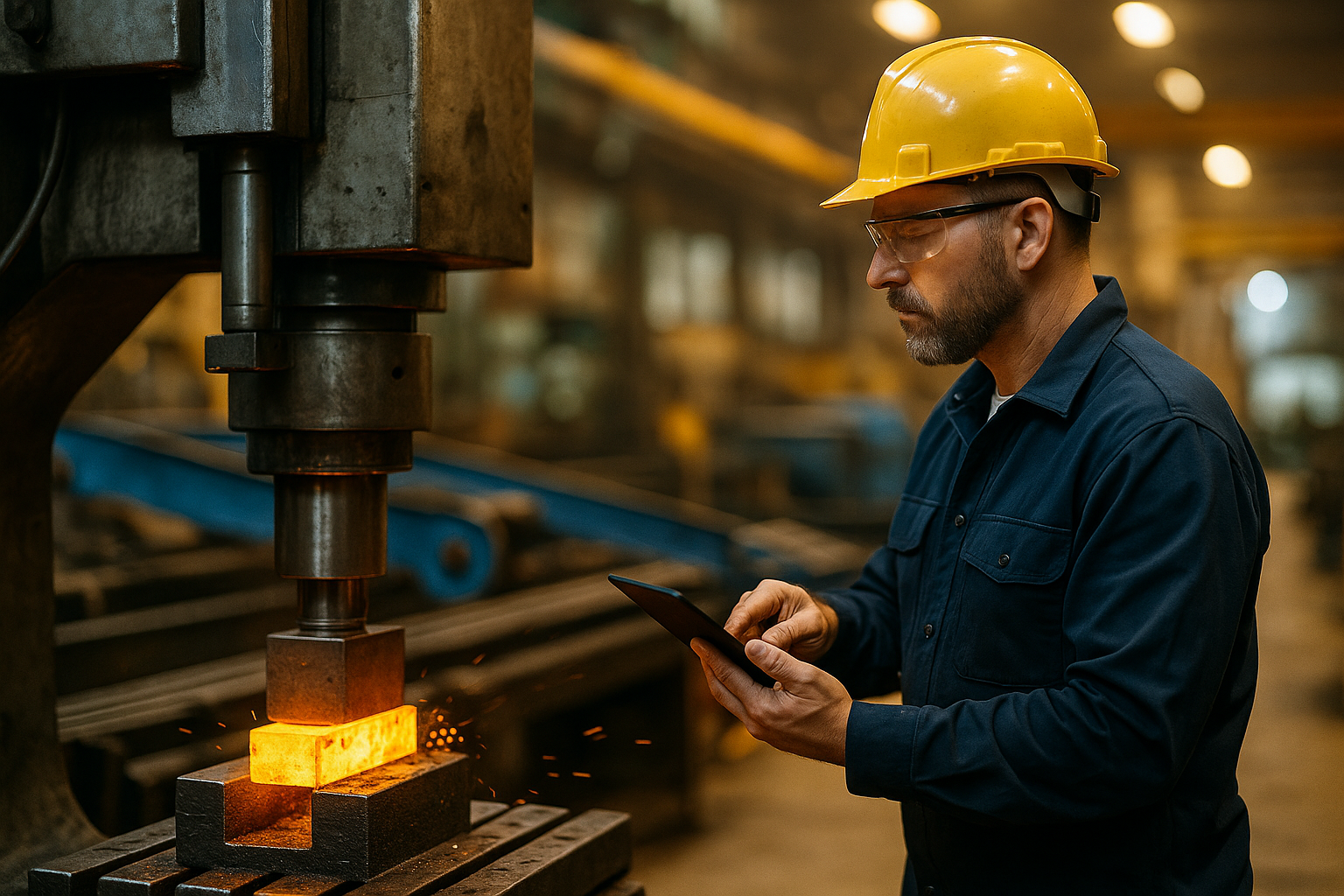
The Role of a Reliability Engineer in the Industrial and Manufacturing Sectors
Reading Time: 2 minutes
In industries such as manufacturing, pharmaceuticals, and energy, equipment reliability is critical to maintaining efficiency, reducing downtime, and ensuring workplace safety. The Reliability Engineer plays a crucial role in achieving these objectives by focusing on preventive maintenance, failure analysis, and continuous improvement strategies. What is a Reliability Engineer? A Reliability Engineer is a professional dedicated to improving asset performance by
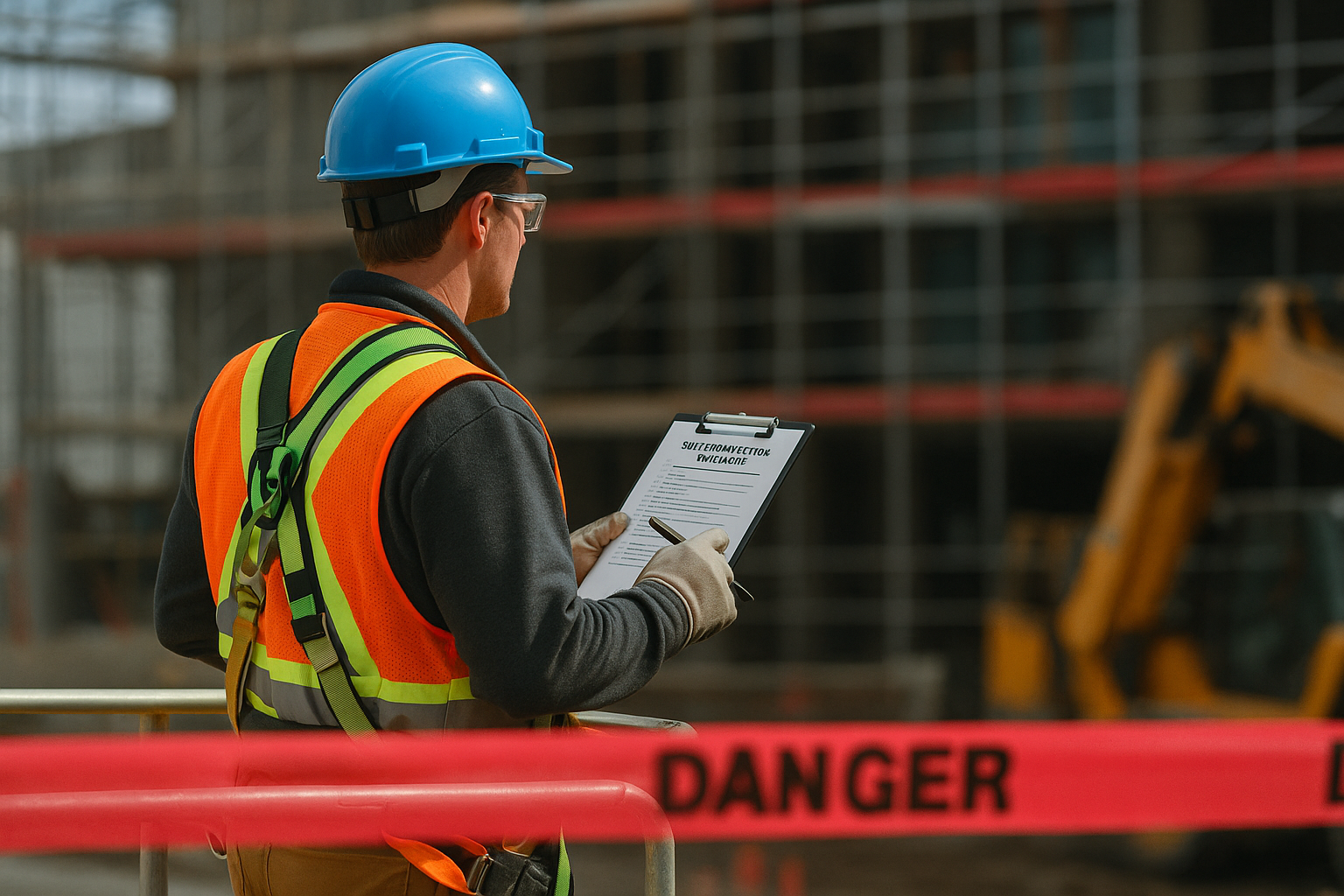
