INCREASE ASSET PERFORMANCE
WITH BETTER ROOT CAUSE ANALYSIS.
Reliability's PROACT® root cause analysis training and RCA software can quickly help your team capture ROI, increase asset uptime, and ensure safety.
What our customers are saying
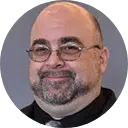
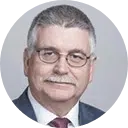
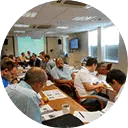
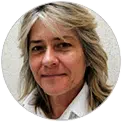

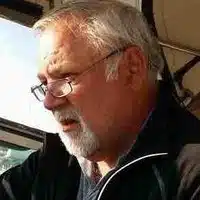
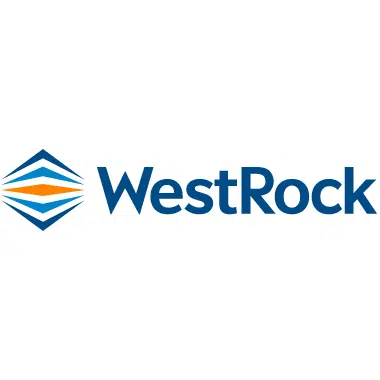
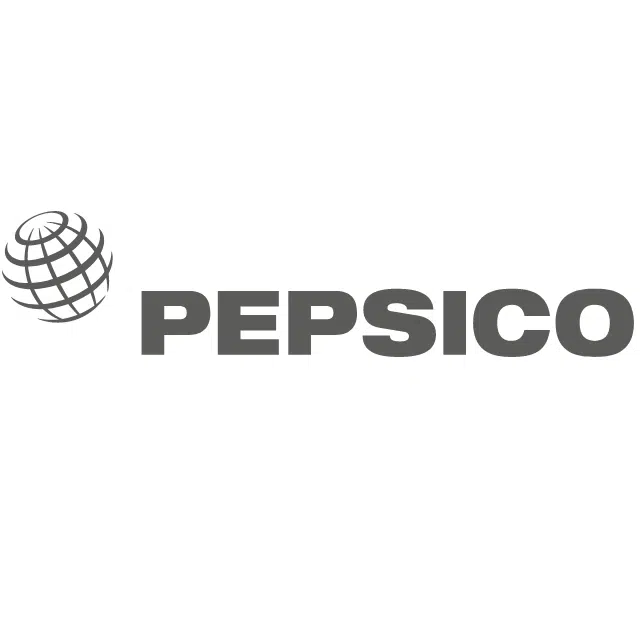
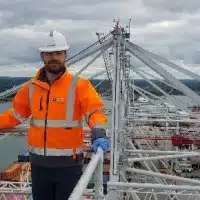
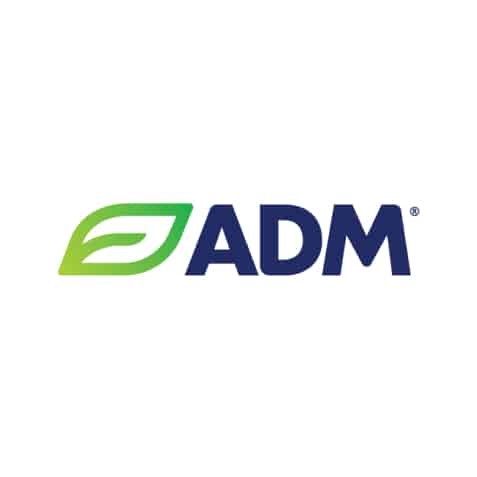
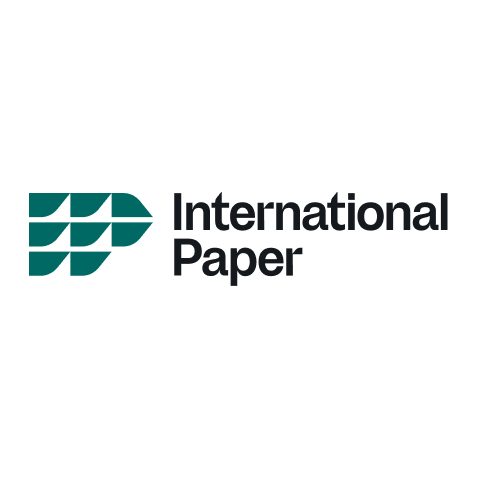
Build the reliability program of the future, today.