The Importance of Root Cause Analysis in Health, Safety, and Environment (HSE)
Reading Time: 3 minutes
Health, Safety, and Environment (HSE) are critical pillars of success for industrial operations. A robust HSE program protects employees, ensures compliance, and minimizes environmental impact. However, even the most comprehensive HSE strategies are not immune to incidents. When accidents, environmental violations, or health concerns arise, Root Cause Analysis (RCA) becomes an indispensable tool for driving improvements and preventing recurrence. The
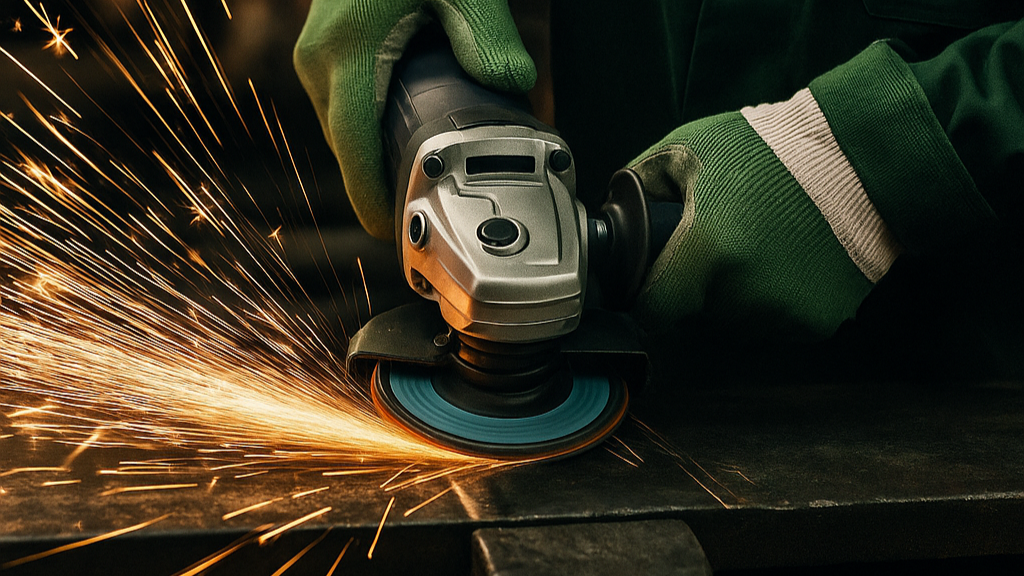
RCA Templates: A Critical Tool for Effective Problem-Solving
Reading Time: 2 minutes
Root Cause Analysis (RCA) is a cornerstone of reliability engineering, providing a structured approach to identifying and addressing the root causes of failures. A well-designed RCA template simplifies this process, ensuring consistency and thoroughness across teams. What is an RCA Template? An RCA template is a pre-formatted document or framework designed to guide teams through the RCA process. It serves
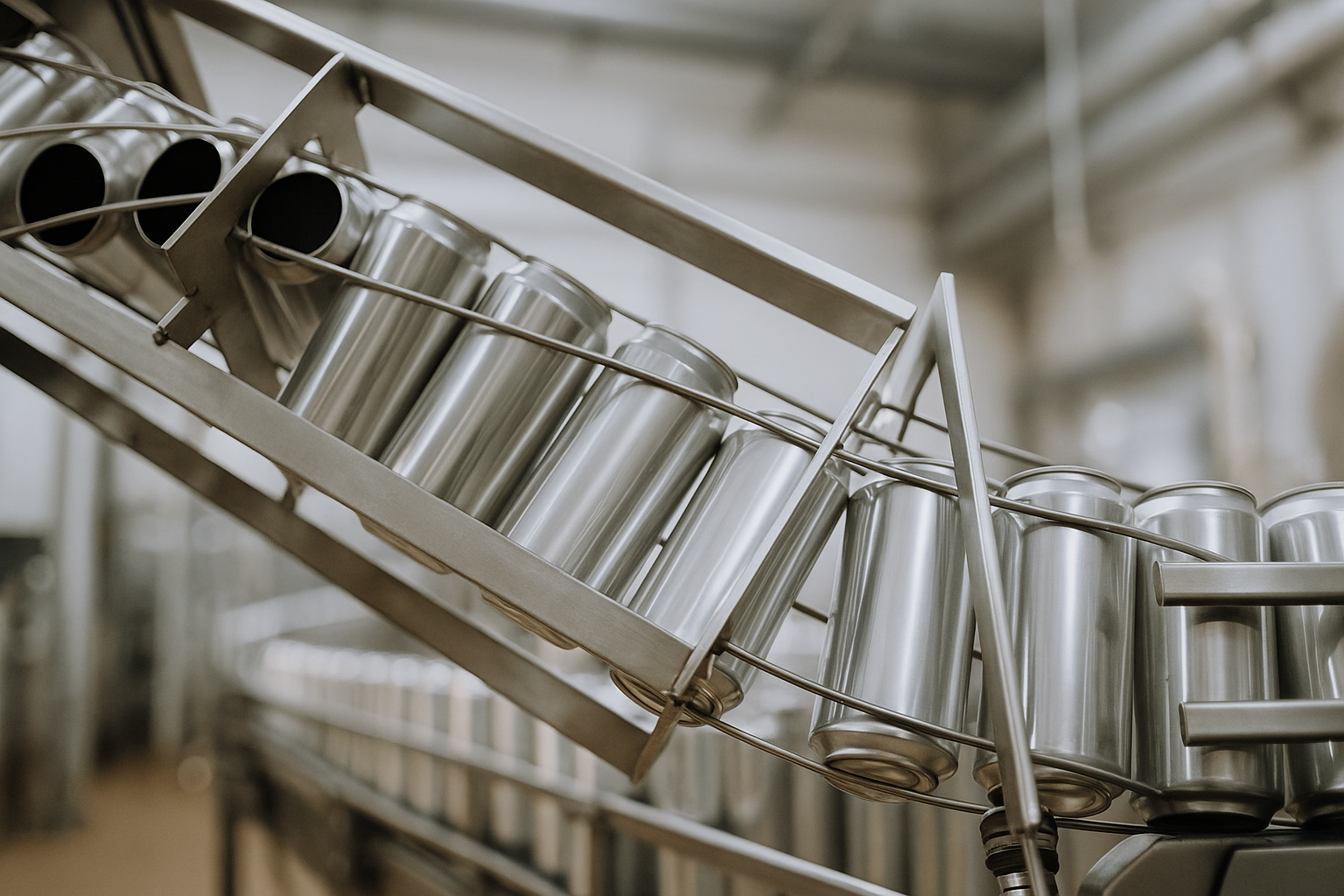
Using the 5 Whys Technique for Root Cause Analysis in Complex Environments
Reading Time: 4 minutes
In today’s fast-paced business world, identifying, and solving problems efficiently is key to maintaining operational success. One