Root Cause Analysis Training
Root Cause Analysis Software
Our root cause analysis software EasyRCA mobilizes your team to complete standardized RCA’s while giving you the enterprise-wide data you need to increase asset performance and keep your team safe.
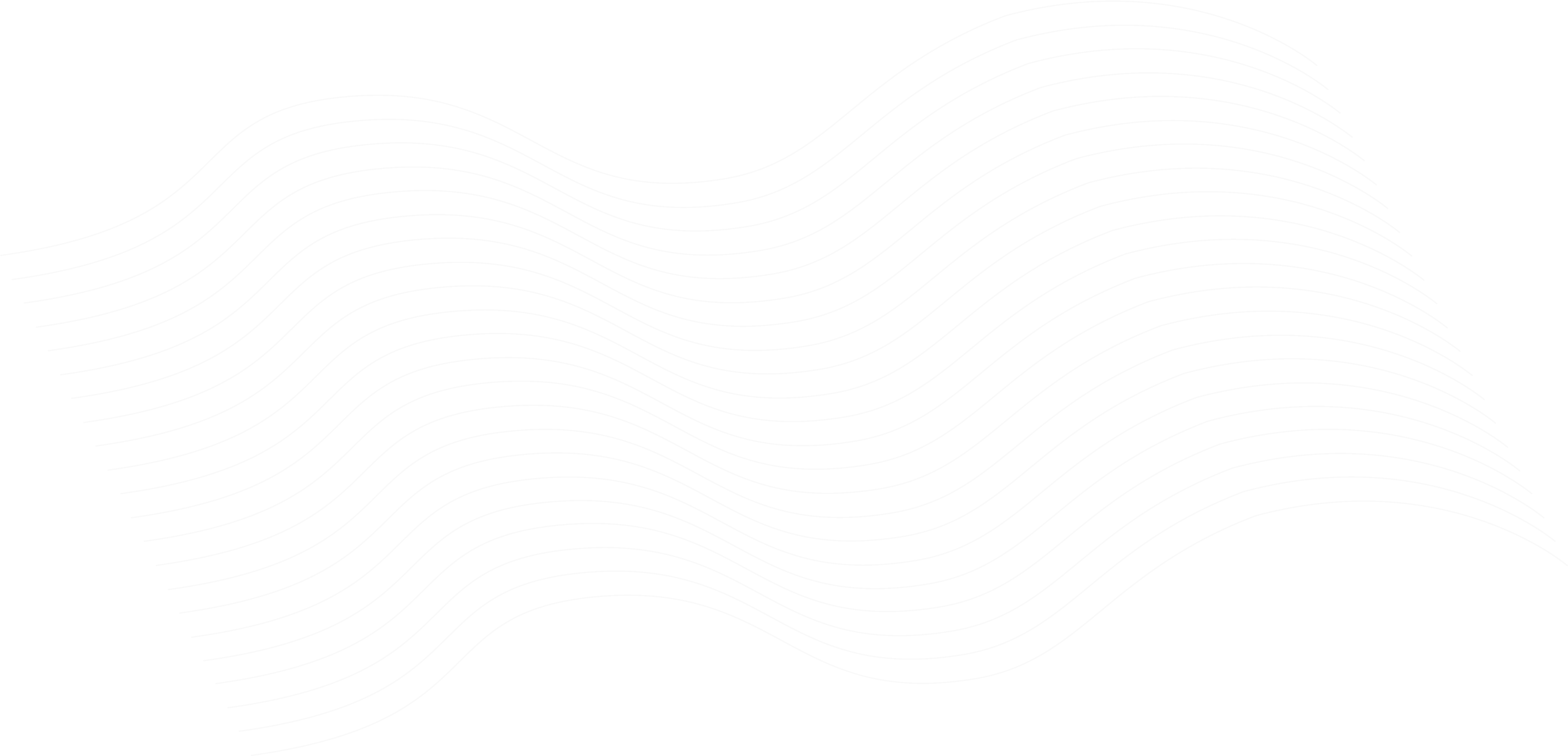