method that has stood the test of time in uncovering the root cause of issues is the 5 Whys technique. Straightforward yet extremely effective, it helps teams drill down to the core of a problem by asking “why” multiple times until the root
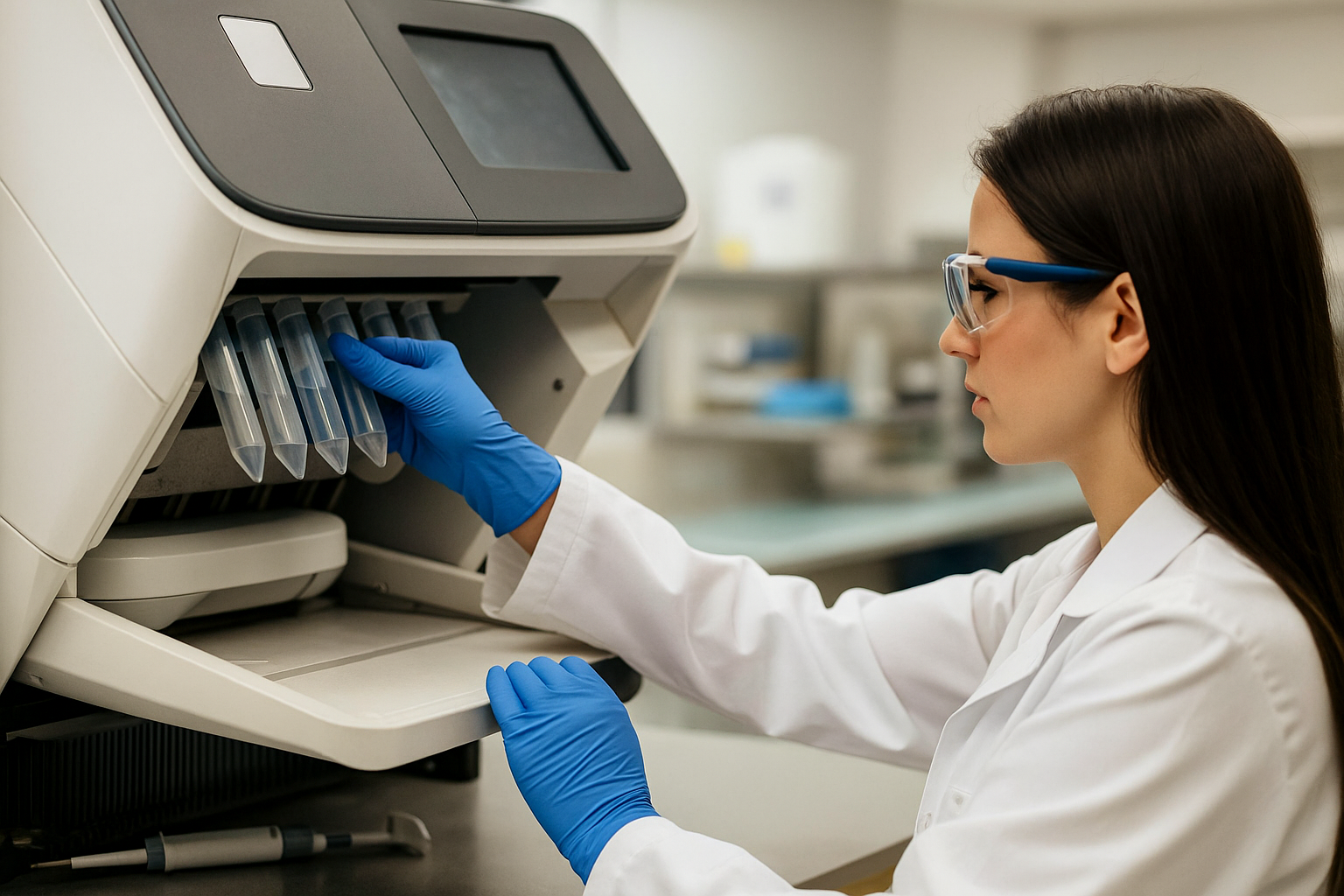
How Root Cause Analysis Tools Can Prevent Equipment Failures in Healthcare
Reading Time: 3 minutes
In the fast-paced world of healthcare, where it’s a matter of life and death, equipment failures can have serious consequences. When an important machine stops working, it can jeopardize patient safety, disrupt care, and even put life on the line. Fortunately, Root Cause Analysis (RCA) tools can help healthcare professionals identify and prevent these failures before they occur. Let’s explore
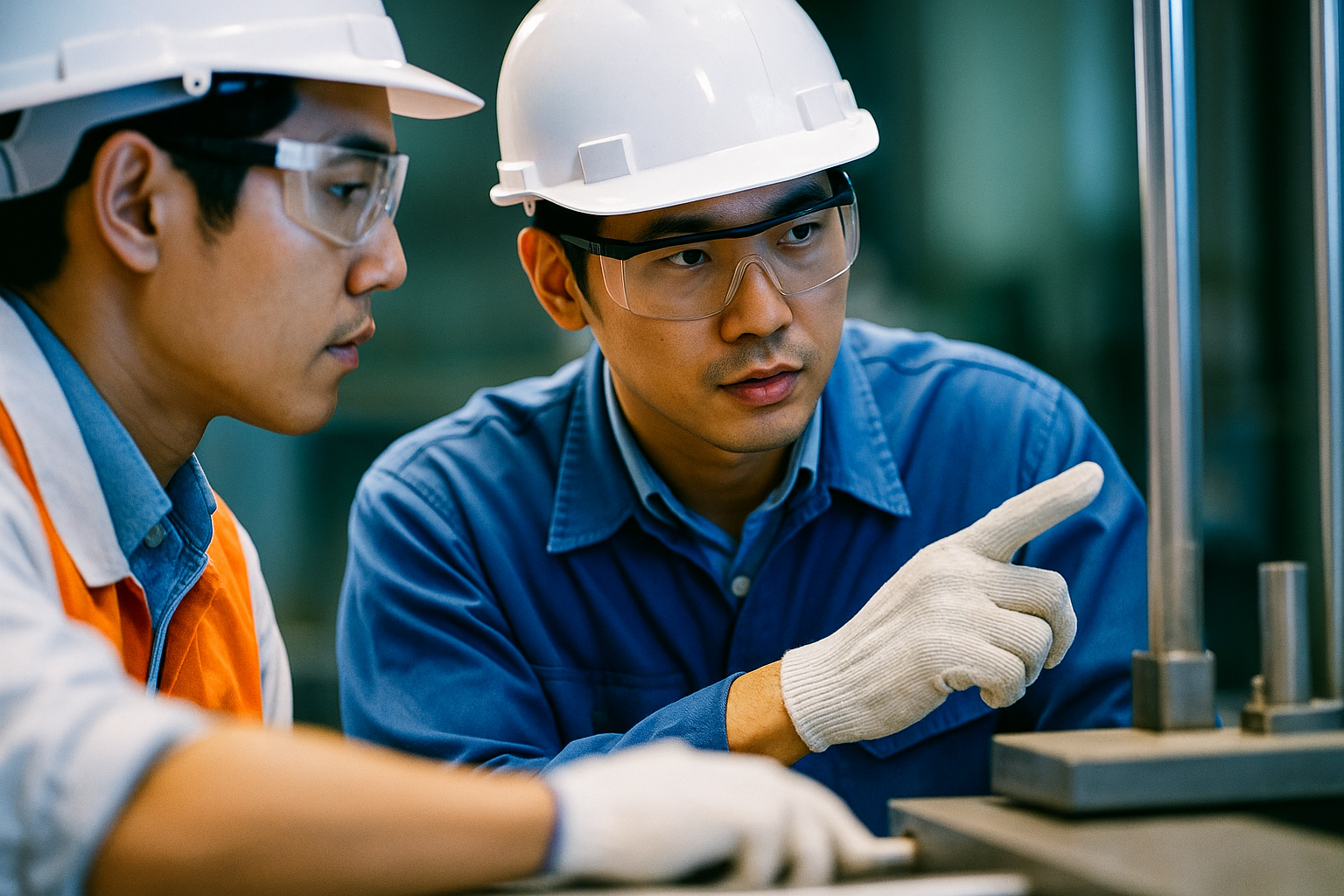
A Step-by-Step Guide to Using Root Cause Analysis Tools for Improved Reliability
Reading Time: 3 minutes
Reliability has become a cornerstone of operational excellence in today’s fiercely competitive industrial landscape. Unexpected failures can lead to significant downtime, increased costs, and potential safety hazards. To effectively address these recurring challenges, organizations turn to Root Cause Analysis (RCA) tools, which help uncover the underlying causes of problems and prevent their recurrence. This comprehensive guide will take you step-by-step