See How Root Cause Analysis Can Help You
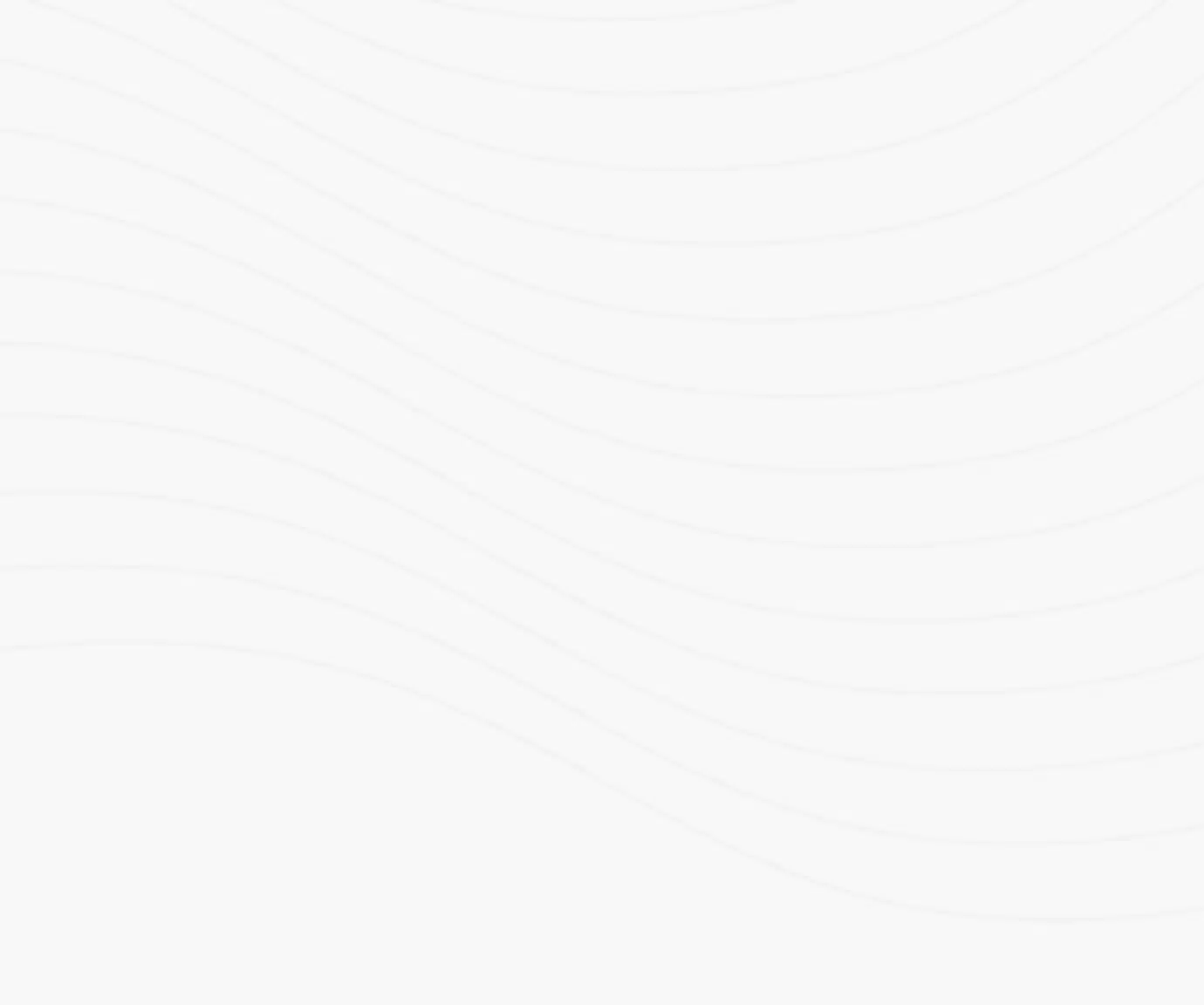
It's essential that your most critical assets are as reliable and safe as possible.
If your teams aren't conducting excellent and efficient root cause analysis, you're leaving significant ROI on the table.