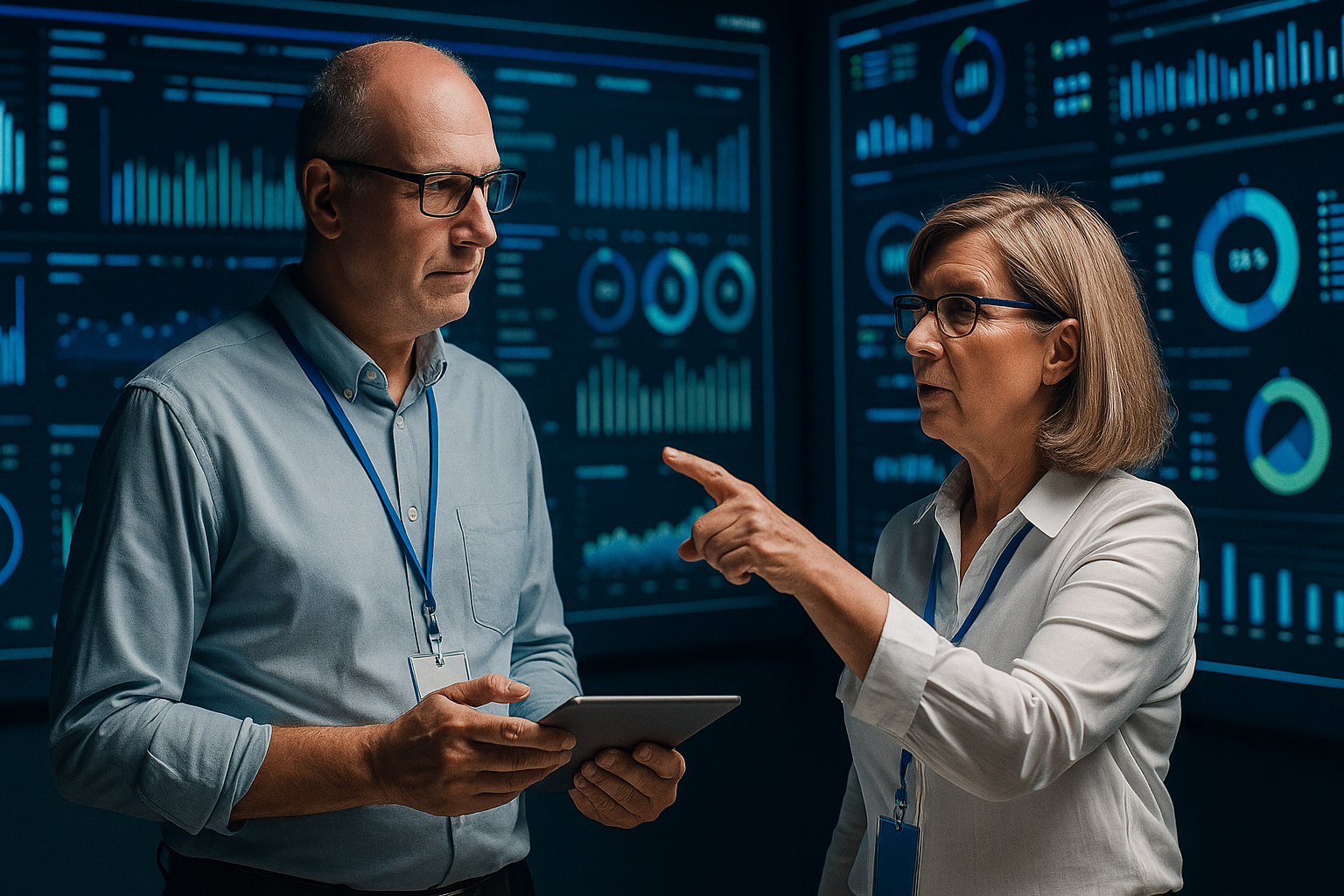
How to Choose the Right Root Cause Analysis Tool for Your Reliability Program
Reading Time: 4 minutes
In today’s fast-paced industrial environments, ensuring the reliability of your systems is critical to maintaining productivity and avoiding costly failures. At the heart of any effective reliability program is the ability to identify and address problems before they escalate. One of the most powerful methods for achieving this is Root Cause Analysis (RCA), a process that helps uncover the true
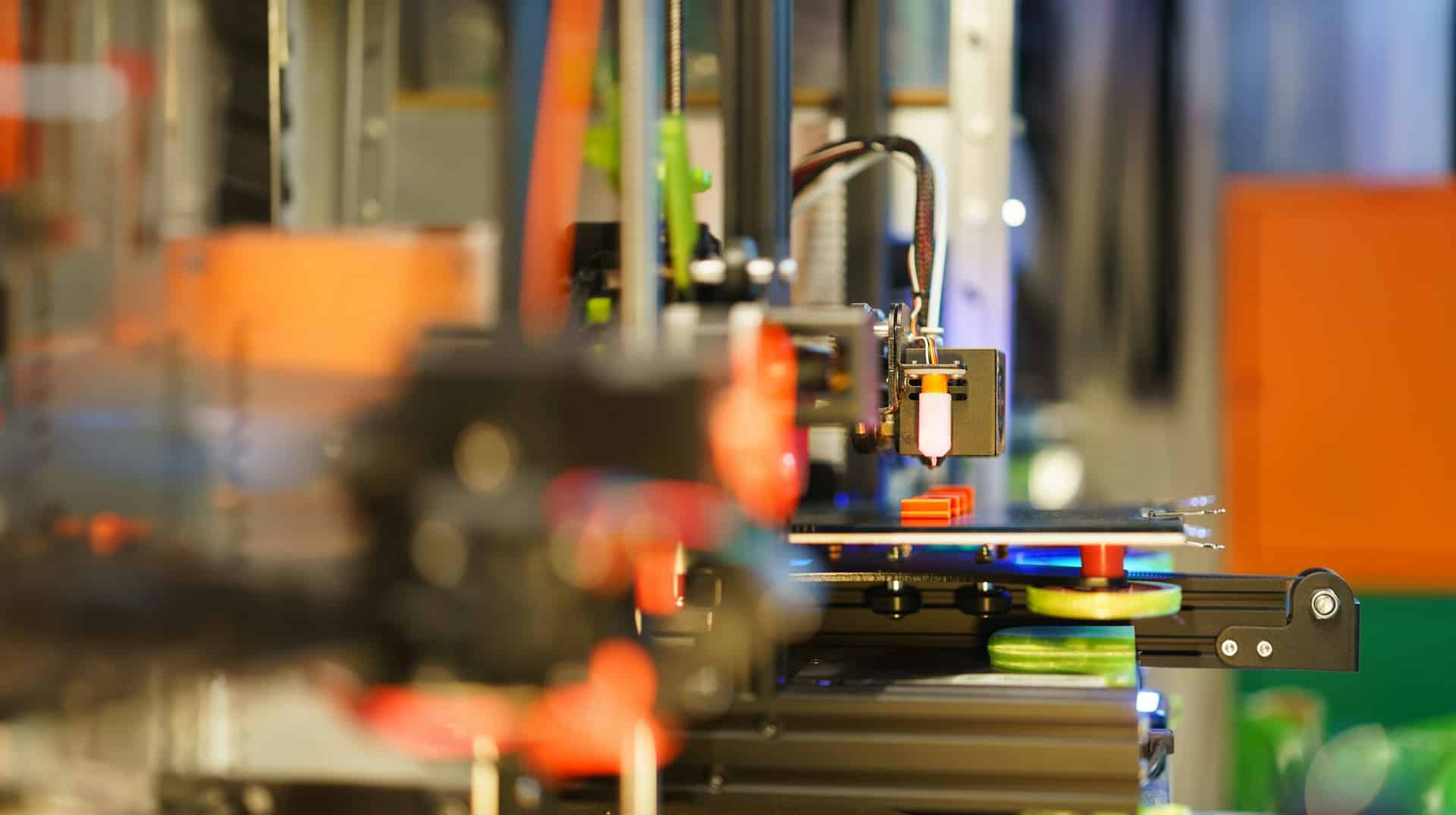
How to Perform Root Cause Investigations?
Reading Time: 6 minutes
When failures occur, they not only disrupt productivity but can also lead to significant costs and safety risks. To prevent these issues from recurring, it’s essential to identify the root cause of the problem. Root Cause Investigation (RCI) is a powerful tool that helps organizations get to the heart of failures, ensuring long-term reliability and operational excellence. The purpose of
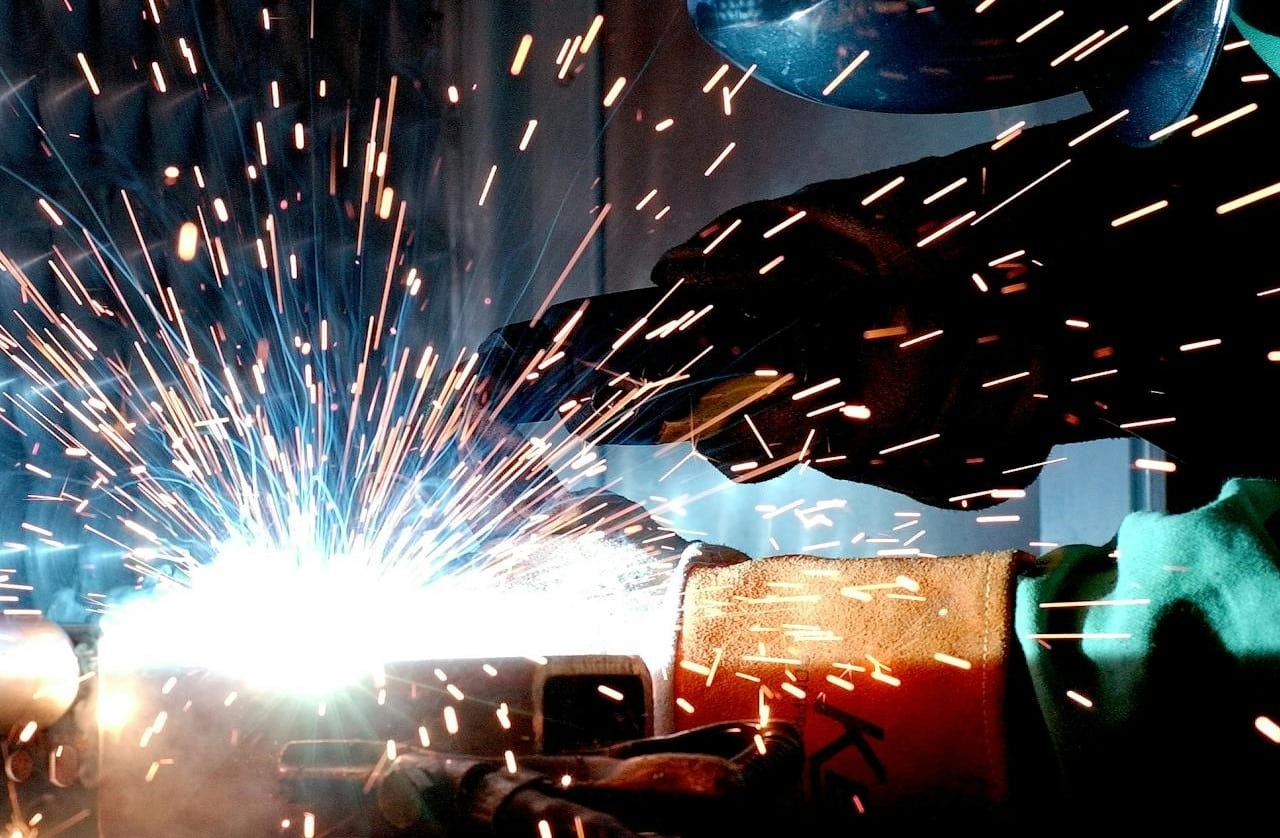
Post-Incident Analysis for Enhanced Reliability
Reading Time: 5 minutes
With over two decades in business – spanning strategy consulting, tech startups and executive leadership – I am committed to helping your organization thrive. At Reliability, we’re on a mission to help enhance strategic decision-making and operational excellence through the power of Root Cause Analysis, and I hope this article will be helpful! Our goal is to help you better
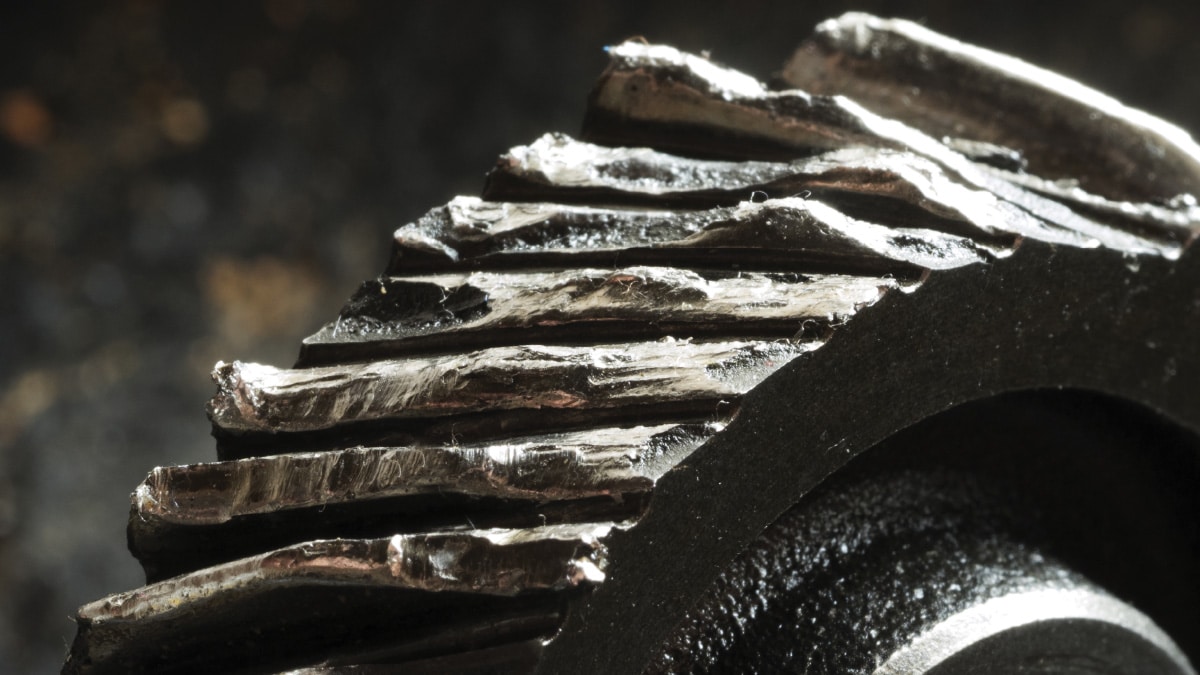
How To Conduct Incident Analysis?