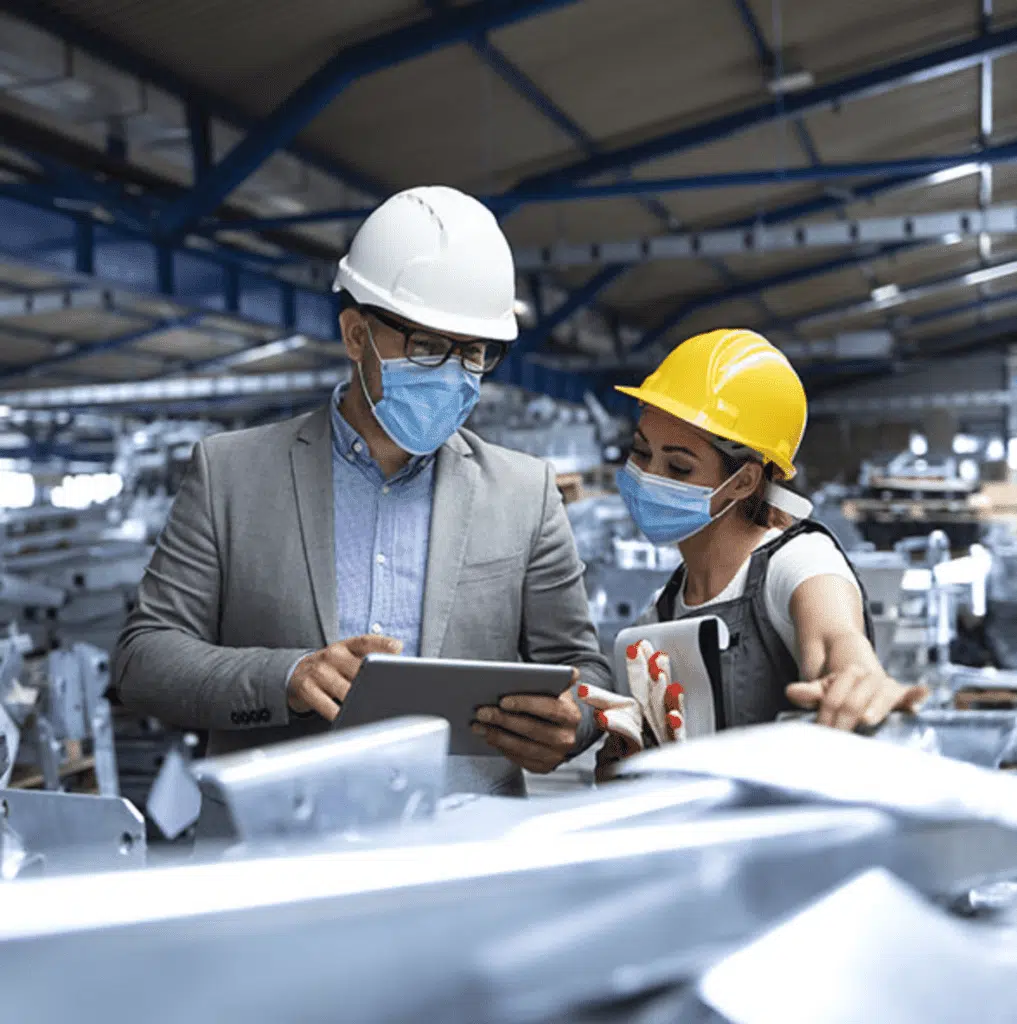
More RCA's in less time with better ROI.
Better data across multiple plants
Increased uptime and ROI from assets
Improved safety
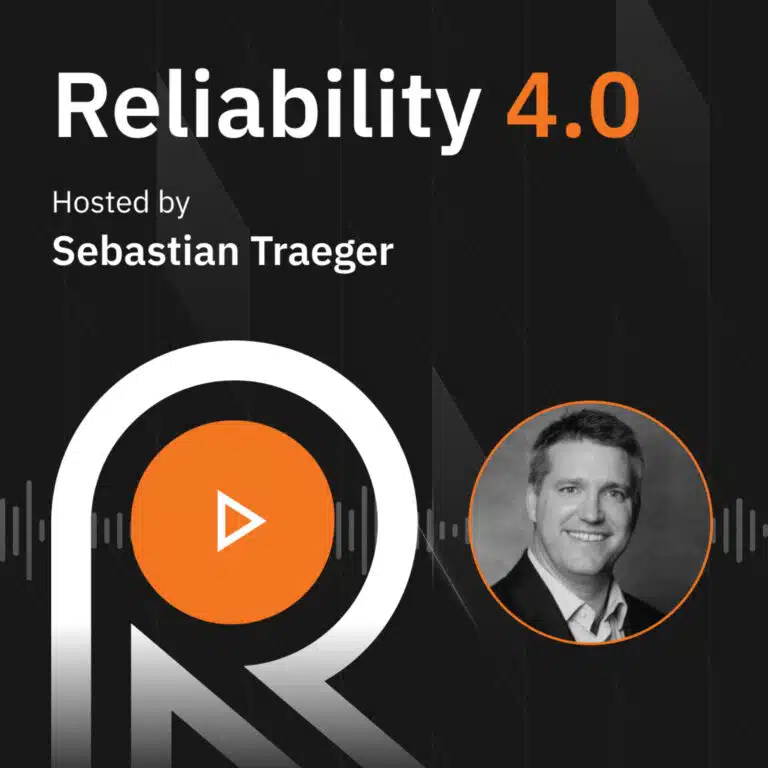
This podcast is your premier destination to unravel how cutting-edge technologies like AI, IoT, and Big Data are revolutionizing the way we approach reliability and maintenance in various industries. Our host, the CEO of Reliability.com, Sebastian Traeger, uses his extensive experience to illuminate the most pressing topics in the reliability engineering field today. The Reliability 4.0 Podcast is here to keep you informed and inspired, bringing you insightful discussions, interviews with leading experts, and real-world case studies. Subscribe now to never miss an episode!