Reading Time: 7 minutes
With over two decades in business – spanning strategy consulting, tech startups, and executive leadership – I am committed to helping your organization thrive. At Reliability, we’re on a mission to help enhance strategic decision-making and operational excellence through the power of Root Cause Analysis, and I hope this article will be helpful! Our goal is to help you better
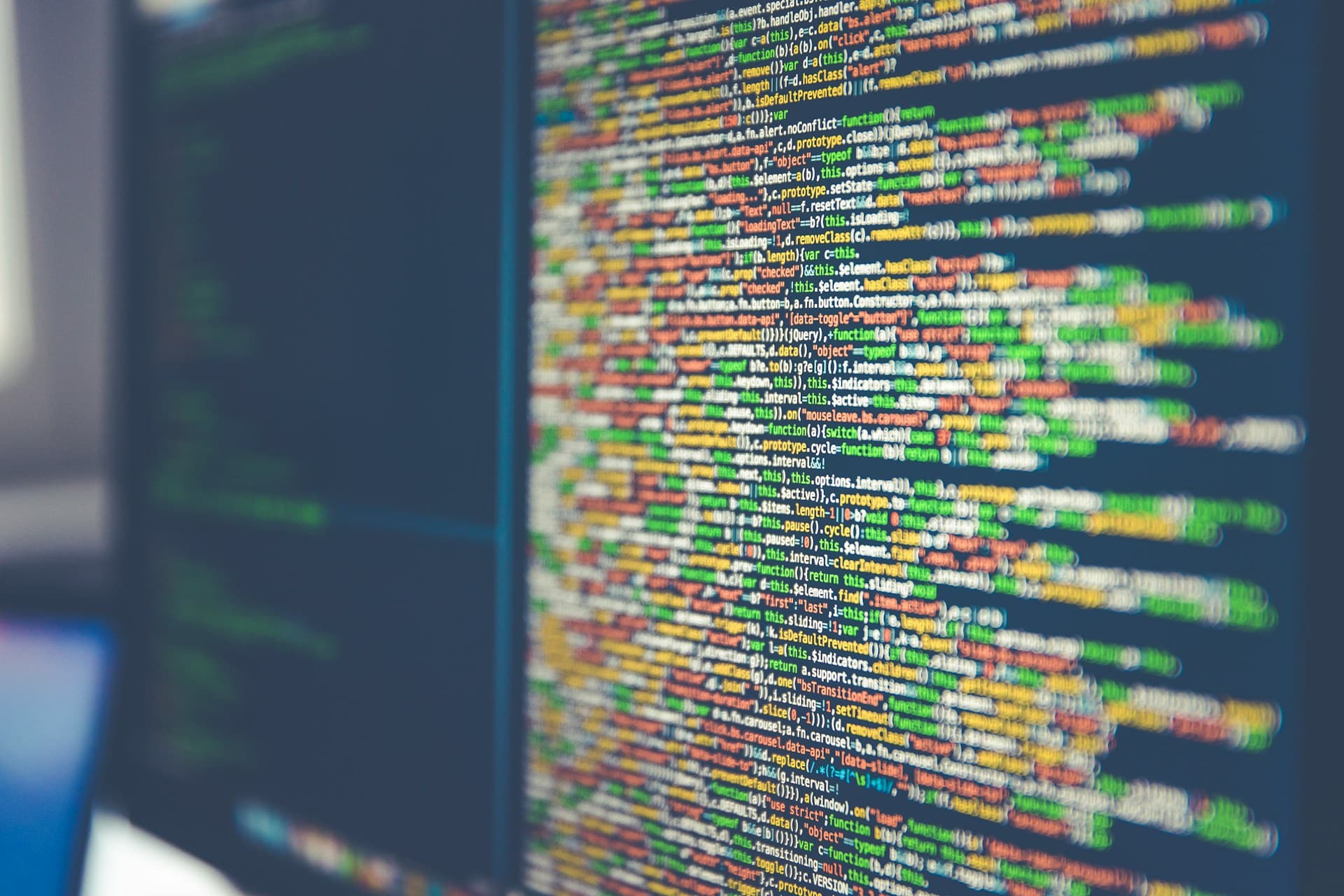
The Role of Artificial Intelligence in Reliability Engineering
Reading Time: 6 minutes
With over two decades in business – spanning strategy consulting, tech startups, and executive leadership – I am committed to helping your organization thrive. At Reliability, we’re on a mission to help enhance strategic decision-making and operational excellence through the power of Root Cause Analysis, and I hope this article will be helpful! Our goal is to help you better