What really makes or breaks a CMMS rollout? In this episode of Reliability 4.0, we sit down with Greg Christensen, host of CMMSradio, to unpack the lessons he’s learned personally and from hundreds of conversations with maintenance and operations pros navigating the world of CMMS and asset management.
We dig into:
🔸 Why CMMS projects fail (hint: it’s not the software)
🔸 How to build a business case for switching systems
🔸 What separates shiny tech from real process improvement
🔸 The role of leadership, training, and user buy-in
🔸 Where RCA fits into the big picture of long-term success
If you’re evaluating vendors, leading a digital transformation, or just trying to make your plant more reliable — this episode is full of real talk and hard-won insights.
This episode is available on:
📺 YouTube
Or wherever you get your podcasts!
If you’re looking for practical ways to strengthen your reliability program, tie your CMMS data to real problem-solving, or make RCA easier for your team, let us know! You can message us directly or get in touch with our team here: https://easyrca.com/engage.
#CMMS #Maintenance #Reliability #RootCauseAnalysis #Reliability40 #DigitalTransformation
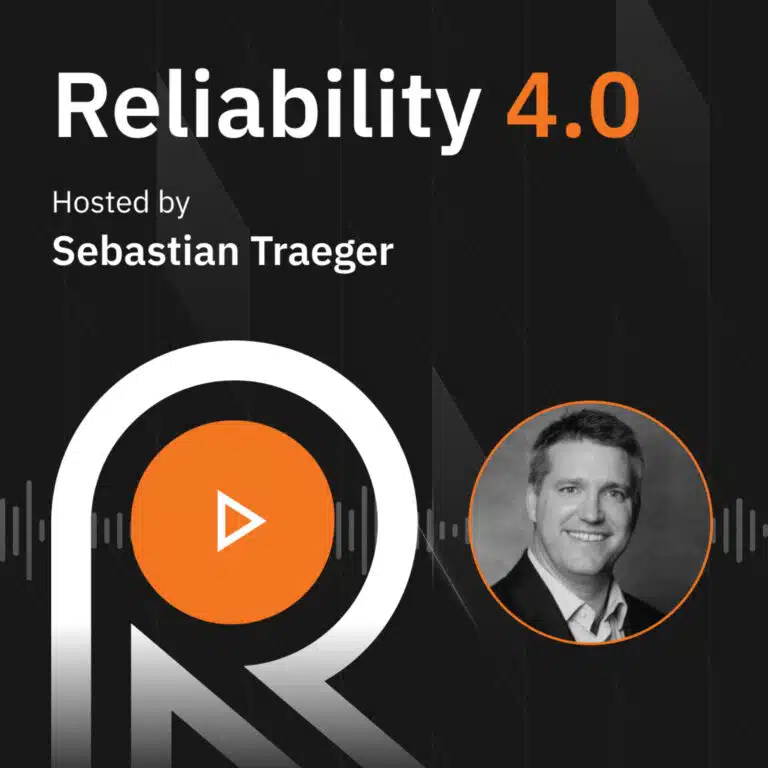

Our PROACT® RCA Methodology
Since its inception in the mid-80’s, our PROACT® methodology has helped hundreds of companies do tens of thousands of successful RCAs, resulting in large financial returns for the business. PROACT® is a robust Root Cause Analysis (RCA) process that can drive incredible business results for your company.